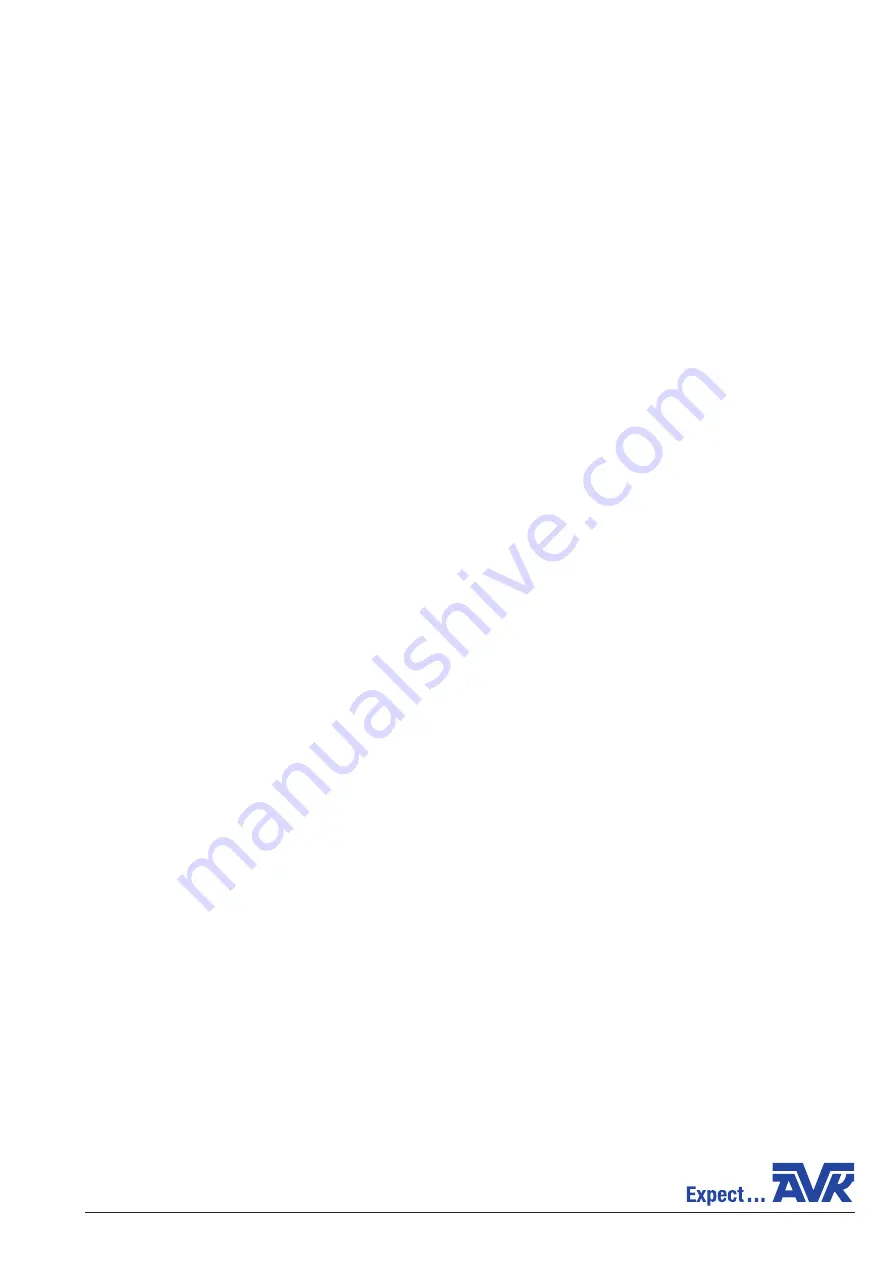
INSTALLATION AND MAINTENANCE INSTRUCTIONS - ORIGINAL VERSION
AVK GATE- AND SERVICE CONNECTION VALVES FOR GAS
SERIES 02, 03, 06, 36, 38 and 46
Page 4/8
MI GateValvesGas Rev. N June 2019 GB
11. LAYOUT AND SITING
It should be considered at the design stage where valves will be located to give access for operation, adjustment, maintenance
and repair.
Valves must be provided with adequate support. Adjoining pipework must be supported to avoid the imposition of pipeline
strains on the valve body, which would impair its performance.
The valve shall be installed in piping systems designed with compensators according to standard practice and norms designed
to absorb axial pipe movements due to temperature expansion or contraction.
A heavy valve may need independent support or anchorage.
If the valve is installed in rock or sharp-edged stone, there shall be a bed of earth, sand or other suitable material to a minimum
depth of 150 mm beneath the valve. Fine-grade (< 5 mm) material free from sharp-edged stones shall be filled and compacted
carefully around the side of the valve and to a minimum consolidated height of 150 mm above the valve.
12. INSTALLATION
Prior to installation, a check of the valve labelling and marking must be made to ensure that the correct valve is being installed.
Record the valve serial number and its location to help with traceability.
The valve shall be handled with great care not damaging the coating to avoid the risk of external corrosion.
Extra care shall be taken to make sure outside coating is intact or the use of other means of additional protection shall be used
when the valve is installed in polluted or aggressive soil conditions or coastal environments. Alternatively, the frequency of
inspections shall be increased to detect any corrosion.
Before installing and commissioning the valve shall be examined for damaged coating. If the coating is damaged repair is re-
quired. AVK can supply a coating repair kit.
The valve should be fully opened and closed to ensure it is operating satisfactorily.
Valves are precision manufactured items and as such, should not be subjected to misuse such as careless handling or allowing
dirt to enter the valve through the end ports.
Excessive forces during installation and operation must be avoided.
All special packaging materials must be removed.
When valves are provided with lifting lugs or eye nuts, these should be used to lift the valve. These lugs are designed to take
the weight of the valve only and not any attached pipe work etc. Valves should not be lifted using the handwheel, stem, gear-
box, actuator or by the purge pipes (only applicable for the AVK valves with purge points). During lifting all applicable Health &
Safety requirements should be observed.
Immediately prior to valve installation, the pipework to which the valve is fastened should be checked for cleanliness and free-
dom from debris.
Valve end protectors should only be permanently removed immediately before installation. The valve interior should be inspect-
ed through the end ports to determine whether it is clean and free from foreign matter.
The mating flanges (both valve and pipework flanges) should be checked for correct gasket contact face, surface finish and
condition. If a condition is found which might cause leakage, no attempt to assemble should be made until the condition has
been corrected.
The gasket should be suitable for operation conditions or maximum pressure/temperature ratings and should be checked to
ensure freedom from defects or damage.
Care should be taken to provide correct alignment of the flanges being assembled. It is important when installing any valve that
pipeline stresses are kept to a minimum and no undue external forces are placed on the valve connections. During assembly,
the bolts must be tightened sequentially to make the initial contact of flange and gasket flat and parallel followed by gradual
and uniform tightening to the specified torque for the gasket being used in an opposite bolting sequence to avoid bending one
flange relative to the other, particularly on flanges with raised faces. See figure 1 for bolt tightening pattern.