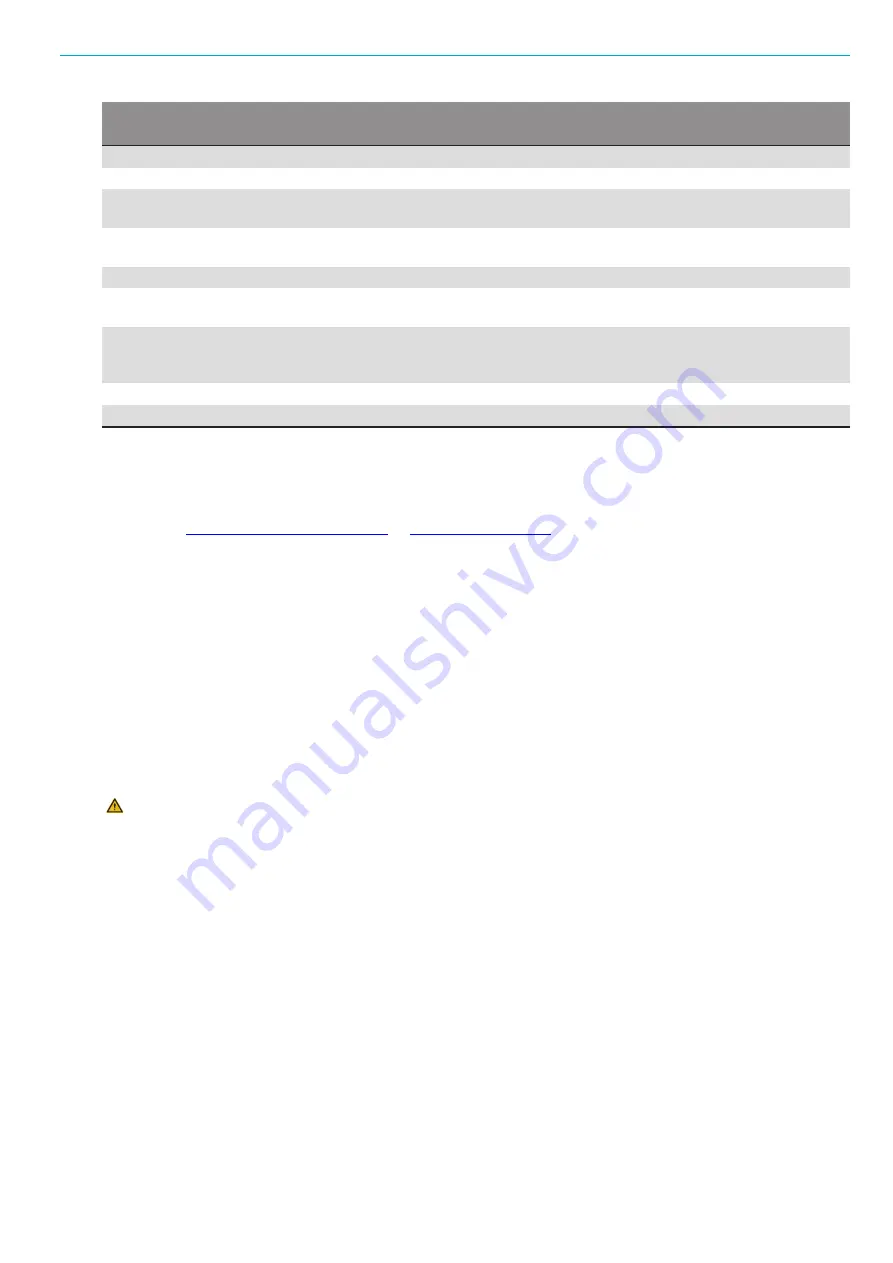
LSV39 SA12-125
EN
Product Information
© Atlas Copco Industrial Technique AB - 9839 0621 01
7
Position
Part
Function
1
Air inlet
For connection to compressed air through a whip hose.
2
Throttle lever
Starts and stops the tool.
3
Security mechanism
A two-step function for a safe start and stop of the tool. Push the re-
lease arm forward to release the throttle lever
4
Support handle
Adjustable for a flexible working position for left or right handed opera-
tor.
5
Spindle locking button
Locking the spindle to facilitate fastening of the wheel.
6
Wheel guard adjustment
button
Adjusting the wheel guard position.
7
Wheel guard
Adjustable wheel guard allows flexible positioning. Prevents the opera-
tor to come in contact with the grinding wheel and protect the operator
in the event of a bursting wheel.
8
Auto balancer
Reduces vibrations.
9
Spindle
For fastening of the wheel.
Technical Product Data
Technical Product Data can be found on either ServAid, or the Atlas Copco website.
https://servaid.atlascopco.com
or
Service Overview
Overhaul
The tool should be examined regularly at six-month intervals. If it is in heavy duty service or not running
properly it should be taken out of service more often.
To increase life length of gears, change grease and replace bearings and sealings more often.
After a maximum of 1000 hours the angle gear grease shall be changed. If the grease are not changed in
time other angle gear and motor parts might get damaged.
For correct lubrication properties use Rhenus LKR03, a semifluid type of grease. The required amount of
grease is maximum 11 cm³.
The strainer at the air inlet should be cleaned frequently to prevent clogging and decreased capacity.
WARNING Risk of Serious Injury or Death
Overspeed can result in serious injury or death.
►
If a speed governor is used, make sure that the correct speed governor is assembled. Careless
handling may put it out of order
►
Do not disassemble security parts and always replace them if they are damaged.
►
Always do a free speed check of the tool after service.
Replacement of vanes
Replace the vanes in the motor when a power drop of the tool is experienced. If the vanes are not re-
placed in time other motor parts may be damaged. For increased life length of the vanes use an oil lubri-
cator to dose oil into the air inlet.
Maintenance and service instructions
The service must only be done by authorized workshops or qualified service technicians.