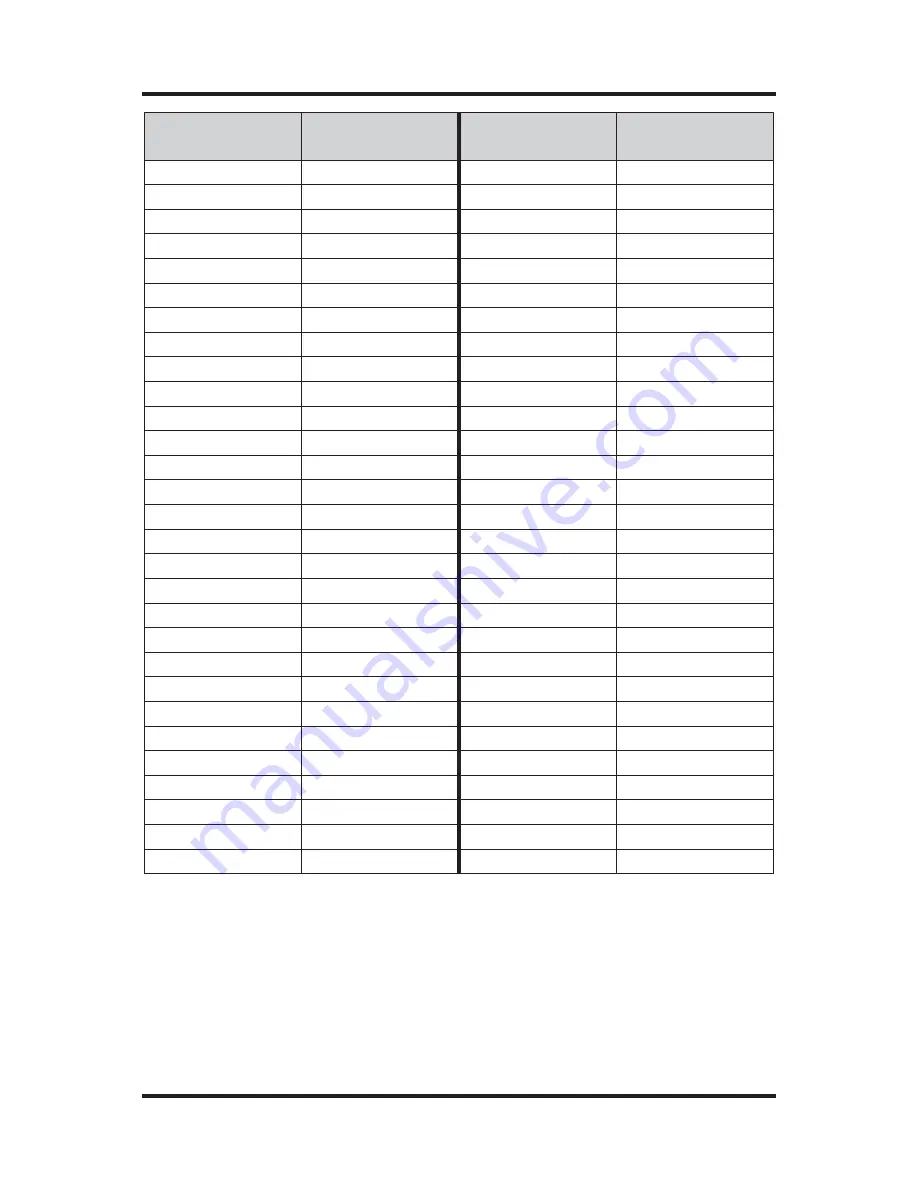
GDC-350 Operation Manual
24
5909-9000
Rev
1
VOLT READING
AT TEST POINTS
TIME DELAY
IN MINUTES
VOLT READING
AT TEST POINTS
TIME DELAY
IN MINUTES
0 V
N/A
0.58 V
2.9
0.02 V
0.1
0.60 V
3.0
0.04 V
0.2
0.62 V
3.1
0.06 V
0.3
0.64 V
3.2
0.08 V
0.4
0.66 V
3.3
0.10 V
0.5
0.68 V
3.4
0.12 V
0.6
0.70 V
3.5
0.14 V
0.7
0.72 V
3.6
0.16 V
0.8
0.74 V
3.7
0.18 V
0.9
0.76 V
3.8
0.20 V
1.0
0.78 V
3.9
0.22 V
1.1
0.80 V
4.0
0.24 V
1.2
:
:
0.26 V
1.3
1.0 V
5.0
0.28 V
1.4
1.2 V
6.0
0.30 V
1.5
1.4 V
7.0
0.32 V
1.6
1.6 V
8.0
0.34 V
1.7
1.8 V
9.0
0.36 V
1.8
2.0 V
10.0
0.38 V
1.9
2.2 V
11.0
0.40 V
2.0
2.4 V
12.0
0.42 V
2.1
2.6 V
13.0
0.44 V
2.2
2.8 V
14.0
0.46 V
2.3
3.0 V
15.0
0.48 V
2.4
3.2 V
16.0
0.50 V
2.5
3.4 V
17.0
0.52 V
2.6
3.6 V
18.0
0.54 V
2.7
3.8 V
19.0
0.56 V
2.8
4.0 V
20.0
Move the jumper on the lower bank (J6) from its resting position (P1) to P4. This is
the system configuration position. Next, select the jumper position on upper bank J7
to achieve the desired function. Reference the table on page 20 for appropriate
jumper position locations.
Once the desired jumper position has been achieved, use the UP or DOWN push-
buttons to make changes. Once the desired time delays have been set, move jumper
back to resting position (P1) of the upper bank (J7). If additional time delays are
desired, move the jumper to the appropriate position and once again use the push-
buttons to set desired voltage to achieve desired time delay.