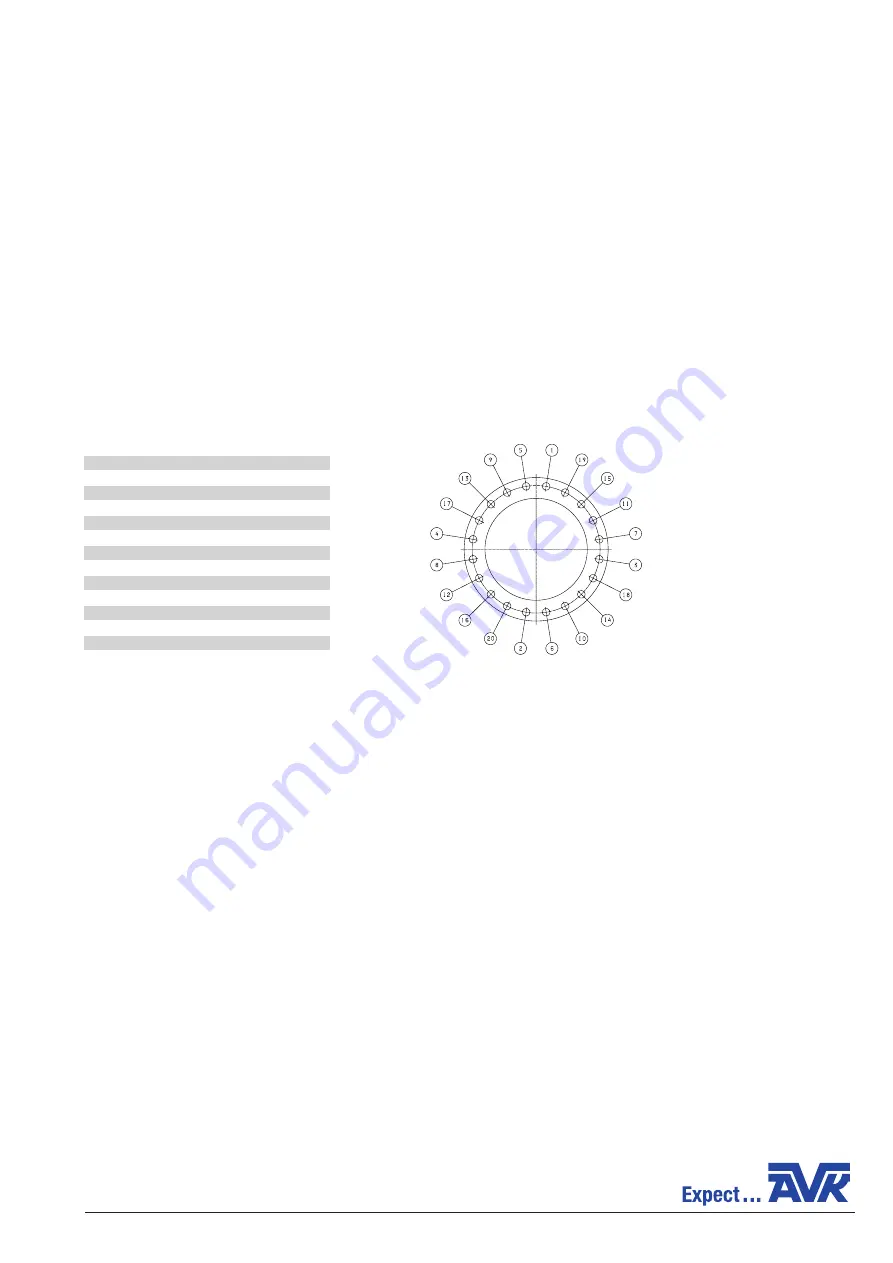
INSTALLATION AND MAINTENANCE INSTRUCTIONS - ORIGINAL VERSION
AVK GATE- AND SERVICE CONNECTION VALVES FOR GAS
SERIES 02, 03, 06, 36, 38 and 46
Parallel alignment of flanges is especially important in the case of the assembly of a valve into an existing system.
The bolting used for the flange connection must be checked for correct size, length, material and that all connection flange bolt
holes are utilised. See table 1 for bolt sizes.
If a permanent extension spindle and road cover is used only a permanent telescopic extension spindle that is not completely
collapsed (shall be extracted e.g. min. 50 mm) shall be used to avoid transfer any loads to the buried valve.
Gate valves with spigot pipe ends are to be installed either by means of appropriate welding or the use of a suitable coupling.
For welding procedures please refer to pipe manufacturers’ specifications.
For choice of coupling please consult an AVK representative.
Special care shall be taken when installing gate valves with purge points. The purge point pipes shall be protected from any
sideway loads, both during handling and after installation.
13. OPERATION
Gate valves are typically operated with an extension spindle in below ground installations. In manholes or in above ground
installations handwheels or electric actuators may be used. Ensure proper sizing of the handwheel and/or operating keys,
extension spindles and actuators. Please refer to AVK datasheets for further information. When installing gate valves mounted
with electric actuators, please observe closing torques and number of turns from the datasheet. When the valve is installed
in a chamber with an extension spindle going to above ground level, ensure that no vertical force from the extension spindle
presses down directly on the valve stem top. The extension spindle must be supported by wall mounts or similar to prevent
vertical forces and thereby supporting the weight of the extension spindle.
When closing the gate valve ensure that the appropriate torque and number of turns are applied to the valve. See table 2.
14. PRESSURE TESTING
After installation, perform a pressure test before the trench is closed. Secure the pipe and gate valve against movement. If the
pipeline and valve are tested with water prior to gas/air tests, ensure that the pipeline and valve are drained to prevent frost
damage. AVK valves are designed to resist a test pressure of 1.5 x PN.
15. MAINTENANCE
The valve is designed to give long trouble free service without the need of routine maintenance.
After the specified number of operation cycles have been reached the wear inside the valve shall be examined. If the wear is
extensive, worn components shall be replaced or a new valve shall be installed.
If internal or external leakage is suspected, it is recommended that AVK International be contacted to suggest suitable remedial
action.
Page 5/8
MI GateValvesGas Rev. N June 2019 GB
BOLT SIZES
DN Working pressure (bar)
Quantity
mm
PN 10 PN 16
PN 10 PN 16
40
M16
M16
4
4
50
M16
M16
4
4
65
M16
M16
4
4
80
M16
M16
8
8
100
M16
M16
8
8
150
M20
M20
8
8
200
M20
M20
8
12
250
M20
M24
12
12
300
M20
M24
12
12
350
M24
M24
16
16
400
M24
M27
16
16
450
M24
M27
20
20
500
M24
M30
20
20
600
M27 M30
20 20
Table 1
Figure 1