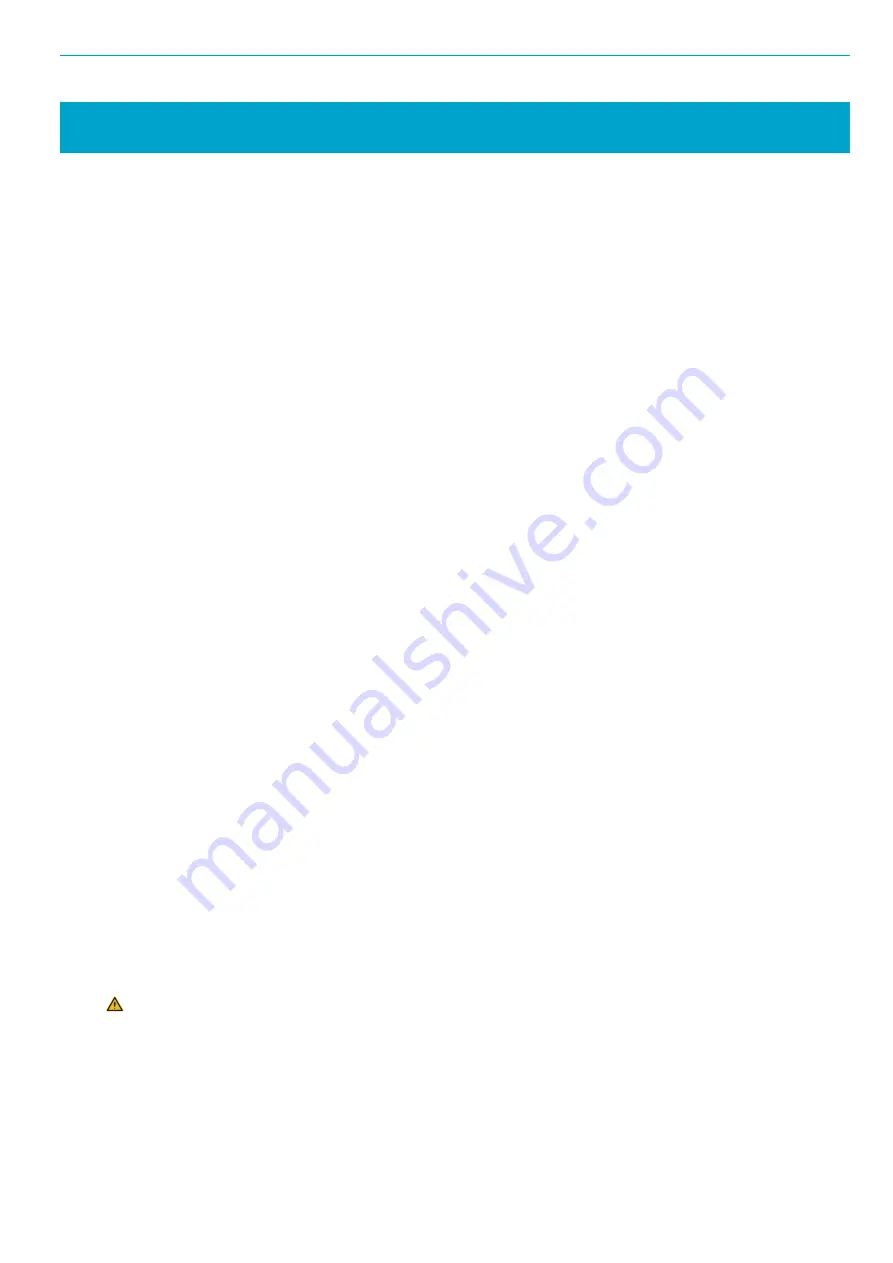
LSV39 SA12-125
EN
Operation
© Atlas Copco Industrial Technique AB - 9839 0621 01
11
Operation
Ergonomic guidelines
Consider your workstation as you read through this list of general ergonomic guidelines and see if you can
identify areas for improvement in posture, component placement, or work environment.
■
Take frequent breaks and change work positions frequently.
■
Adapt the workstation area to your needs and the work task.
■
Adjust for convenient reach range by determining where parts or tools should be located to avoid
static load.
■
Use workstation equipment such as tables and chairs appropriate for the work task.
■
Avoid work positions above shoulder level or with static holding during assembly operations.
■
When working above shoulder level, reduce the load on the static muscles by reducing the weight
of the tool, using for example torque arms, hose reels or weight balancers. You can also reduce
the load on the static muscles by holding the tool close to the body.
■
Make sure to take frequent breaks.
■
Avoid extreme arm or wrist postures, particularly for operations requiring a degree of force.
■
Adjust for convenient field of vision by minimizing movement of the eyes and head during the work
task.
■
Use the appropriate lighting for the work task.
■
Select the appropriate tool for the work task.
■
Use ear protection equipment in noisy environments.
■
Use high-quality inserted tools or consumables to minimize exposure to excessive levels of vibration.
■
Minimize exposure to reaction forces.
■
When cutting:
A cut-off wheel can get stuck if the wheel is either bent or if it is not guided properly. Make sure to
use the correct flanges for cut-off wheels and avoid bending the wheel during cut-off operation.
■
When drilling:
The drill might stall when the drill bit breaks through. Makes sure you use support handles if the
stall torque is too high. The safety standard ISO11148 part 3 recommends using something to ab-
sorb the reaction torque above 10 Nm for pistol grip tools and 4 Nm for straight tools.
■
When using direct-driven screw or nutrunners:
Reaction forces depend on tool setting and joint characteristics. The ability to bear reaction forces
depends on the operator’s strength and posture. Adapt the torque setting to the operator's strength
and posture and use a torque arm or reaction bar if the torque is too high.
■
Use dust extraction system or mouth protection mask in dusty environments.
Configuration Instructions
Wheel configuration options
WARNING Risk of injury
►
Always shut off air supply, drain hose of air pressure and disconnect tool from air supply when not
in use, before changing accessories or when making repairs.
►
Always wear protective gloves when changing accessories or when making repairs.
The table below shows the configuration options for different wheel types with applicable attachment parts
in the following order:
Grinding wheel (Type 27), Cutting off wheel (Type 41), Wheel brush, Pad