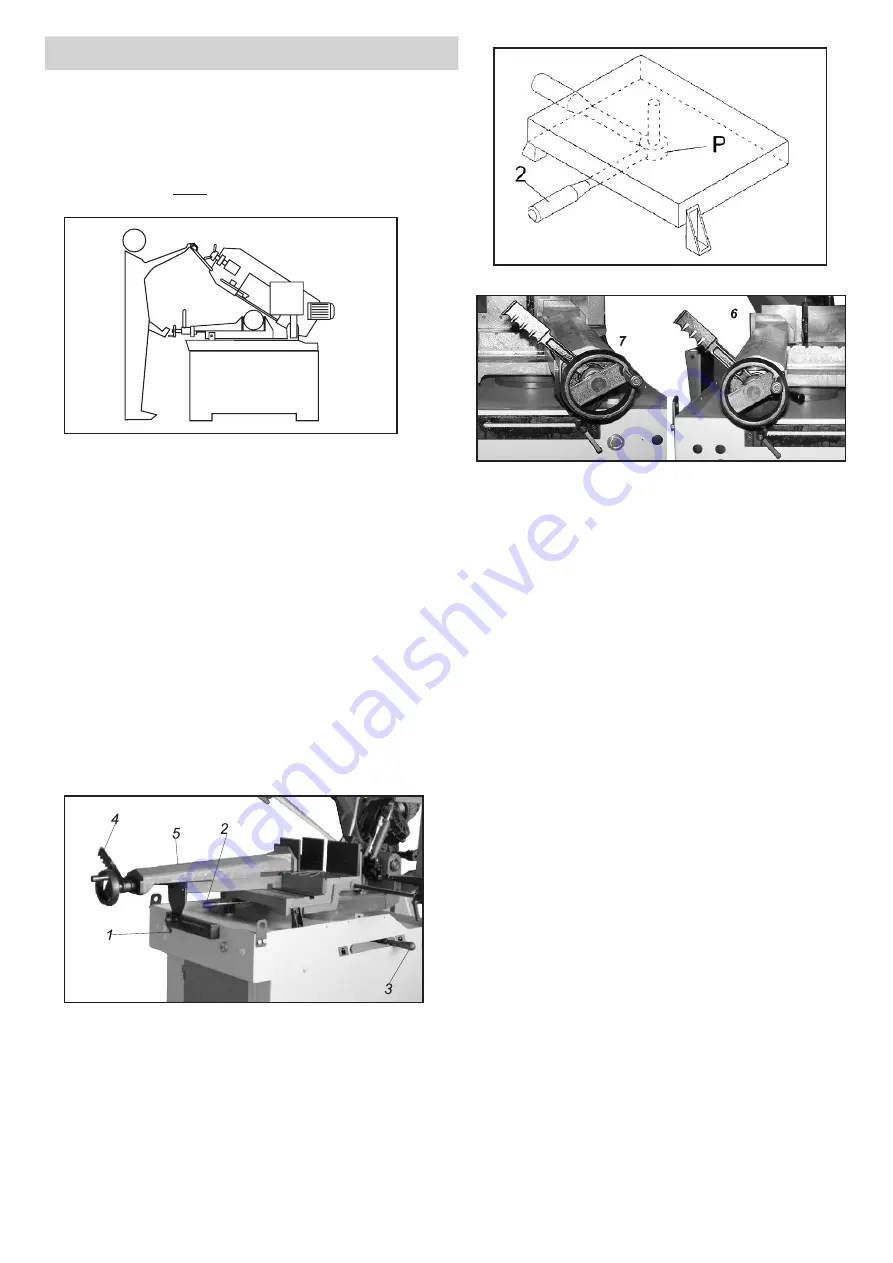
OPERATION
The machine has been designed to cut metal building
materials, with different shapes and profiles, used in
workshops, turner’s shops and general mechanical
structural work.
Only one operator is needed to use the machine, that
must stand on the
front
of machine as shown in the
picture.
Before starting each cutting operation, ensure that
the part is firmly clamped in the vice and that end is
suitably supported.
Do not use blades of a different size from those stated
in machine specifications.
If the blade gets stuck in the cut, release the running
button immediately, switch off the machine, open the
vice slowly, remove the part and check that the blade
or its teeth are not broken. If they are broken, change
the tool.
Clamping the work piece
Place work piece between the jaws.
Use the hand wheel to approach the vice jaw to the
work piece, leaving 3-4mm of space. Lock down work
piece by lowering the quick lock lever(
4
).
When the cutting cycle is finished, release vice by
raising the quick lock lever (
4
). Upon releasing the
quick lock lever (
4
), the vice jaw will open to the same
distance that was set initially. This allows for rapid
loading of same size material.
These figures below examples of suitable clamping of
different section bars, bearing in mind the cutting
capacities of the machine in order to achieve a good
efficiency and blade durability.
Once
in
position, move
the
lever(
2
) to the right to
lock it into position.
If the lever (
2
)
is not between the
vise/bed mounts and facing the user,
then the vise will
not be able to lock.
If the vise lever(
2
) has gone
beyond or is obstructed by a vise/bed mount,
then use
the following procedures.
Adjust
the
lever(
2
)
by grasping at the pivot point(
P
)
and
lowering
it
,
which may assist in the adjustment
.
The lever can now be freely rotated into a more
convenient
position
.
Some movement of the vise
Vice adjustment
jaw may be required.
Raise the lever (
2
)
then move to
the right to lock.
The device does not require any particular adjustment
;
in case of excess play
of
the
sliding
guide
,
tighten
Lock the track support(
1
) by turning handle clockwise.
slide screw more.
To move the vise in either direction, the
vise
jaw
must
be
unlocked
at
two
points
.
Release
the
track support by turning the handle(
1
)
counter-clockwise.
Release
the
vise
by
moving
the
lever(
2
) to the left.
The
vise (
5
) may now be moved to right position (
7
) or
left position (
6
)by pushing it with one hand on the vise
and the other hand on the track handle(
1
).
Fig 3
8
Fig 4
Fig 5
Fig 6
Summary of Contents for LM-270
Page 27: ...26 24 4 A 330...
Page 28: ...27 68 328 329 66A...
Page 29: ...28 209A 325 326 327 211 212 213...
Page 30: ...29...