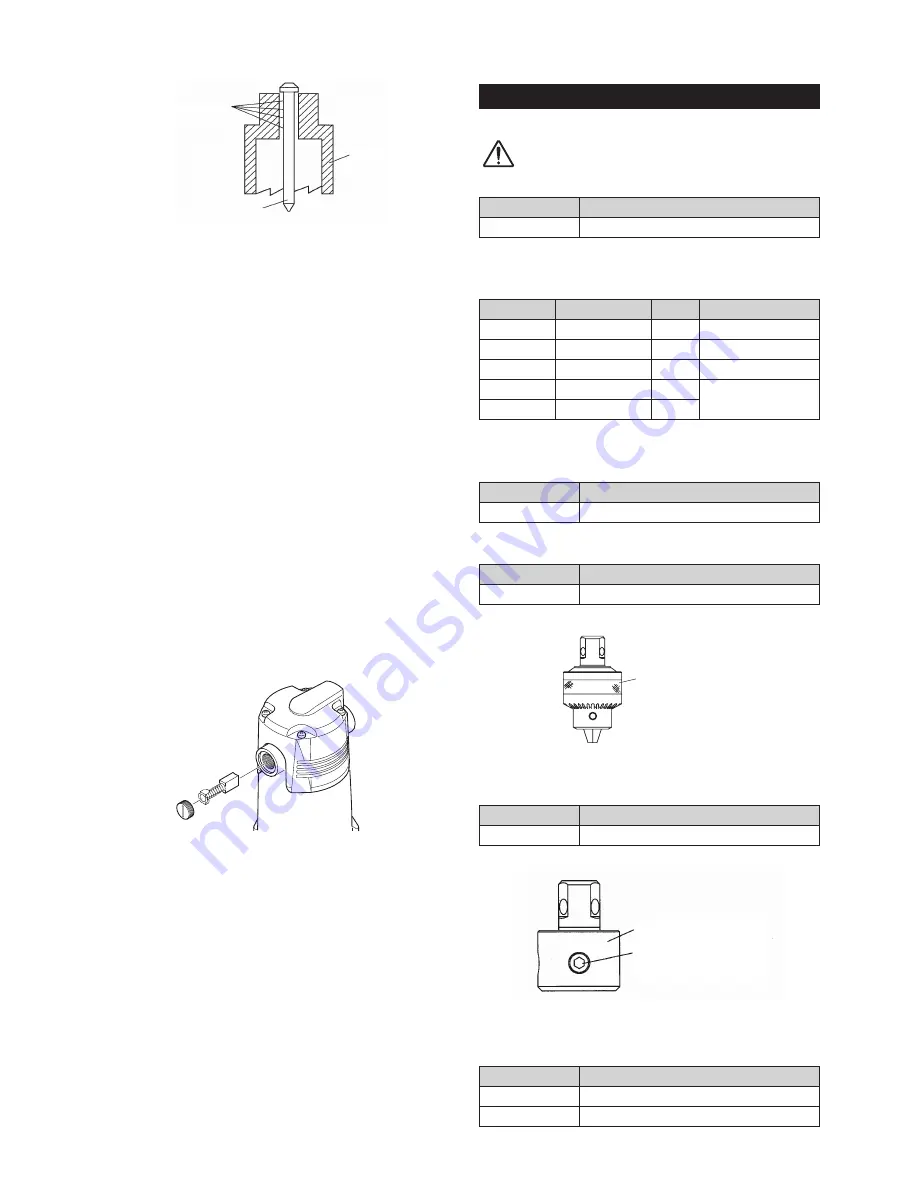
16
Cutting chips
Pilot Pin
Cutter
Fig. 33
9-6. Cutter Regrinding
When you need to regrind cutter, please contact
sales agent through which you have purchased your
machine or an authorized dealer near you.
9-7. Carbon Brushes Inspection and Replacement
Check Carbon Brushes for wear periodically.
This machine has a "switch-off brush" which
automatically stops the motor to protect it when the
carbon brushes reach the application limits.
When the brushes reach the limits, replace both
brushes with the new ones according to the following
procedures. (Fig.34)
Check - machine failure.
(1) Remove the Brush Cap with a straight slot
screwdriver.
(2) Remove the worn-out Carbon Brush and replace
it with a new one. Then reattach the Brush Cap.
(3) After replacing the Brush, operate the unit for
about ten minutes with no load.
Fig. 34
10 OPTIONAL PARTS
10-1. Nitto-Brand Cutting Oil
CAUTION
Use Nitto-brand Cutting Oil for Atra Ace.
Part No.
Part Name
TB01507
Cutting Oil 2
ℓ
(Light Blue)
10-2. Pilot Pin
(metric size)
Part No.
Part Name Depth (mm) Applicable (mm)
TK01167 Pilot Pin 06025
25
Jetbroach 12-17dia.
TJ15859 Pilot Pin 08035
35
Jetbroach 17.5-32dia.
TK01166 Pilot Pin 06050
50
Jetbroach 12-17dia.
TJ16019 Pilot Pin 08050
50
Jetbroach 17.5-32dia.
(TK00802) Pilot Pin 0850
50
※
( ):Special Order
10-3. Supporting Magnet Ass
’
y
Part No.
Part Name
TB04374
Supporting Magnet Ass’y
10-4. Twist Drill Adapter
(Fig.35)
Part No.
Part Name
TB07690
Drill Adapter Ass’y
Drill Adapter Ass’y
Fig. 35
10-5. Side-Lock Cutter Adapter
(Fig.36)
Part No.
Part Name
TB05188
Adapter Ass’y
Adapter
Hex. Socket Set Screw
with Dog Point 10X7.5
Fig. 36
10-6. Jet Oiler
(Fig.37)
Part No.
Part Name
TQ10581
Jet Oiler
TQ05275
Tube 4×7×1000
WOJ-3200.indd 16
10.11.12 11:14:34 PM