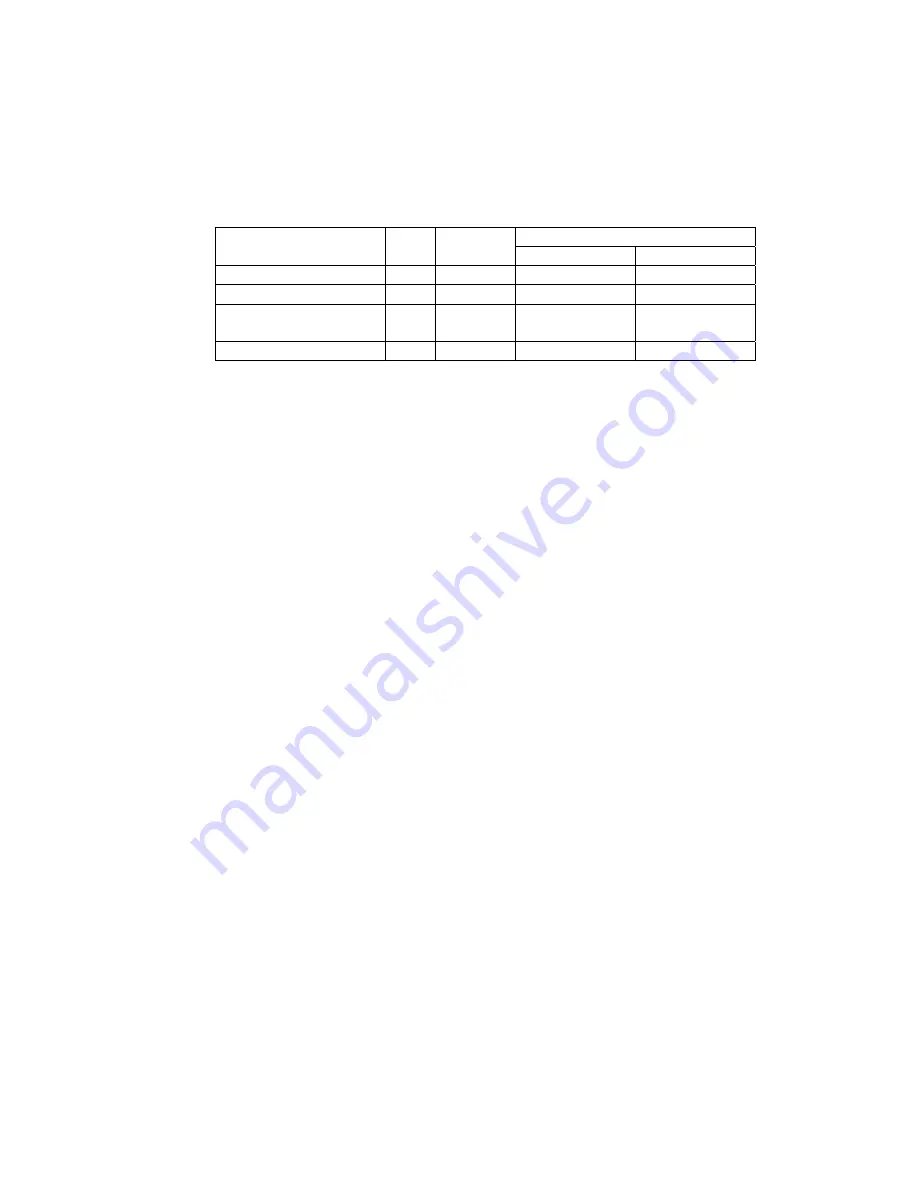
C) Receive error.
C) Receive error.
C) Receive error.
C) Receive error.
(1) Check timing :
When receiving the data from host. (LAN connection)
(2) How to check :
By detecting framing or parity error during internal processing of data.
(3) Cause of the error :
LAN setting does not match to host computer.
(4) How to recover :
LCD
How to recover
Beep
sound
ERROR
LED status
Upper Lower
Error detection
ON
ON
E60 LAN
Receive error
Press any button down
OFF
ON
E60 LAN
Receive error
Press ‘PAUSE’ button
down
OFF OFF
PAUSE
Turn power switch again. OFF
OFF
READY