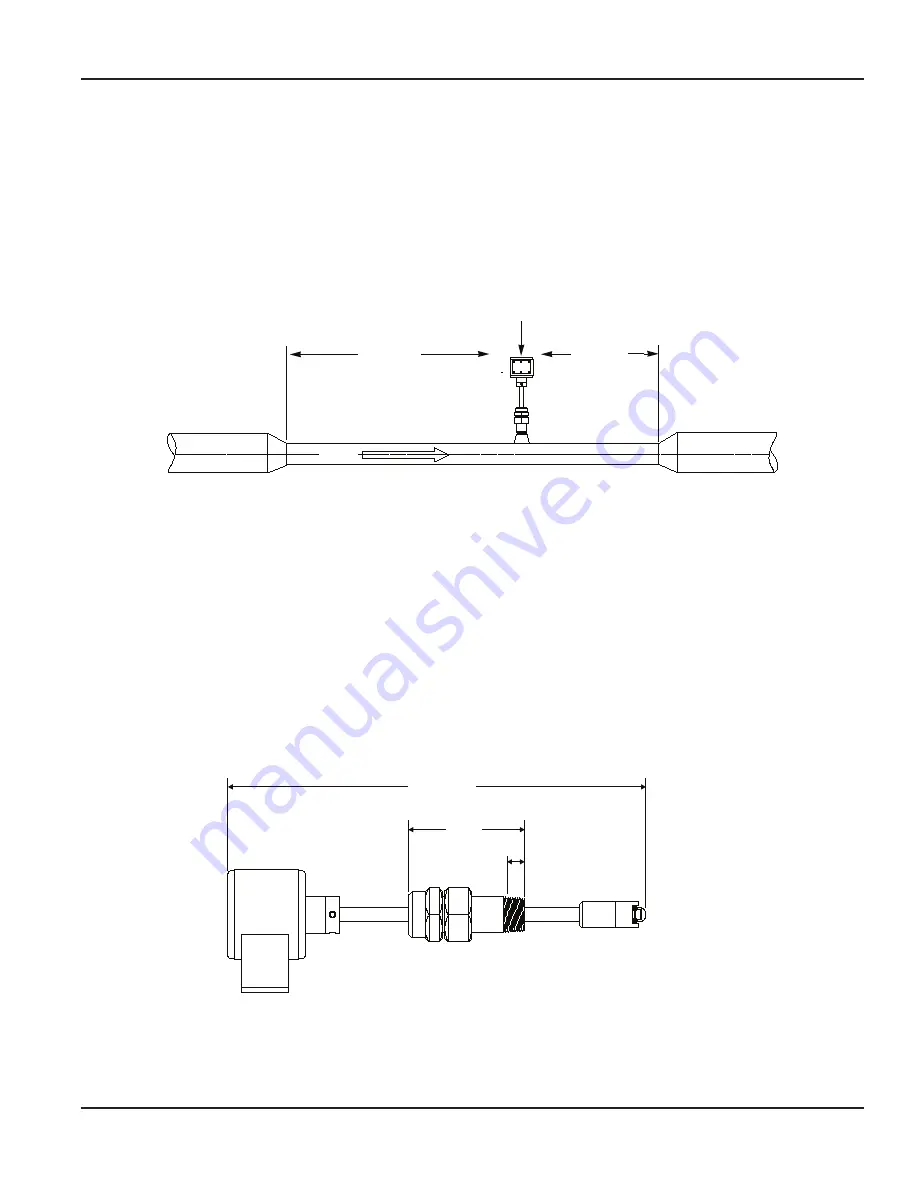
MECHANICAL INSTALLATION
The accuracy of flow measurement for all insert type flow measuring devices is highly dependent on proper location of the
sensor in the piping system . Irregular flow velocity profiles caused by valves, fittings, and pipe bends, can lead to inaccurate
overall flow rate indications even though local flow velocity measurement may be accurate . A sensor located in the pipe that
is partially full or where it can be affected by air bubbles, floating debris, or sediment may not achieve full accuracy and could
be damaged .
Data Industrial flow sensors are designed to operate reliably under adverse conditions, but the following recommendations
should be followed to ensure maximum system accuracy:
5 x Pipe Dia
DATA INDUSTRIAL
SDI Series Sensor
10 x Pipe Dia
FLOW
Figure 2: Minimum recommended straight run distance
1 . Choose a location along the pipe where there is straight pipe for a distance of ten pipe diameters upstream and five pipe
diameters downstream of the sensor . Pipe bends, valves, other fittings, pipe enlargements and reductions or anything else
that would cause a flow disturbance should not be present in this length of pipe .
2 . The recommended tap location around the circumference of a horizontal pipe is on top . If trapped air or debris will
interfere, then the sensor should be located around the pipe from the top preferably not more than 45 degrees from
top dead center . The sensor should never be located at the bottom of the pipe, as sediment may collect there . Locations
off top dead center cause the impeller friction to increase, which may affect performance at low flow rates . Any
circumferential location is correct for installation in vertical pipes .
3 . Insertion depth is critical to accuracy . The algorithm used to convert impeller motion into flow was developed through
flow tests in an independent calibration laboratory . The impeller must be located in the same position in the pipe as it
was in the calibration test for the impeller frequency to accurately describe the same liquid velocity . Detailed installation
instructions on the following pages include methods for ensuring correct insertion depth .
4 . Alignment of the sensor is also important . The impeller shaft must be perpendicular to the flow for accuracy . Alignment
instructions are also included on the following pages .
D1=15 3/4”
D2=19”
4.23”
0.660”
Handtight Enga Wrench Makeup
Per ANSI/ASME B1.20.1-1993, R1992
D1 is for pipe sizes 1½” - 10” *
D2 is for pipe sizes 12” - 36” *
* Pipe sizes are for reference only - Depending on pipe material, tapping
saddle, or existing hardware a longer sensor length may be required,
Consult Factory.
Figure 3: Direct insertion sensor dimensions
Mechanical Installation
Page 7
May 2017
SEN-UM-00217-EN-10