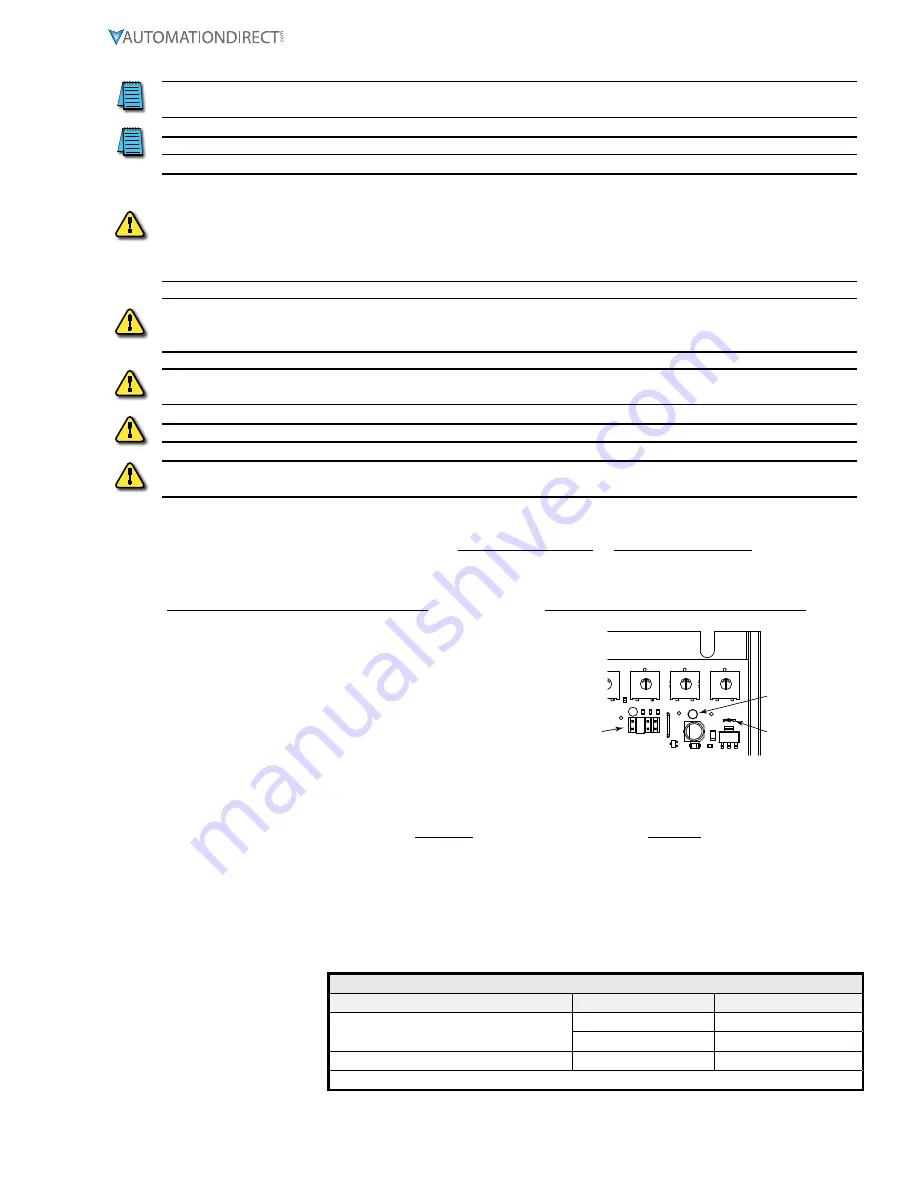
Page 7
IronHorse GSD1 DC Drives User Manual – 2nd Edition, Revision B – 10/12/2018
i
nSTallaTion
anD
W
irinG
Install open-frame drives in an enclosure with a volume at least three times the volume of the open-
frame drive.
Do not mount controller where ambient temperature is outside the range of -10 to 45 °C (14–13 °F).
I
mpRopeR
INstAllAtIoN
oR
opeRAtIoN
of
thIs
dc d
RIve
mAy
cAuse
INjuRy
to
peRsoNNel
oR
dRIve
fAIluRe
. t
he
dRIve
must
be
INstAlled
IN
AccoRdANce
WIth
locAl
,
stAte
,
ANd
NAtIoNAl
sAfety
codes
. m
Ake
ceRtAIN
thAt
the
poWeR
supply
Is
dIscoNNected
befoRe
AttemptING
to
seRvIce
oR
Remove
ANy
compoNeNts
!!! I
f
the
poWeR
dIscoNNect
poINt
Is
out
of
sIGht
,
lock
It
IN
dIscoNNected
posItIoN
ANd
tAG
It
to
pReveNt
uNexpected
ApplIcAtIoN
of
poWeR
. o
Nly
A
quAlIfIed
electRIcIAN
oR
seRvIce
peRsoNNel
should
peRfoRm
ANy
electRIcAl
tRoubleshootING
oR
mAINteNANce
. A
t
No
tIme
should
cIRcuIt
coNtINuIty
be
checked
by
shoRtING
teRmINAls
WIth
A
scReWdRIveR
oR
otheR
metAl
devIce
.
b
efoRe
AttemptING
to
WIRe
the
dc d
RIve
,
mAke
suRe
All
poWeR
Is
dIscoNNected
. R
echeck
code
desIGNAtIoN
to
AssuRe
pRopeR
voltAGe
Is
pReseNt
foR
the
dc d
RIve
. c
AutIoN
should
be
used
IN
selectING
pRopeR
WIRe
sIze
foR
cuRReNt
ANd
voltAGe
dRop
;
mINImum
WIRe
sIze
14AWG
foR
10
Amp
models
ANd
12AWG
foR
20
Amp
models
.
d
o
Not
ReveRse
posItIve
ANd
NeGAtIve
bAtteRy
/
poWeR
leAds
,
As
thIs
WIll
dAmAGe
the
dc d
RIve
.
t
o
chANGe
motoR
dIRectIoN
,
INteRchANGe
the
posItIve
ANd
NeGAtIve
motoR
ARmAtuRe
leAds
.
cAutIoN!! t
uRN
poWeR
off
WhIle
mAkING
WIRING
coNNectIoNs
.
cAutIoN!! s
et
the
voltAGe
selectIoN
jumpeR
to
mAtch
the
supply
voltAGe
. A
N
INcoRRect
jumpeR
settING
WIll
Not
cAuse
dAmAGe
to
the
dRIve
,
but
WIll
Affect
oveRAll
speed
,
mAxImum
speed
ANd
IR
compeNsAtIoN
AdjustmeNts
.
f
UsinG
Externally fuse the +Battery input line with Littlefuse 314 series or Bussman ABC series or equivalent
fuses designed for use with motors and motor control systems; rated for the lesser of:
1) 200% of the continuous current rating of the drive, or 2) 150% of the motor full-load current.
(Fast-blow fuses are NOT recommended
.
) (AutomationDirect sells ABC series fuses.)
c
Urrent
l
iMit
s
ettinG
anD
c
Urrent
l
iMit
(t
riP
) O
UtPUt
48V
36V
24V
12V
Voltage
Selector
Jumpers
Current Limit
Trip Output LED
Current Limit
Trip Output
Please note the following recommendations
regarding the Current Limit (Trip) Output and Setting:
•
The Current Limit Output can be used to inhibit the
drive or break the power connection to the drive�
•
The Current Limit Output threshold is the same as
the Current Limit Setting�
•
To properly adjust the CURRENT LIMIT Setting, a DC ammeter should be placed in series with the
armature line� This meter can be removed after the DC Drive is adjusted�
•
The Current Limit Output is immediate, without time delay, and is NOT retentive�
•
Use with 12VDC relay� In order to maintain a current limit fault, use a latching relay�
•
Source voltage from terminal P2-1�
•
Current Limit Trip Output sinks to terminal P2-4 (50VDC@0�3A)�
•
Recommended use with Inhibit, terminals P2-4 and P2-5�
•
If you connect the current limit relay to the Pot HI (P2-1), supply voltage will be 10V, regardless of the
supply voltage to the drive� If the relay is connected to the supply voltage, the relay voltage needs to
match the supply voltage� The Current Limit Output is capable of up to 100V�
t
erMinal
b
lOcks
GSD1 Wiring Terminals
Type
Wire Range*
Tightening Torque
Barrier terminal block (P1) (Power)
14 – 28 AWG (10A)
7�0 lb·in [8�0 kg·cm]
10 – 14 AWG (20A)
8�5 lb·in [9�8 kg·cm]
Barrier terminal block (P2)
14 – 28 AWG
7�0 lb·in [8�0 kg·cm]
* Wire range of the terminal. See Installation and Wiring above for minimum wire sizes.