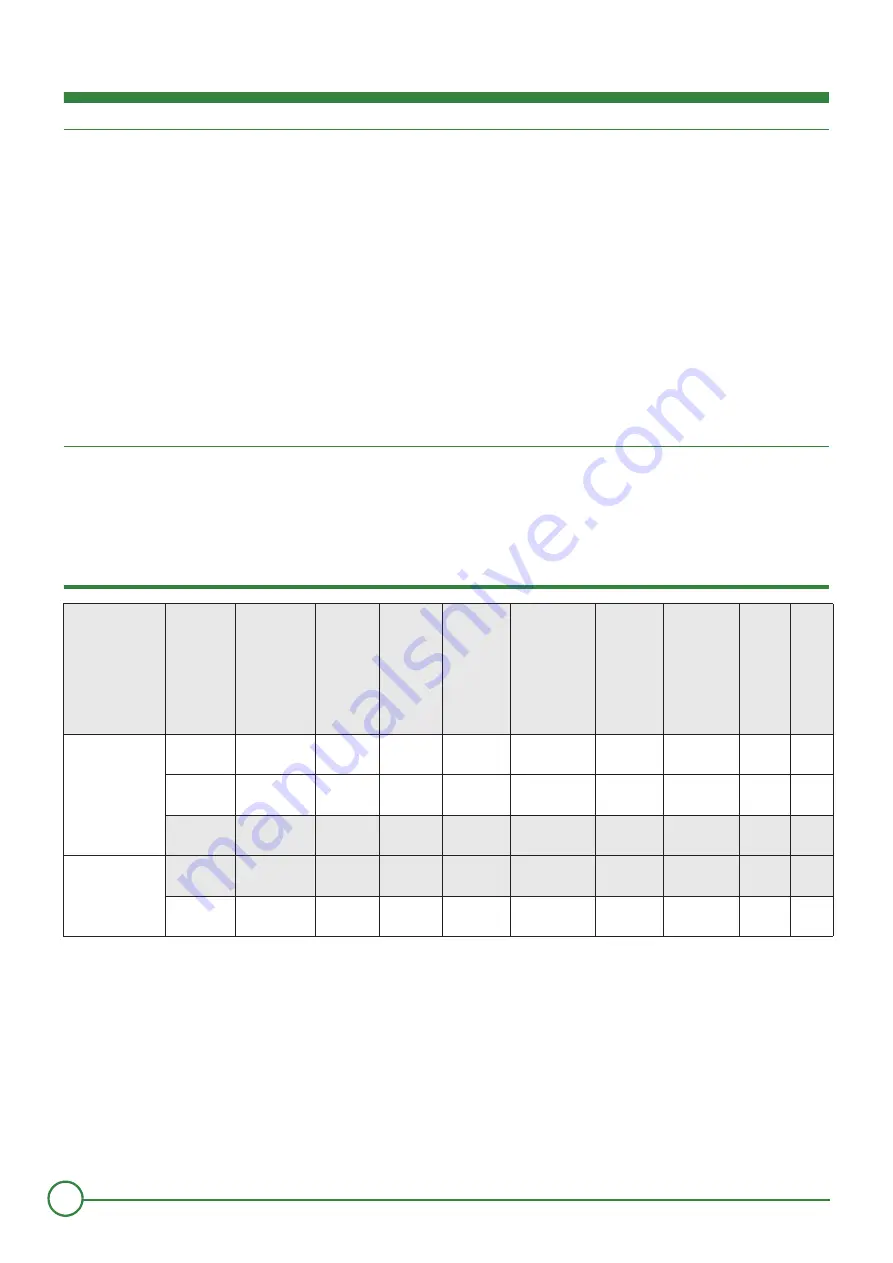
16
Installation instructions "1552 - EN"
Adjustment
Recommendations for measuring combustion
Fine tune the burner so that it meets the existing local regulations.
It is important that the flow of combustion products between the chimney and the furnace nozzle is sealed in order to avoid
measurement errors.
In order to measure combustion: Keep to the burner's operating times:
• 10 min operation (Boiler at temperature).
• 20 min operation (Cold boiler).
After assembling and setting the burner:
• Check the soot index.
• Check the smoke gas emission values.
Keep to the advised settings to avoid having flame surveillance problems at low powers
Recommendations for adjusting the recirculation slot
The recirculation gas proportion is based on the recirculation slot. This gas proportion directly affects the NOx rate.
The larger the recirculation slot, the lower the NOx rate. However, flame stability decreases. The recirculation slot
must be set to obtain the lowest possible NOx rate with good flame stability.
1 Recommended Settings
(1)
Ring from 1 mm
In grey: factory setting
Burner
Burner
power
(kW)
Filler
(USG)
Fuel oil
pressure
(bar)
Head
pressure
(mbar)
Air valve
setting
indication
Recirculatio
n slot (mm)
Position
of the
head -
Distributi
on bar
(Indicativ
e setting)
Number of
rings
4
(1)
Side
3
(mm)
CO
2
(%)
ATL F10E2-1.28
23
Danfoss
0.55 - 80°S
10
6.5
15
2
8
2
2.5
12.5
25
Danfoss
0.55 - 80°S
12
7.8
45
2
8
2
2.5
12.5
28
Danfoss
0.55 - 80°S
14
8.6
110
2
8
2
2.5
12.5
ATL F10E2-1.33
28
Danfoss
0.55 - 80°S
14
6.7
90
2
5
4
2
13
30
Fluidics
0.65 - 60°SF
12
7.5
120
2
5
4
2
13