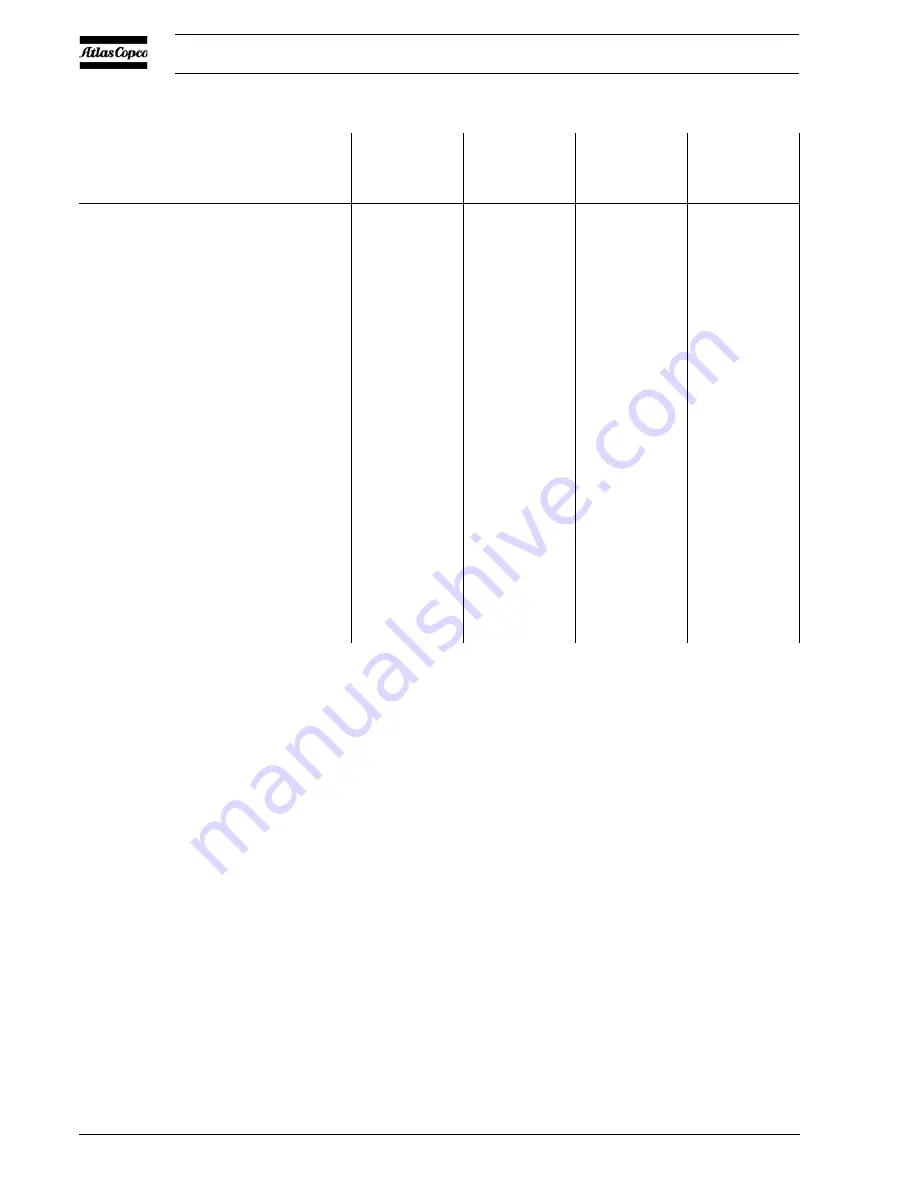
58
Instruction Manual
Compressor type
XAHS 37 DD -
XAHS 70 DD7
XAS 47 DD -
XAS 90 DD7
XAS 47 DDG -
XAS 90 DD7G
XAS 57 DD -
XAS 110 DD7
DDG IT
Designation
Unit
Value
Value
Value
Value
Performance data
1)
1. Engine shaft speed, normal and
maximum
r/min
2,400
2,400
2,750
2,750
2. Engine shaft speed, compressor
unloaded
r/min
1,850
1,850
1,850
1,850
3. Engine shaft speed, generator at
maximum load
r/min
-
-
2,700
-
4. Free air delivery
2)
no aftercooler
l/s
32
43
31
50
with aftercooler
l/s
27
38
26
45
5. Typical oil content of compressed air
mg/m
3
< 5
< 5
< 5
< 5
free air
6. Engine oil consumption (maximum)
g/h
12.3
12.3
15
15
7. Compressed air temperature at outlet
valves
no aftercooler
°C
90
88
93
93
with aftercooler
°C
30
30
30
30
8. Noise level
- Sound pressure level (LP), measured
according to ISO 2151 under free field
conditions at 7 m distance
dB(A)
70
70
70
72
- Sound power level (LW) complies with
2000/14/EC
dB(A)
98
98
98
98
Summary of Contents for XAHS 37 DD
Page 2: ......
Page 63: ......
Page 64: ...Printed in Belgium 07 2007 2954 2140 02 www atlascopco com ...