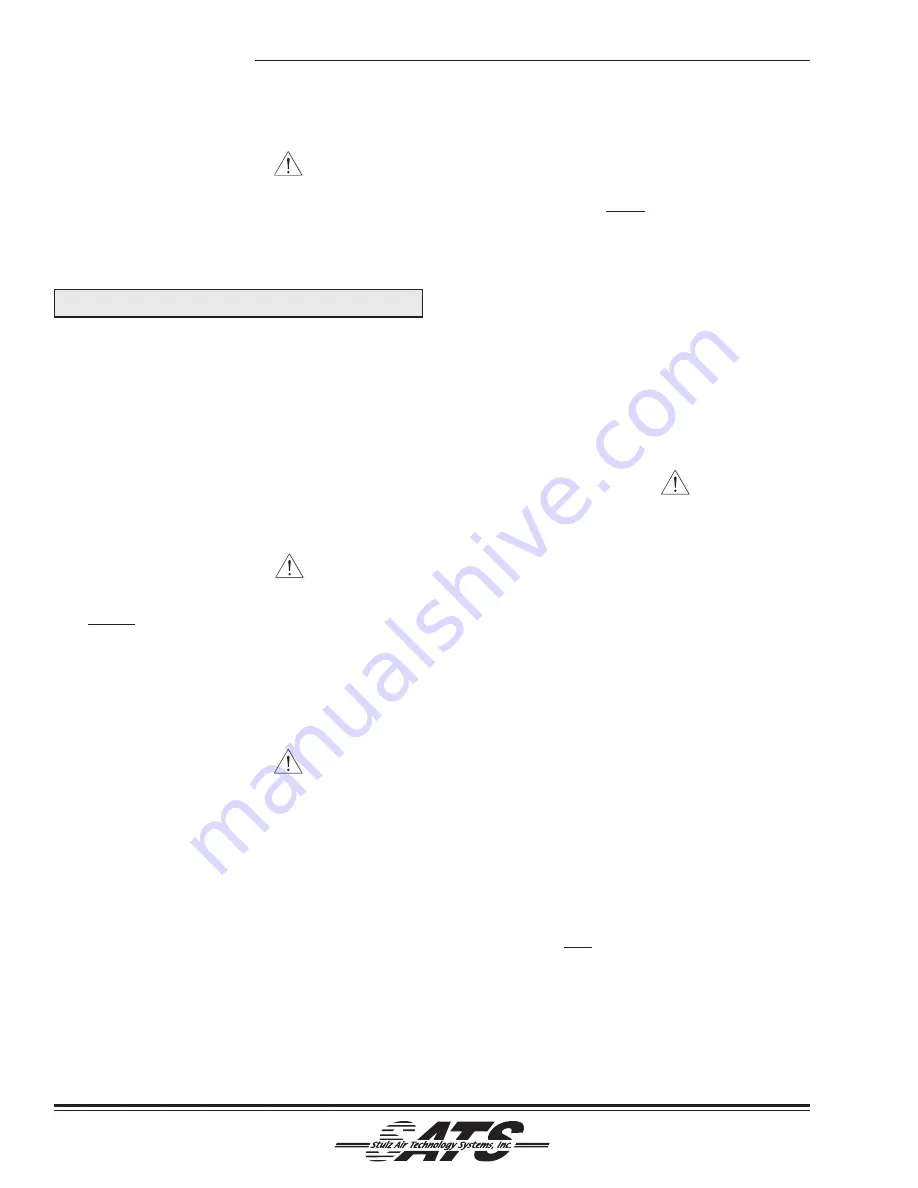
(©October, 2006)
CyberChiller Series Installation, Operation & Maintenance Manual
CAUTION
A proper vacuum must be drawn on the refriger-
ant system prior to charging. If this is not done
the refrigerant will combine with the moisture in
the pipes to form an acid that will eventually
cause compressor failure.
FINE TUNING THE SYSTEM CHARGE
2.7.3.2
-20ºF Variable Speed Control
The following instructions are for charging systems
with condenser fan cycling or variable speed control
using R-22 refrigerant.
1.
Bleed air from hoses and "break" the system
vacuum by supplying R-22 vapor. Supply R-22
vapor until the pressure is raised to about 50
psig. This small holding charge allows the low
pressure switch to “make” throughout the pro-
cess of fine tuning the system charge
WARNING
Do not add liquid R-22 refrigerant to the
suction side of the system.
2.
Start the system and use the microprocessor
controller to lower the supply water temperature
set-point 3-5°F below actual water temperature.
This will ensure the cooling mode stays on during
the charging procedure.
CAUTION
An adequate heat load must be supplied to the
unit to ensure a proper charge.
3.
Supply R-22 vapor to the suction port until the
liquid line sight glass is cleared of all bubbles.
4.
After the unit has stabilized, the liquid line sight
glass should be clear and the discharge pressure
should be a minimum of 200 psig. A superheat
reading should be taken 6 inches from the com-
pressor, with the temperature-measuring device
being well insulated. The superheat should be
approximately 10-12 ºF.
5.
A sub cooling reading should be taken on the
output side of the condenser, with the tempera-
ture-measuring device being well insulated. The
2-11
sub-cooling temperature should be approximately
10-20 ºF.
NOTE
Under cold climate conditions it is recommended
to do the following:
6.
Block off the intake air to the condenser with
cardboard (or reduce the water glycol flow) until a
constant discharge pressure (225-280 psig) can
be obtained. This will lower the possibility of
overcharging and avoid the occasional bubbles
that may appear in the sight glass during fan
cycling.
7.
Ensure the crankcase heater is operational by
checking the amperage.
CAUTION
Remove the blockage to the air intake of the
condenser (or restore the water/glycol flow).
9.
Fill out applicable blocks of Warranty Registration
and Start-Up Checklist.
2.7.4
R407C Refrigerant Charging Procedures
R-407C is a blended refrigerant recognized for being
safer for the environment. Refrigerants that are multi-
component blends have component parts with different
volatilities that result in a change in composition and
saturation temperature as evaporation and condensa-
tion occur. Typically the composition of R-407C vapor
is different than that of R407C liquid within a con-
tained system. The composition of liquid R-407C
refrigerant remains relatively constant, however, the
refrigerant vapor tends to separate into its component
parts even when circulating. When charging a system
using blended refrigerants, it is essential that the
composition of the refrigerant is maintained. To
ensure correct composition, introduce R-407C into the
system in liquid form rather than vapor form. Cylinders
which are not provided with dip tubes should be
inverted to allow only liquid refrigerant to charge the
system. Keeping the temperature of the cylinder
below 85°F will help to maintain the correct refrigerant
composition while the cylinder is emptied.
Summary of Contents for CyberChiller CCH-330-D-AR
Page 1: ... October 2006 CyberChiller Series Installation Operation Maintenance Manual ...
Page 36: ... October 2006 CyberChiller Series Installation Operation Maintenance Manual NOTES ...
Page 38: ... October 2006 CyberChiller Series Installation Operation Maintenance Manual NOTES ...
Page 40: ... October 2006 CyberChiller Series Installation Operation Maintenance Manual ...