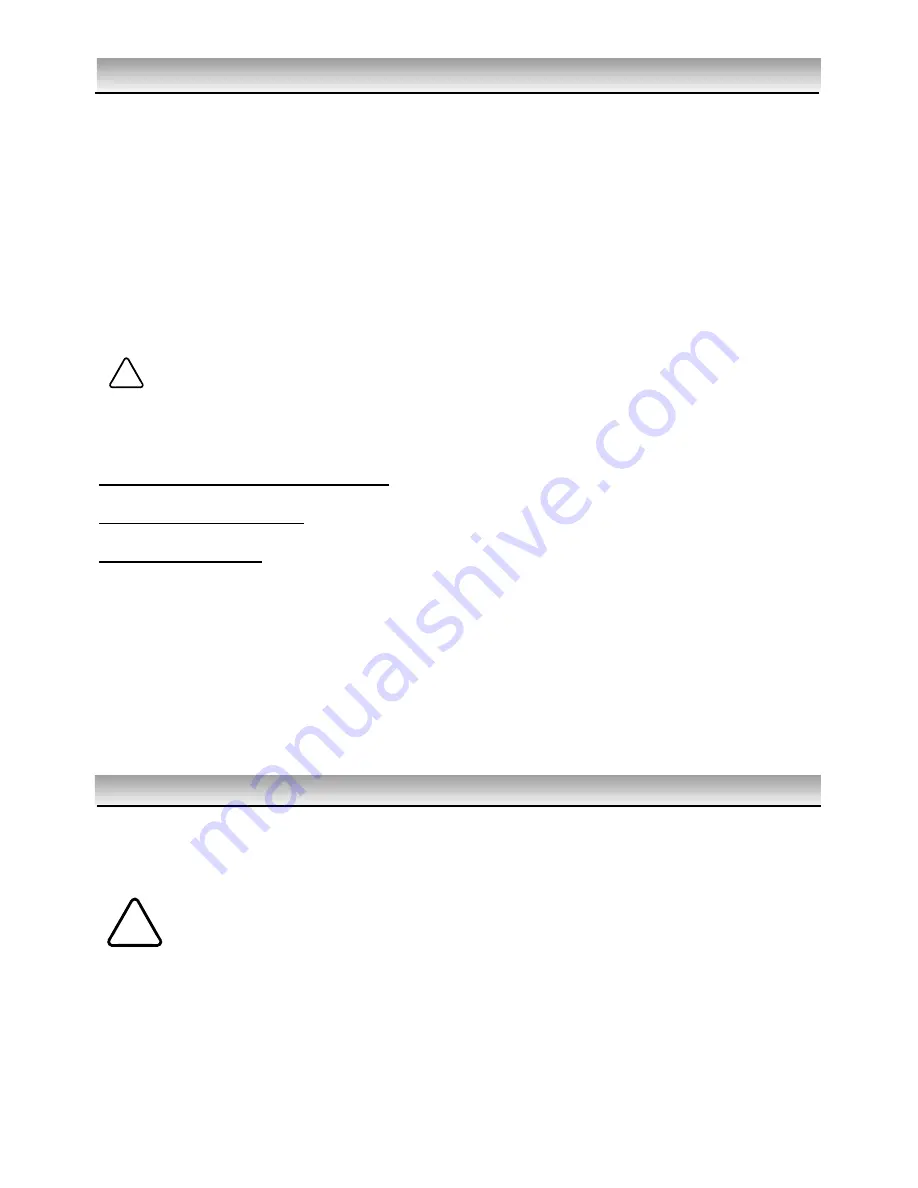
Good Working Practices/Safety
The following suggestions will enable you to observe good working practices, keep yourself and fellow
workers safe and maintain your tools and equipment in good working order.
WARNING!! KEEP TOOLS AND EQUIPMENT OUT OF THE REACH OF YOUNG CHILDREN
Work Place/Environment
The machine is not designed for working outside, do not use when or where it is liable to get wet. If the
machine does get wet; dry it off as soon as possible, with a cloth or paper towel. Do not use 240Va.c.
powered machines anywhere within a site area that is flooded or puddled, and do not trail extension cables
across wet areas. Keep the machines clean; it will enable you to more easily see any damage that may
have occurred. Clean the machine with a damp soapy cloth if needs be, do not use any solvents or
cleaners, as these may cause damage to any plastic parts or to the electrical components.
General Instructions for 240v Machines
!
04
Initial Actions
Having unpacked your machine and its accessories, please check the contents against the
equipment list ”What’s in the box”, if there are any discrepancies, please contact Axminster
Power Tool Centre using the procedures laid down in the catalogue. Please dispose of the
packaging responsibly; much of the material is bio-degradable. The machine and its accessories
will arrive coated with heavy corrosion preventative grease and greased wax paper. These will
need to be cleaned from the machine, its components and accessories prior to it being set up
and commissioned. Use coal oil, paraffin or a proprietary degreaser to remove the barrier grease.
Be warned, it will stain if you splash it on clothing etc.; wear overalls, coverall et al., rubber
gloves are also a good idea, as is eye protection if your cleaning process tends to be a little bit
enthusiastic. After cleaning, lightly coat the exposed metal surfaces of the machine with a thin
layer of light machine oil. N.B If you used paraffin/kerosene make sure you apply this thin film
sooner rather than later.
Please read the Instruction Manual prior to using your new machine; as well as the
installation procedure, there are daily and periodic maintenance recommendations to
help you keep your machine on top line and prolong its life. Keep this Instruction Manual
readily accessible for any others who may also be required to use the machine.
Work Place/Environment/Installation
Mains Powered Machines
Primary Precautions
These machines are supplied with a moulded 13 Amp. Plug and 3 core power cable. Before
using the machine inspect the cable and the plug to make sure that neither are damaged. If any
damage is visible have the machine inspected/repaired by a suitably qualified person. If it is
necessary to replace the plug, it is preferable to use an ‘unbreakable’ type that will resist
damage. Only use a 13 Amp plug, make sure the cable clamp is tightened securely. Fuse at 13
Amp. If extension leads are to be used, carry out the same safety checks on them, and ensure
that they are correctly rated to safely supply the current that is required for your machine. It is
also recommended that the power supply outlet is the switched type, and that the supply is
switched off whilst plugging in, or unplugging the machine.
!