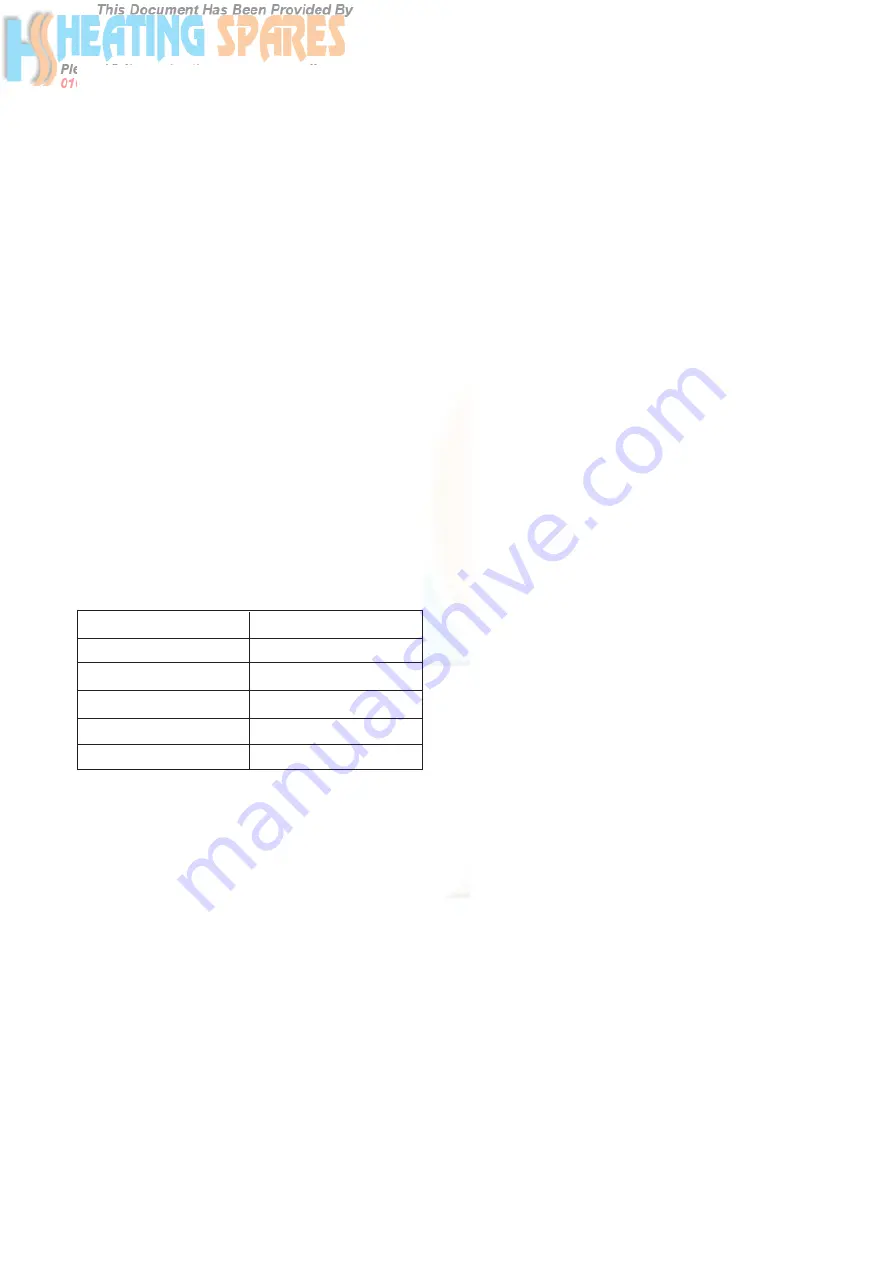
Supplied By www.heating spares.co Tel. 0161 620 6677
7
WATER SYSTEM
IMPORTANT: USE ONLY COMPRESSION FITTINGS
WHEN CONNECTING THE BOILER TO THE CENTRAL
HEATING SYSTEM
The installation must comply with the requirements of the
following codes of practice.
BS 5449 Part 1 Forced Circulation Hot Water Systems.
BS 7074 Part 1 Code of practice for Sealed System
water systems.
BS 7593 Treatment of water in domestic hot water central
heating systems.
The water system must be thoroughly flushed out with
cold water without the pump in position. Refit the pump
and fill the system. Vent all air from system. Clear any air
locks and examine the system for water leaks.
IMPORTANT: ENSURE ALL SERVICE VALVES ARE IN
OPEN POSITION.
Ensure boiler is fitted with flow pipe at top and return
pipe at bottom.
The boiler is supplied with dia 22mm tail pipes top and
bottom for connection to system.
The boiler must be installed using 22mm compression
fittings both top and bottom.
The AZTEC range of boilers are low water content boilers
so require a good flow rate at all times (see chart).
AZTEC boilers are approved for use on fully pumped open
vented systems and sealed systems. When fitting on a
sealed system a 3 bar safety valve must be fitted to system,
where thermostatic radiator valves are fitted it will be
necessary to fit a bypass to obtain min flow rates.
IMPORTANT: IF MIN FLOW RATES ARE NOT
OBTAINED THE BOILER MAY GO TO LOCK OUT ON
HIGH LIMIT THERMOSTAT.
Where more than 1 boiler is fitted refer to multiple boiler
instructions.
System must be flushed out before adding inhibitor to BS
7593: 1992 treatment of water in central heating boiler.
IMPORTANT: THIS BOILER IS TO BE FITTED ON
FULLY PUMPED SYSTEMS ONLY.
SEALED WATER SYSTEM
REQUIREMENTS
The installation must comply with the appropriate
requirements of the current issue of BS4814, BS5449,
BS6798 and BS7074 Part 1 and 2.
THE INSTALLATION ENGINEER MUST BE REGISTERED
AS A COMPETENT UDHWSS INSTALLER.
MODEL
MIN FLOW RATE / Min
AZTEC 2 Kw
4 LTRS
AZTEC 6 Kw
8 LTRS
AZTEC 9 Kw
10 LTRS
AZTEC 11 Kw
11 LTRS
AZTEC 12 Kw
12 LTRS
Safety Valve
A safety valve set at 3 bar must be fitted with the drain
routed to the outside of the building. The drain must not
discharge above an entrance or a window or any public
access area, be clear of any electrical fittings and positioned
so that any discharge can be seen.
Expansion Vessel Capacity
A diaphragm type expansion vessel, conforming to the
current issue of BS4814. The expansion vessel must be
connected to the systems at a point close to the inlet side
of the circulating pump. The expansion vessel volume
depends on the total water system volume and the initial
system design pressure. For any system an accurate
calculation of vessel size is given in the current issue of
BS5449 and BS7074 Part 1.
The water content of the boiler is given in Technical
Specification Note a higher initial design pressure
requires a larger volume expansion vessel.
The charge pressure must not be less than the static
head of the system, that is the highest point of the
system above the expansion vessel.
Capacity of expansion vessel
Where design information is not complete the following
chart (page 8) can be used for selecting the size of the
vessel, it should be noted that the size given in the table
take account of fault conditions.
System Temperature
The normal running temperature of the system is 80°C, if
a fault was to occur then the safety device would allow
the system temperature to rise to 100°C. It is recommended
that this figure be used in the calculations of vessel size.
Connection of the expansion vessel
The expansion vessel should be connected in the neutral
part of the system this being the return pipe work close to
the boiler, refer to sealed system pipework layout
drawing.(Fig. 12)
Pressure Gauge
A pressure gauge must be permanently fitted in the
system covering a range from 0 to 4 bar.
Position where it can be seen when filling system.
Inhibitor
If using an existing system, take care to drain down the
entire system including the radiators then thoroughly
clean out before fitting the boiler.
Attention is drawn to the current issue of BS5449 and
BS7593 on the use of inhibitors in central heating systems
Drain Tapping
A drain tapping must be provided at lowest point of the
system, which will allow the entire system to be drained.
NOTE: Failure to ensure the correct vessel size could
result in premature failure of the expansion vessel
which in turn may adversely effect other components
in the system i.e, circulating pump and diverter valve.
System Makeup
Water loss from the system should be replaced from a
makeup vessel connected to the system. This vessel
should be higher than the top of the system. Alternatively
provision can be made by pre-pressurisation of the system
via a temporary hose connection and through a double
check valve (non-return) and stop valve.
There must be no permanent connection to the mains
water valve supply even through a non return valve.