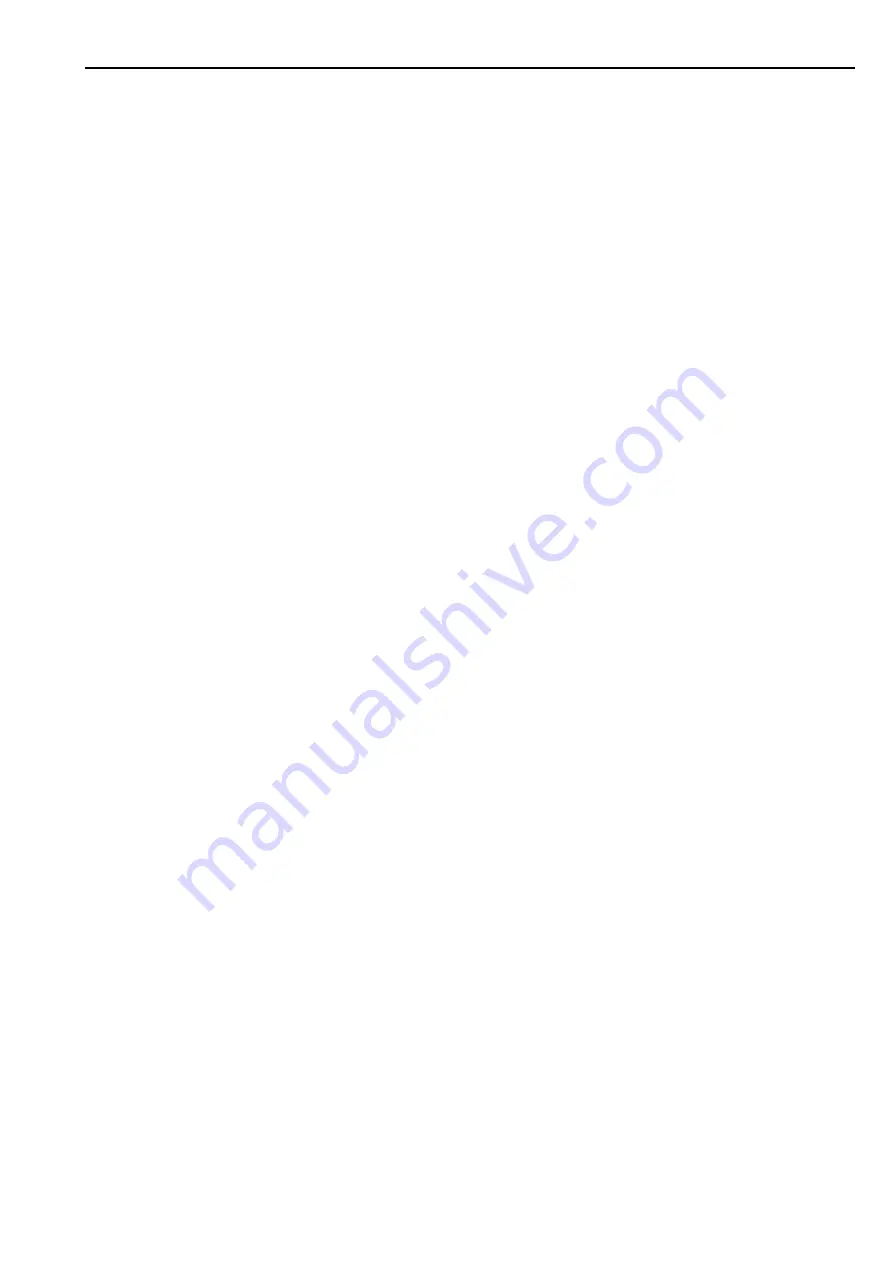
Operation manual Profibus PBD 100
23.07.2007
20/36
Byte 5 to 8: reserved for extensions, must be set to 0.
9
Description of actuator functions
9.1
Operation commands for OPEN / CLOSE operation
Operation commands are determined by operation command bits and the nominal value (set point) of the DP process representation input.
Only one command bit may be set at any given time. If several command bits are set, no operation is performed and the fault signal
‘incorrect command’ is given. To avoid placing too much strain on the mechanics the actuator is equipped with a (programmable) delay
when changing direction (reversing prevention).
The following operation command bits are required for OPEN / CLOSE
operatio
n:
Remote OPEN
Remote CLOSE
Remote operation OPEN / STOP
Remote OPEN = 1
The actuator runs in direction OPEN.
Remote OPEN = 0
The actuator stops.
The actuator is switched off automatically when the final position OPEN is reached (limit switch LSO (WÖL)
set). Faults (thermal protection, power failure, torque) stop the operation.
Remote operation CLOSE / STOP
Remote CLOSE = 1
The actuator runs to position CLOSED.
Remote CLOSE = 0
The actuator stops.
The actuator is switched off automatically if the final position CLOSED is reached (limit switch LSC (WSR) for
limit seating or LSC (WSR) and TSC (DSR) for torque seating). Faults (thermal protection, power failure,
torque) stop the operation.
Remote operation to nominal position (NOMINAL) / STOP
The positioner can only function when the actuator is equipped with a position transmitter, e.g. potentiometer / RWG (option).
Remote NOMINAL = 1
The actuator moves to the set nominal value.
Remote NOMINAL = 0
The actuator stops.
The nominal position can be set in % or in ‰. To switch from percent to per mil use parameter 2 (Data code
from position transmitter). Faults (thermal protection, power failure, torque) halt the operation via the positioner.
With a set point of 0 % or 0 ‰ the actuator runs to the end position CLO-SED With a set point of 100 % or
1000 ‰ the actuator runs to the end position OPEN In case the set point is more than 100 % or 1000 ‰ , no
operation is performed
9.2
Positioner
The positioner is activated via the bit ‘Remote Nominal’. The positioner is a three-position-controller. Via the ‘NOMINAL’ position in the
process representation input, the nominal value of the position is transmitted cyclically to the actuator as nominal variable (cycle time = bus
cycle time DP). The positioner integrated in the controls BS4581 provides the position signal for controlling the motor depending on the
nominal and actual position value. The feedback signal (actual value of actuator position) is produced internally within the actuator. The
position transmitter compares the nominal value of the position set in the controls to the locally measured actual value of the position. If the
difference between nominal value and actual value is higher than the max. error (parameter 14), the positioner drives the motor, depending
on the error, either in direction OPEN or direction CLOSE.