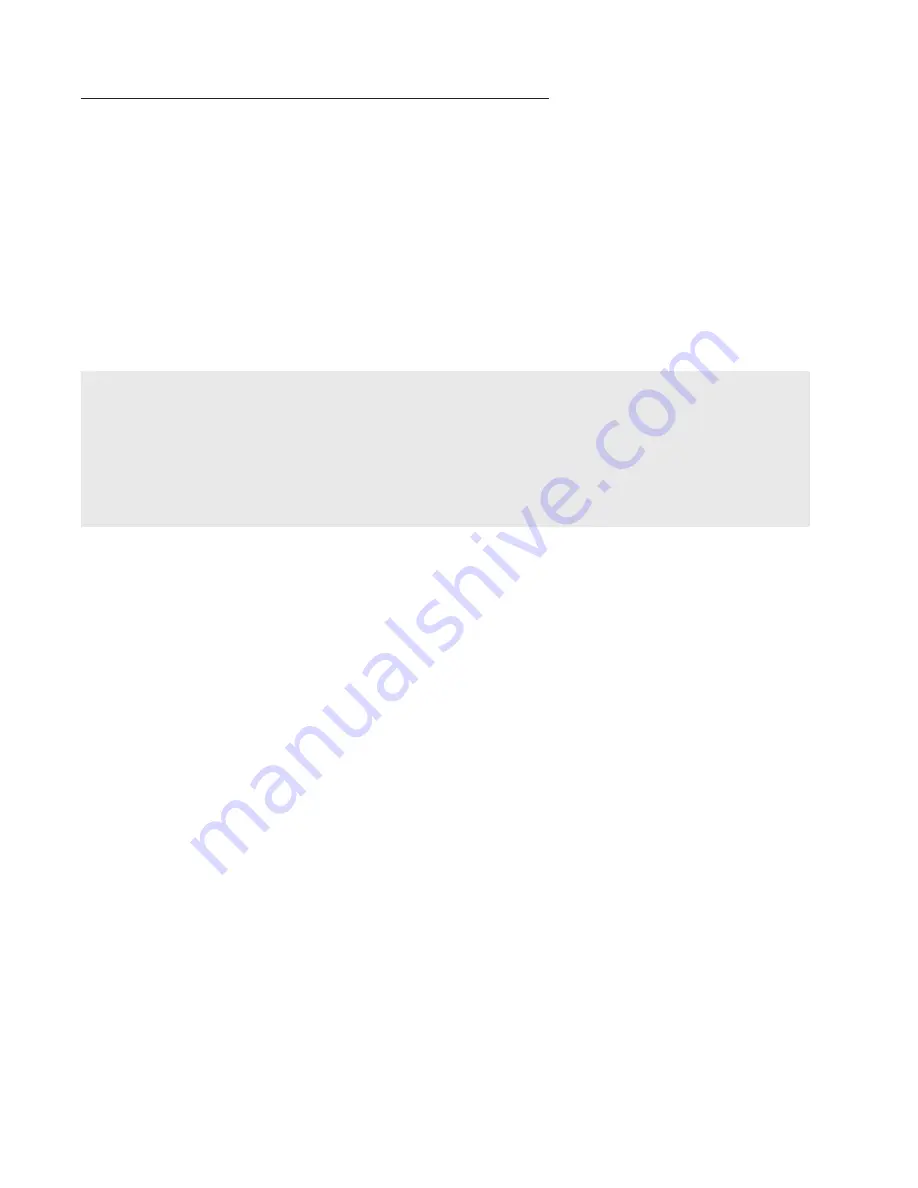
7
© Copyright 2012 Badger Fire Protection
Annual Maintenance & Service Examination Procedures
Per NFPA 10, maintenance is a thorough examination of a fire extinguisher and is intended to
provide maximum assurance that it will operate effectively and safely It includes a thorough
examination of all components and the repair or replacement of such items, if necessary
Maintenance should be performed at intervals not to exceed one year apart or any time an
inspection discrepancy dictates
Badger recommends that only authorized Badger distributors and certified personnel who have
been properly trained to recognize and correct discrepancies, as well as understand all the proper
industry safety procedures, conduct the maintenance or service of Badger fire extinguishers Refer
to the trouble shooting section of this manual for additional information on specific equipment
observations or discrepancies
Only Badger factory replacement parts are recommended for
use in Badger extinguishers.
WARNING:
Prior to servicing or recharging an extinguisher, personnel should be thoroughly
familiar with the contents of this manual to recognize any equipment conditions or
discrepancies that might dictate or prohibit further equipment maintenance or repair.
WARNING:
To prevent injury or death, always ensure all pressure is properly relieved from an
extinguisher prior to attempting any service, repair or recharge.
1 Ensure extinguisher is installed in its proper location and that it is readily accessible (Badger car-
bon dioxide extinguisher models are approved for temperatures indicated on the nameplate)
2 Externally examine unit and cylinder for any signs of damage, dents or corrosion that might
prohibit service or dictate the need for any special maintenance/repair procedures
Ensure cylindar
hydro date is within 5 year requirements
3 Closely examine the extinguisher frame for any damage, corrosion, cracks or deformation
When the extinguisher is tilted on its wheeled axis, service personnel should listen for any
sounds from within the cylinder that might indicate a broken siphon tube or foreign mate-
rial (Refer to Trouble Shooting section)
4 Examine both wheels to ensure they are secure, not damaged and rotate freely Lubricate
as necessary
5 Unthread and remove the discharge hose assembly from the cylinder valve assembly Fully extend
the hose assembly and closely examine the discharge nozzle valve, horn, hose and couplings for
any damage, abrasions, cracking, thread wear or conditions that might affect its proper function
(ON Badger CD-100-1 MODELS) – The agent discharge hose assembly and hose manifold
assembly must both be disconnected and thoroughly examined
6 Examine the discharge nozzle valve for any damage or corrosion and while pointing nozzle in a
safe direction slowly squeeze the lever to verify it operates properly Ensure the nozzle discharge
horn is not damaged, cracked or obstructed and is correct for the model
7 Blow (low pressure) dry air through the discharge hose assembly and nozzle to ensure it is not
plugged or obstructed and operates freely (If hose is obstructed, properly secure hose assembly
and using the proper service kit adaptor, connect a regulated pressure source set no higher than
100 PSI to assist in clearing the hose and nozzle assembly )