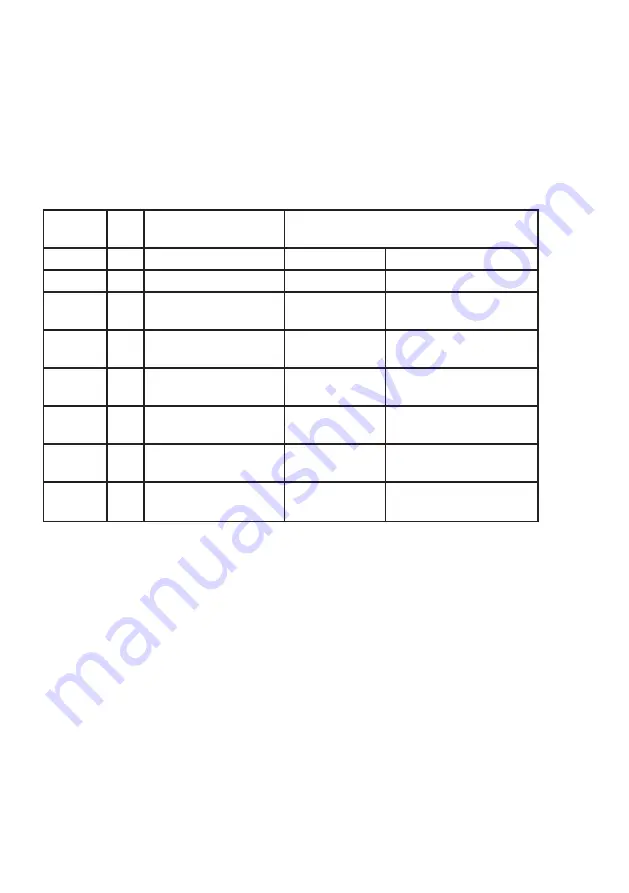
13
AA702
Terminal
Default Function
Assignment
Alternative Function Assignment
BATT (-)
Ground
BATT
(+)
Positive
OUT 1
(+)
1
Windlass
Down
Power Enable when
dual thrusters selected
OUT 2
(+)
1
Windlass
Up
OUT 3
(+)
2
Thruster A (Bow)
Port
Windlass
Option A
OUT 4
(+)
2
Thruster A (Bow)
Starboard
Windlass
Option B
OUT 5
White
(+)
2
Thruster B (Stern)
Port
Power Enable
3
Rope/Chain
Motor Load Wires
OUT 6
Brown
(+)
2
Thruster B (Stern)
Starboard
Dual Speed
3
Rope/Chain
Motor Load Wires
2.4.1 BASE STATION INTERNAL CONNECTIONS
Notes:
Unused outputs are automatically assigned as auxiliary outputs. See Pages 25 and 29
for more details. All outputs are active high (+).
1
Only one windlass can be connected to a base station. 2 windlasses require 2 base
stations. The windlass outputs OUT1 and OUT2 are fixed, however, the
control buttons for up and down can be swapped in the set up menu as can the
location of the windlass (bow or stern).
2
Stern and bow thruster output locations stated are the default locations. These can
be swapped in the set up menu. The port and starboard directions for each output
cannot be changed.
3
Only required for rope/chain counting
OUT 5 = White Motor Load Wire
OUT 6 = Brown Motor Load Wire
The AA710 kit has one master base station and one remote console.
Each base station has 6 outputs. Up to 2 slave stations can be attached to the master
station to provide extra outputs.
2.4 REMOTE CONSOLE AND BASE STATION INSTALLATION
Summary of Contents for AA702
Page 1: ......
Page 57: ... Check out the collection of anchors and docking we offer ...