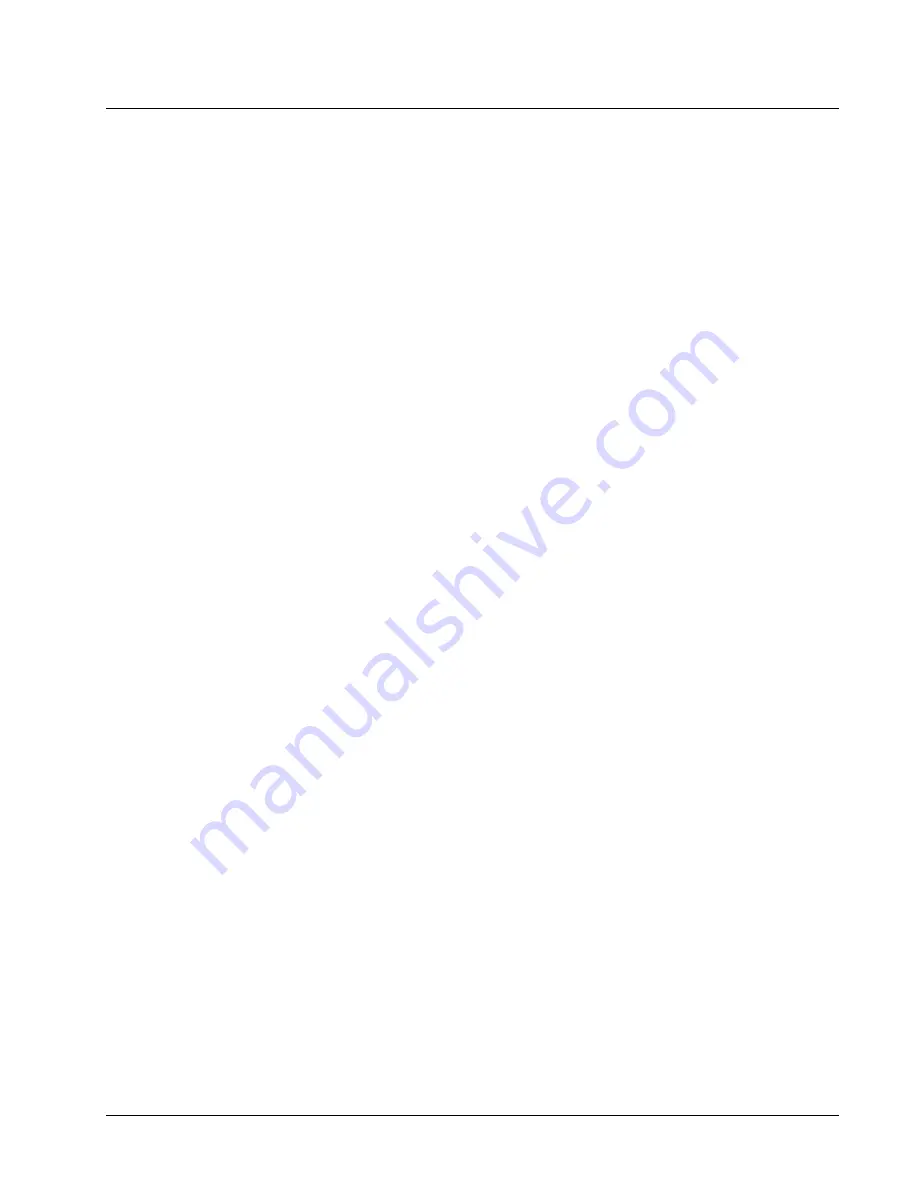
User Manual Model 676 LOKPRINT®
Maintenance
•
••
•
39
Lubrication Procedure
General
The 676 series printers are factory equipped with either composition bearings not
requiring lubrication, pre-lubricated bronze bearings, or pre-lubricated needle
bearings. Periodic cleaning of the printer and removal of dust will greatly enhance
the length of the time the printer will function.
Composition (Iglide) Bearings
1) If field replacement of an assembly fitted with a plastic bearing is performed, a
single drop of spindle oil should be applied to assist in bearing break-in.
2) If, after long use, a plastic bearing starts to "squeak", disassemble the component
containing the bearing and lightly abrade the shaft surface. Clean the bearing
(dust or old oil) with alcohol, re-lubricate with 1 drop of light oil and reassemble.
No other printer lubrication should be required in normal use.
Summary of Contents for LOKPRINT 676
Page 2: ...User Manual Model 676 LOKPRINT This page intentionally blank...
Page 6: ......
Page 10: ...4 Description Specifications User Manual Model 676 LOKPRINT...
Page 63: ...User Manual Model 676 LOKPRINT Mechanical Assembly Drawings 57 Mechanical Assembly Drawings...
Page 64: ...58 Mechanical Assembly Drawings User Manual Model 676 LOKPRINT Unwind Assembly Drawing...
Page 66: ...60 Mechanical Assembly Drawings User Manual Model 676 LOKPRINT Web Guide Assembly Drawing...
Page 68: ...62 Mechanical Assembly Drawings User Manual Model 676 LOKPRINT Drive Assembly Drawing...
Page 70: ...64 Mechanical Assembly Drawings User Manual Model 676 LOKPRINT Top Printhead Assembly Drawing...
Page 79: ...User Manual Model 676 LOKPRINT Mechanical Assembly Drawings 73...