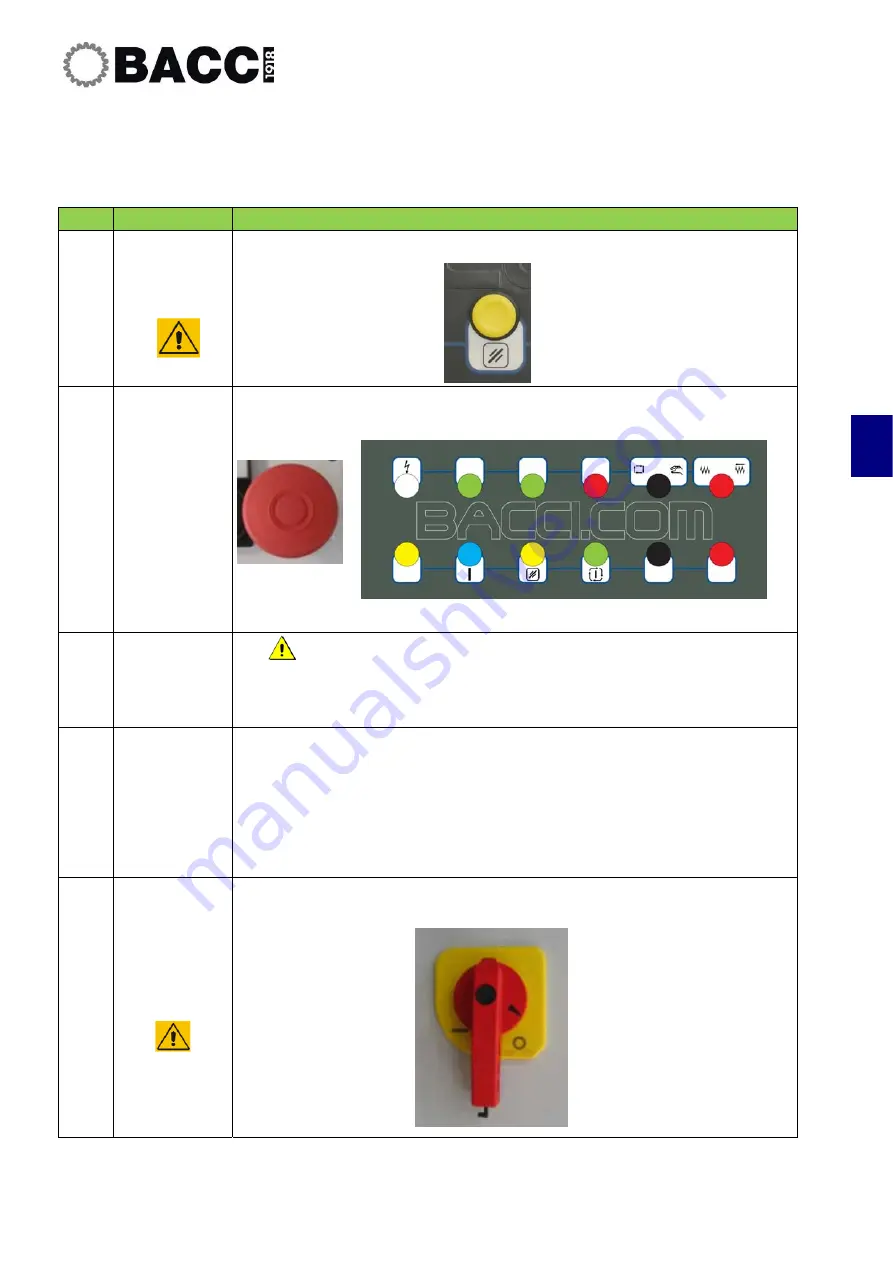
CHAPTER 5 –
Controls and use
Chap. 5
-
21
/48 -
5.4
Machine turn off procedure
To turn off the machine, proceed as described following.
STEP
ACTION
DESCRIPTION
1
Machine
Reset
Press the "Reset" button.
2
Emergency
Pushbutton
Press one of the Emergency pushbuttons located on the pushbutton panels.
3
Exit submenus
•
Exit the submenus of the interface panel and return to the main
page.
4
Turn off
windows
Turn off the Windows operating system:
•
Click on START
•
Click on CLOSE SESSION
•
Click on STOP SYSTEM
•
Click on OK
The following message will appear: “You may now turn off the machine.”
4
Cut-off power
to the
machine.
Turn the main switch to "0"
Summary of Contents for Twin
Page 4: ...TWIN Use and maintenance instruction manual Cap 0 IV 4 Page intentionally left blank ...
Page 5: ...CHAPTER 1 Foreword Chap 1 1 14 CHAPTER 1 Foreword ...
Page 7: ...CHAPTER 1 Foreword Chap 1 3 14 Page intentionally left blank ...
Page 18: ...TWIN Use and maintenance instruction manual Chap 1 14 14 Page intentionally left blank ...
Page 19: ...CHAPTER 2 Safety information Chap 2 1 52 CHAPTER 2 Safety information ...
Page 98: ...TWIN Use and maintenance instruction manual Chap 3 28 28 Page intentionally left blank ...
Page 99: ...CHAPTER 4 Installation Chap 4 1 20 CHAPTER 4 Installation ...
Page 119: ...CHAPTER 5 Controls and use Chap 5 1 48 CHAPTER 5 Controls and use ...
Page 166: ...TWIN Use and maintenance instruction manual Chap 5 48 48 Page intentionally left blank ...
Page 167: ...CHAPTER 6 Maintenance Chap 6 1 32 CHAPTER 6 Maintenance ...
Page 198: ...TWIN Use and maintenance instruction manual Chap 6 32 32 Page intentionally left blank ...
Page 202: ...TWIN Use and Maintenance Instruction Manual Chap 7 4 4 Page intentionally left blank ...