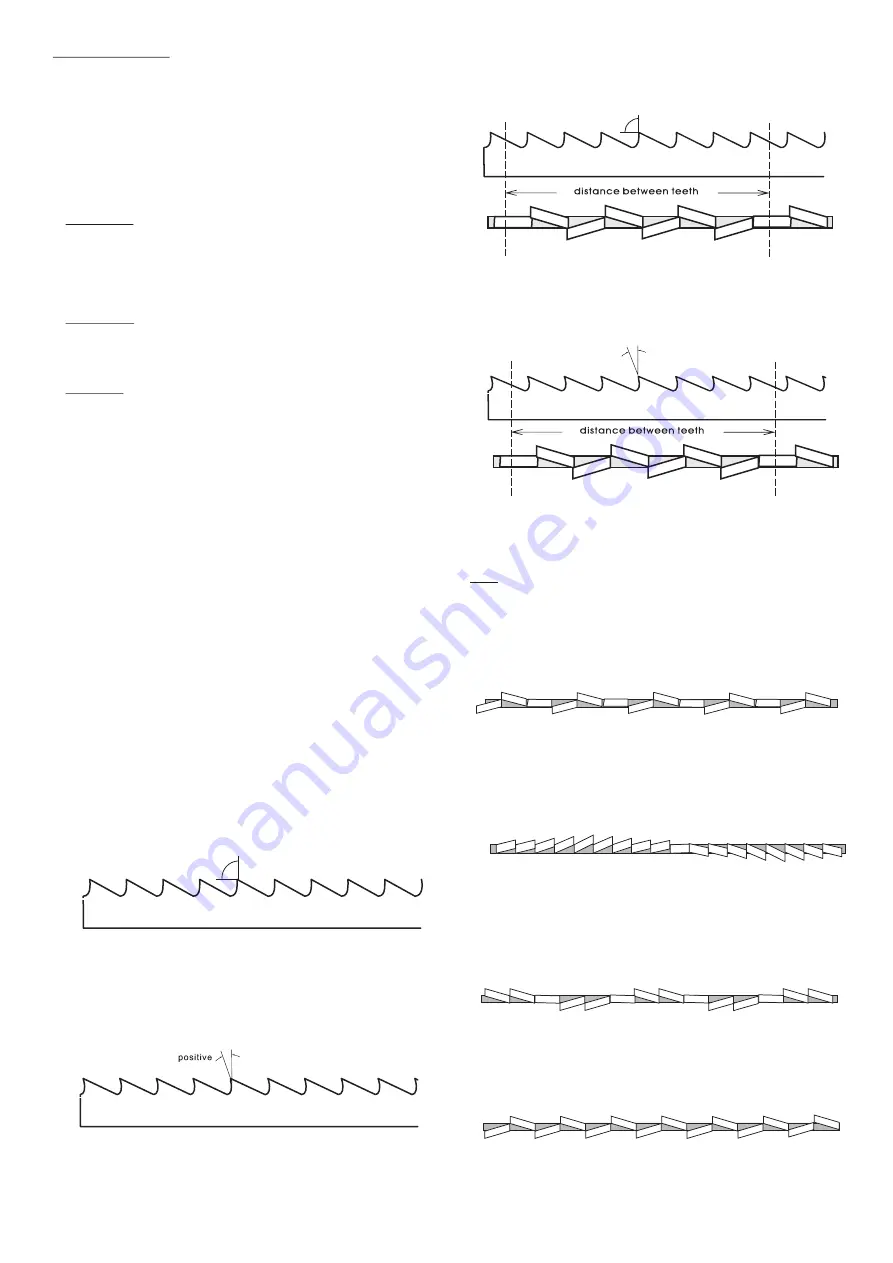
15
Blade
Structure
COMBO TOOTH
Pitch varies between teeth and consequently varying teeth
size and varying gullet depths. Pitch varies between teeth,
Bi-metal blade are the most commonly used. They consist of
which ensures a smoother, quieter cut and longer blade life
silicon-steel blade backing by a laser welded high speed steel
owing to the lack of vibration.
(HSS) cutting edge. The type of stock are classified in M2, M42,
M51 and differ from each other because their major hardness
due to increasing percentage of Cobalt (Cc) and molybdenum
(Mo) contained in metal alloy.
There
are
several
key
factors
to
consider
in choosing
a
blade
:
Tooth
Pitch---The
number
of
teeth
per
inch
(
TPI
)
on
the
blade
,
also
known
as
tooth pitch
.
Select
a
pitch
which
will
assure
that at
least
three
teeth
are
contacting
the workpiece
while
cutting
.
This
helps
to
Another advantage offered in the use of this type of blade in
distribute the
cutting
forces
and
avoids
tooth
the fact that with an only blade it is possible to cut a wide
breakage
.
range of different material in size and type.
Tooth
Form---There
are
four
common
forms of
teeth
on
the
COMBO TOOTH
blade
:
buttress
,
claw
-
tooth
,
precision
and
tungsten
O
O
9 -10 positive rake
carbide
.
Precision
is the
most
common
and
is
the
type
supplied with
this
saw
.
Tooth
Set---Set
is
the
degree
to
which
the teeth
are
bent
away
from
the
blade
.
Typical tooth
set
styles
are
raker
,
wave
and
straight set
.
Always
select
and
use
good
-
quality
saw
blades and
choose
the
right
blade
for
the
job
.
Discuss your
cutting
requirements
with
your
saw
blade dealer
to
make
sure
you
are
getting
the
type
of blade
which
best
suits
your
need
.
Poor
quality blades
and
improper
use
are
often
the
cause
This type of blade is the most suitable for the cutting of
of premature
blade
failure
.
section bars and large and thick pipes as well as for the
cutting of solid bars at maximum machine capacity. Available
Many
conditions
can
lead
to
breakage
.
Blade breakage
is
,
in
pitches: 3-4/4-6.
some
cases
,
unavoidable
,
since
it is
the
natural
result
of
the
peculiar
stresses
that bandsaw
blades
are
subjected
to
.
Sets
Blade
breakage is
also
due
to
avoidable
causes
.
Saw teeth bent out the plane of saw body, resulting in a wide
Avoidable breakage
is
most
often
the
result
of
poor
care
cut in the work-piece.
or
judgement
on
the
part
of
the
operator
when mounting
or
adjusting
the
blade
or
support
guides
.
The
most
common
Regular or Raker Set
causes
of
blade
breakage
are
:
Cutting teeth right and left, alternated by a straight
tooth.
(1) faulty
alignment
and
adjustment
of
the
guides
;
(2) insufficient
number
of
teeth
contacting
the
cut
;
(3) feeding
too
fast
;
(4) tooth
dullness
or
absence of
sufficient
set
;
Of great use for materials with dimensions superior to 5mm.
(5) excessive
tension
;
Used for cutting of steel, castings and hard nonferrous
(6) using a
blade
with
a
lumpy
or
improperly
finished
materials.
weld
;
and
(7) continuously
running
the
bandsaw
when not
in
use
.
Wavy Set
REGULAR TOOTH
Set in smooth waves.
O
0 rake and constant pitch
This set is associated with very fine teeth and it is mainly
used for cutting of pipes and thin section bars (from 1-3mm).
Most common form for transversal or inclined of solid small and
Alternate Set (in groups)
average cross-sections or pipes, in laminated mild steel and
Groups of cutting teeth right and left, alternated by a
gray iron or general metal.
straight tooth.
POSITIVE RAKE TOOTH
O
O
9 -10 positive rake and constant pitch
This set is associated with very fine teeth and it is used for
extremely thin materials (less than 1mm).
Alternate Set( individual teeth)
Cutting teeth right and left.
Particular use for crosswise or inclined cuts in solid sections or
large pipes, but above all harder materials (highly alloyed and
This set is used for the cutting of nonferrous soft materials,
stainless steels, special bronze and forge pig iron).
plastics and wood.
Summary of Contents for LM-270
Page 27: ...26 24 4 A 330...
Page 28: ...27 68 328 329 66A...
Page 29: ...28 209A 325 326 327 211 212 213...
Page 30: ...29...