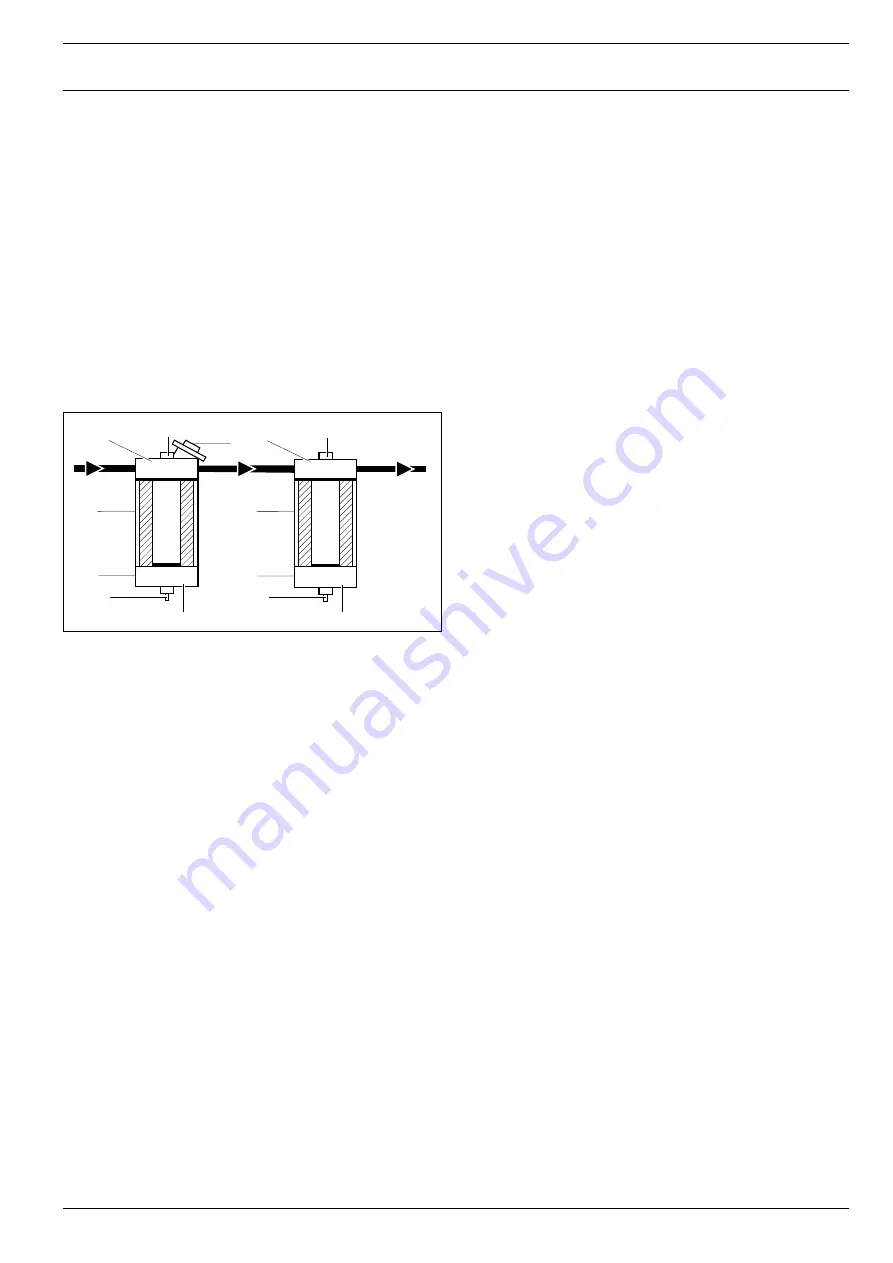
17
I
NSTRUCTION MANUAL
F
UEL SYSTEM
The fuel filter assembly strains out water and impurities from the
fuel.
The fuel is drawn from the tank the through the fuel pre-filter (FF1)
and the fuel fine-filter (FF2) to the engine injection pump.
Only one third of the fuel drawn is used for combustion. The
remnant is used to cool the injection pump and is returned to the
tank via a fuel cooler.
The fuel cooler is located behind the grating at the right-hand side of
the compressor.
The fuel filters each consist of an adapter head, a spin-on filter
element and a waterseparator bowl.
DV1,2 Drain valve
1
Adapter head
FF1
Fuel pre-filter
2
Filter element
FF2
Fuel fine-filter
3
Filter bowl
VP1,2
Vent plug
4
Hand-pump
Draining the fuel pre-filter
1. Open the bowl drain valve (DV1) and pump water out.
2. Close the drain valve.
Draining the fuel fine-filter
1. Open the bowl drain valve (DV2) to evacuate water.
2. Close the drain valve.
Replacing the fuel pre-filter element
1. Drain the fuel from the bowl.
2. Remove the filter and separate the bowl from the element.
3. Apply a film of gas oil to the new bowl seal.
4. Screw the bowl to the new element tightly by hand.
5. Apply a film of gas oil to the new element seal.
6. Screw on the filter tightly by hand.
7. Open the head vent and operate the pump. Close the vent when
fuel begins to purge.
8. Check for leaks, retighten if necessary.
Replacing the fine-filter element
1. Drain from the bowl.
2. Remove the filter and separate the bowl from the element.
3. Apply a film of gas oil to the new bowl seal.
4. Screw the bowl to the new element tightly by hand.
5. Apply a film of gas oil to the new element seal.
6. Fill the element with fuel and screw on the filter tightly by hand.
7. Check for leaks, retighten if necessary.
C
OOLANT
The coolant is a mixture of water and anticorrosion/antifreeze agent.
The coolant must remain in the system all the year round to ensure
adequate corrosion protection and to increase the boiling point.
Renew the coolant every two years, as the corrosion protection
diminishes.
It is not permitted to use water alone as a coolant even if antifreeze
properties are not required. The water in the coolant has to satisfy
certain requirements, which are frequently, but not always, met by
drinking water. If the quality of the water is insufficient, the water
has to be treated. Information regarding this can be obtained from
any Mercedes-Benz Service Station.
The portion of anticorrosion/antifreeze agent in the coolant must not
drop below 40 % by volume during operation (equals antifreeze
protection down to approximately -25 ¡C). A lower portion does not
adequately ensure the anticorrosive properties.
To avoid any damage to the cooling system:
Ð
Use only approved anticorrosion/antifreeze agents. Information
is available from any Mercedes-Benz Service Station.
Ð
When replenishing the system (after loss of coolant) it is
essential to ensure an anticorrosion/antifreeze portion of 50 %
by volume (antifreeze protection down to -37 ¡C).
Ð
Do not use more than 55 % by volume of anticorrosion/
antifreeze agent (= maximum antifreeze protection). Otherwise
the antifreeze properties will be reduced and the heat dissipation
impaired.
In exceptional cases, where it is evident that no anticorrosion/
antifreeze agent can be obtained and no antifreeze protection is
required (e. g. tropics), 1 % by volume = 10 cm
3
/litre of corrosion
protection oil must be added. In such cases, renew the coolant
annually.
DV1
1
2
FF1
VP1
3
4
DV2
1
2
FF2
VP2
3
Summary of Contents for XRVS455 Md
Page 2: ...2 XRVS455 Md ...
Page 26: ...26 XRVS455 Md ...