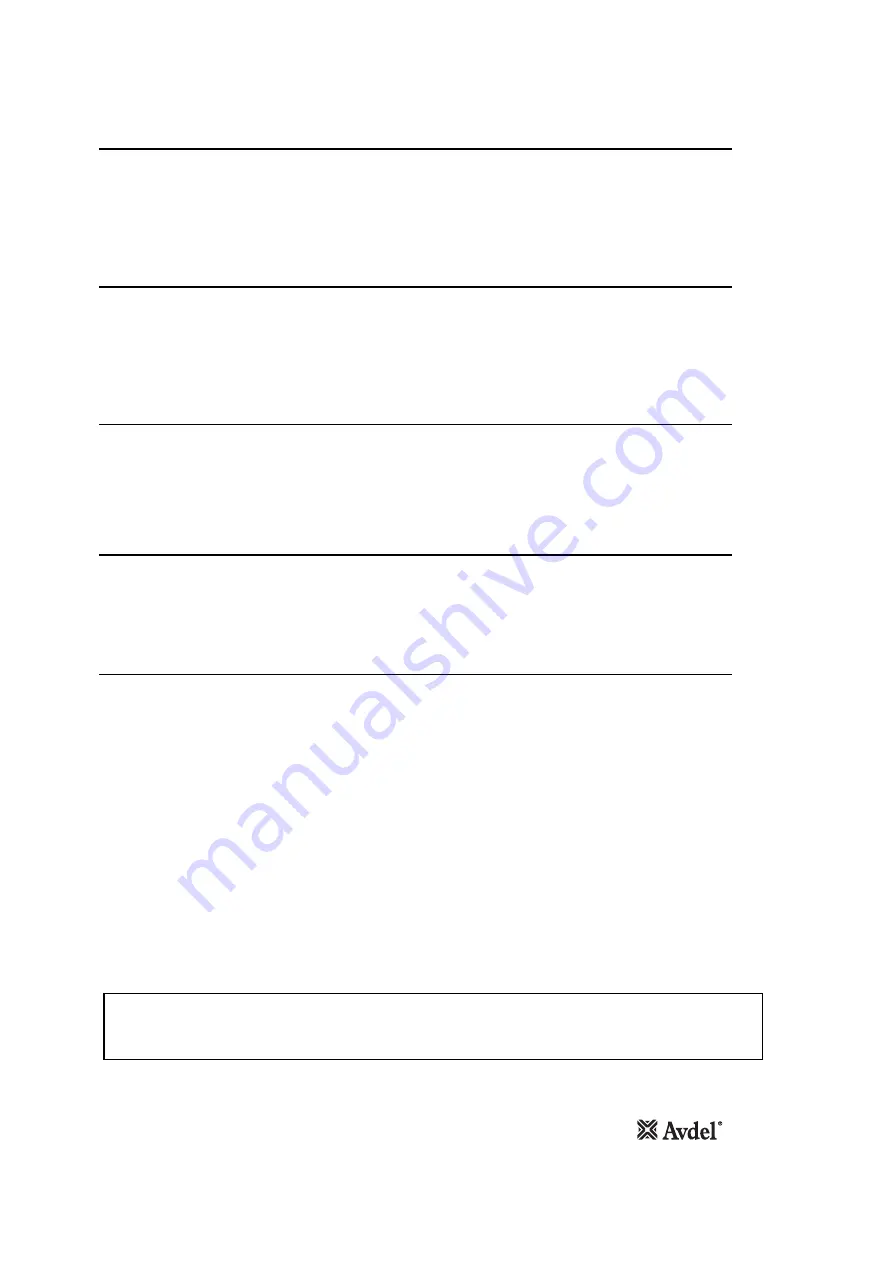
D i f f e r e n t i a l Va l v e
H e a d A s s e m b l y
R e a r C a s i n g
D i s t r i b u t o r
H y d r a u l i c P i s t o n & A i r M o t o r A s s e m b l y ( 7 4 2 0 0 - 1 2 6 1 0 )
M a i n t e n a n c e
13
•
Wrap adhesive tape around hydraulic piston
54
thread and move assembly backwards slowly and firmly. Using circlip pliers* remove
circlip
52
and front seal
51
.
•
Remove ‘O’ rings
76
and
77
.
•
Using two spanners* separate the hydraulic piston
54
from air motor casing
75
. Shim adjustment ring
55
, movement pivot
56
and
‘O ring
101
will come out with hydraulic piston
54
.
•
Remove air motor assembly out of air motor casing
75
, remove circlip
61
using circlip pliers*, then tap air motor casing
75
on bench to
free components.
•
Parts
62
to
74
can be pulled out as an assembly, taking care not to drop pin
74
.
•
Remove bearing
62
, planet gear spindle
63
, three planets
64
, planet gear
65
and spacer
66
.
•
Using a soft mallet tap splined head of rotor
70
.
•
Bearing
67
and front end plate
68
will come out with stator
69
and five rotor blades
71
. (rotor
70
remains in hand).
•
Place rear end plate
72
in vice with soft jaws.
•
Using a pin punch* tap centre of rotor
70
to remove bearing
73
. (turn rotor
70
upside down and bearing
73
will come out).
•
When assembling air motor, rear side of rotor
70
must just touch rear end plate
72
without any axial gap, (any existing gap will disappear
when bearing
73
is fully located.
•
When inserting air motor into air motor casing
75
carefully align parts so that pin
74
locates in centre hole between spin on/off ports of
air motor casing
75
and rear end plate
72
.
•
When assembling hydraulic piston
54
onto air motor assembly, tighten parts by hand and blow air into one of the outer ports of air motor
casing
75
, checking to see air motor rotates freely.
•
When assembling front seal
51
ensure larger diameter faces rear of tool.
•
Complete assembly in reverse order to dismantling.
* Refers to items included in the 74200 service kit. For complete list see page 11.
Item numbers in
bold
refer to the General Assembly drawing and parts list (pages 14-15).
I M P O R T A N T
Check the tool against daily and weekly servicing.
Priming is ALWAYS necessary after the tool has been dismantled and prior to operating
•
Using special flat spanner* unscrew valve locking plug
27
, withdraw and remove spring
104
and ‘O’ ring
29
.
•
Remove silencer
34
using a spanner* and remove nylon washer
33
.
•
Push valve piston
28
out from its housing together with ‘O’ rings
30
,
31
&
32
.
•
Check spring
104
for distortion and renew if required.
•
Assemble in reverse order of dismantling.
•
Remove nose equipment prior to commencing dismantling.
•
Using spanners* remove spindle
44
and locknut
45
.
•
Remove return spring locknut
46
using a spanner*.
•
Remove return spring
47
, washer
99
and locking ring
90
.
•
Check return spring
47
for distortion and renew if required.
•
Assemble in reverse order of dismantling.
•
Using an Allen key* remove screw
40
from stroke set finger
88
and lift off bridge washer
95
.
•
Disengage stroke set finger
88
by pushing it back against spring
89
.
•
Unscrew rear casing
86
.
•
Remove rear casing rubber band
87
if necessary.
•
Extract circlip
84
using circlip pliers* and remove sintered silencer
85
.
•
Complete assembly in reverse order of dismantling. Locate pawl
102
in head before screwing on rear casing
86
.
•
Using an Allen key* remove two screws
40
.
•
Withdraw distributor
83
together with air motor end plug
81
and ‘O’ rings
82
&
31
taking care not to drop ball
79
and push rod
78
.
•
Using an Allen key* remove four countersunk socket head screws
58
and withdraw stroke stop
57
.
•
Pull out two air supply tubes
59
and four ‘O’ rings
60
.
•
Assemble in reverse order of dismantling.
Summary of Contents for 74200
Page 18: ......
Page 21: ...Instruction Manual Original Instruction Threaded Insert Power Tool 74200...
Page 22: ......