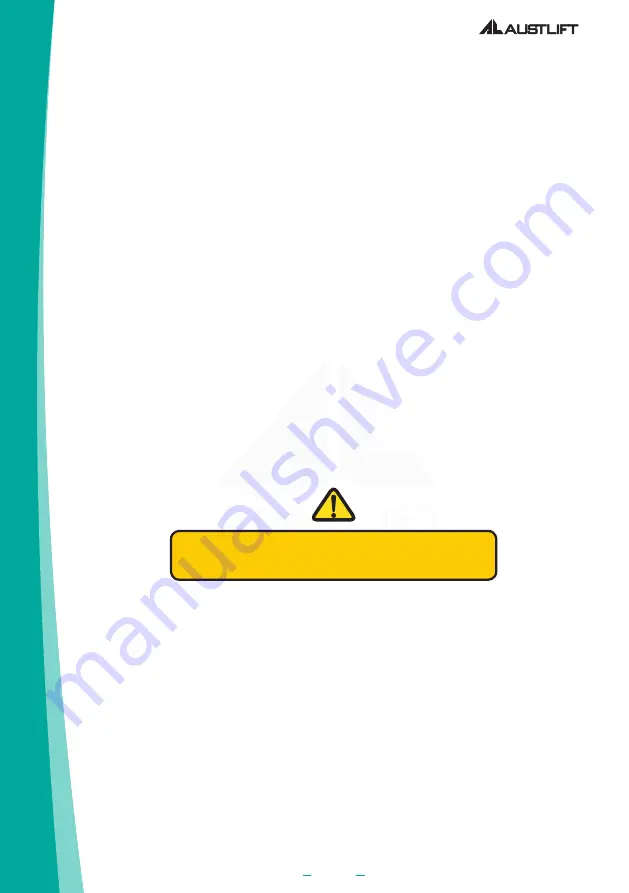
10
ALC UIM HPC-1/UPC-1 11320xx_19
Australian Lifting Centre
USER INS
TRUCTION MANU
AL
LIFTING PLA
TE CLAMP
HPC
-1 & UPC
-1 SERIES
Storage and Handling
•
All plate clamps other than those fixed permanently in position should,
after use, be returned to safe storage. The general requirements are
essentially that the storage should be dry, free from pollutions likely to
cause damage or corrosion and extremes of temperature. Equipment
prior to storage should be checked that the unit remains in good working
order and that all parts are present.
•
When being handled the clamps should not be dropped or thrown.
Warning
•
Ensure the steel plate is to the full depth of the clamp.
•
Make sure the clamps are positioned to the centre of gravity of steel plate.
•
With long steel objects a spreader beam shall be used.
•
Ensure the gripping jaws are in full contact to steel plate.
•
Full work load limit of clamps do not exceed sling angles more than 60º.
•
Reduction of plate clamps work load limits at 90º = 75% of WLL & 120º=
50% of WLL
Warning
Observe these notes for plate clamps!