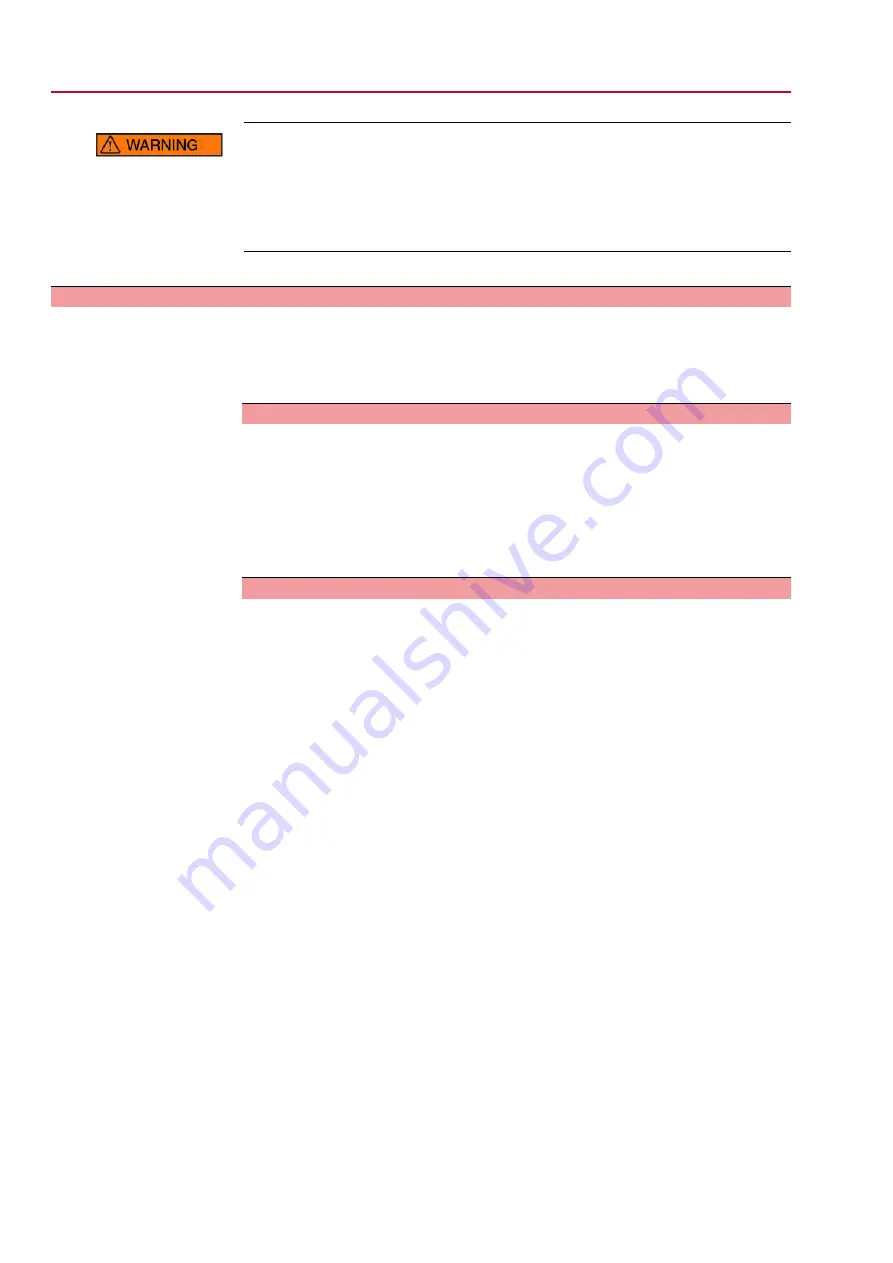
Flameproof enclosure, risk of explosion!
Risk of death or serious injury!
→
Handle cover and housing parts with care.
→
Joint surfaces must not be damaged or soiled in any way.
→
Do not jam cover during fitting.
5.
Fit cover [1] and fasten screws [2] evenly crosswise.
5.4.
Initialization
If all prerequisites starting the initialization phase are fulfilled, initialization starts
automatically to put the combination consisting of actuator (gearbox), FQM and valve
in ready for operation state.
Further information:
➭
page 27, Indications during and after initialization
.
Prerequisites for starting initialization:
●
Power supply applied.
●
Actuator controls are ready for operation (booted after power supply connection).
●
+24 V DC is applied at
ESD
input (refer to wiring diagram).
●
Actuator controls are in operation mode Local or Remote (selector switch position
on Local control or Remote control).
●
The fail safe unit is in the configured fail safe end position.
(The end position switch
LSO/LSC
of fail safe end position must be operated.)
Sequence for initialization
A constant force spring is wound within the fail safe unit thanks to the electric motor
acting as mechanical energy buffer for the fail safe operation. Simultaneously, the
actuator runs to the configured fail safe end position to make sure that both actuator
and FQM fail safe unit are in the same position as the valve.
Information
●
Clicking noises during initialization or the fail safe operation are normal and do
not represent a fault.
●
For repeated FQM tripping (fail safe operation), a pause of minimum 15 minutes
must be obeyed after the fourth fail safe operation to allow motor cool down.
After successful initialization, the FQM fail safe unit is ready for further commissioning,
for standard operation as well as for fail safe operation.
22
FQMEx 05.1 – FQMEx 12.1
Electrical connection
FM version (Class/Division System)