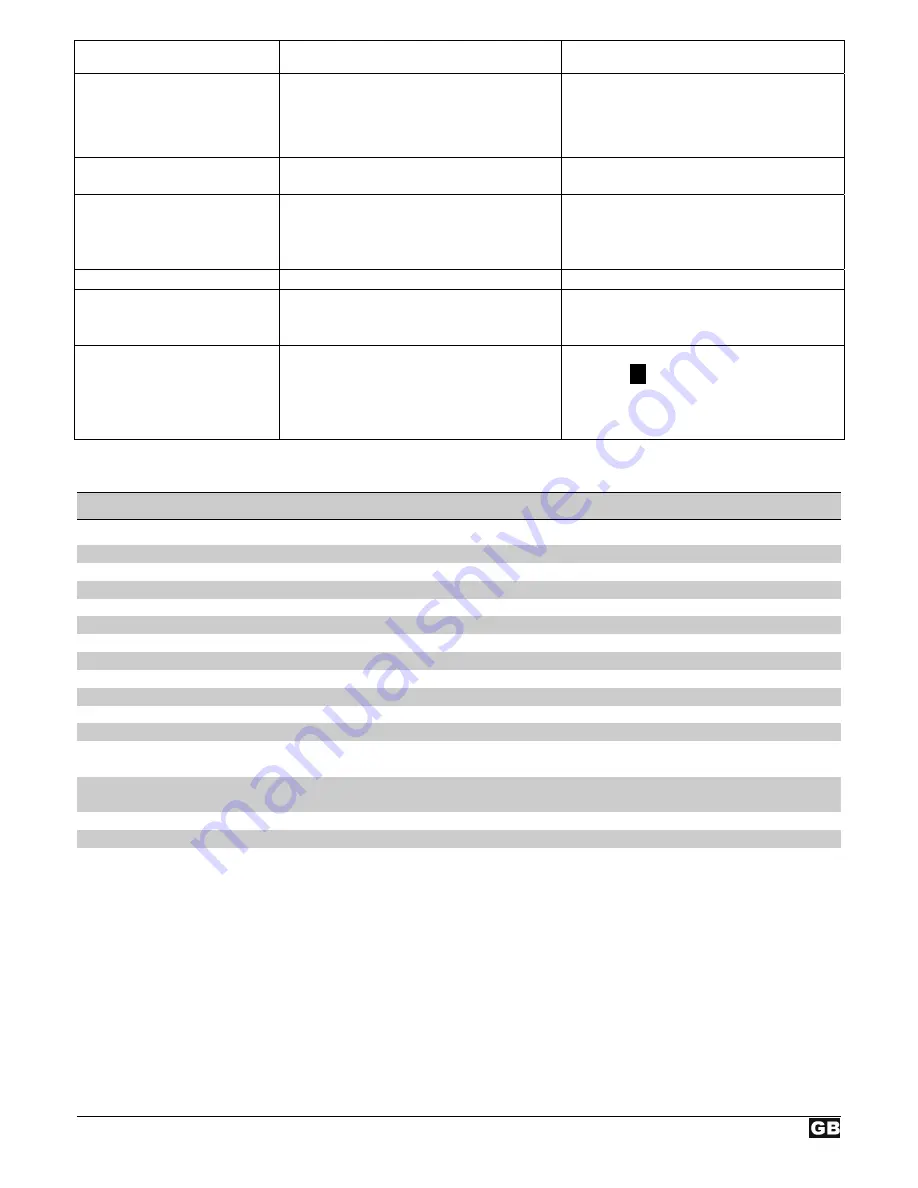
21
Fault Possible
cause Remedy
Machine is stalled during
machining.
•
Dull cutting blades
•
Feed is too great
•
Motor protecting switch has tripped
•
Replace or sharpen the blades.
•
Continue working with slower rate of feed.
•
Switch motor back on after cooling
(”Motor protection”, p. 9)
Workpiece is jammed during
thicknessing.
•
Excessive depth of cut
•
Reduce depth of cut and machine workpiece
in multiple passes.
Surface unsatisfactory.
•
Dull cutting blades
•
Cutting blades blocked by shavings
•
Erratic feeding
•
Replace or sharpen the blades.
•
Remove shavings.
•
Feed the workpiece with constant pressure
and reduced speed.
Machined surface too rough.
•
Too much moisture in the workpiece
•
Dry the workpiece.
Machined surface is shaky.
•
Workpiece was machined against the growth
direction
•
Too much material cut in a single pass
•
Machine the workpiece in opposite direction.
•
Machine the workpiece in multiple passes.
Workpiece advance is slow during
thicknessing.
•
Thicknessing adjusting lever not in its top
position
•
Resin on the thicknessing table plate
•
Sluggish transport rollers
•
Put the thicknessing adjusting lever to its top
position
F2.
•
Clean the table plate and apply a thin film of
sliding wax.
•
Repair the transport rollers.
Technical data
Type / Model
MBY10 / ADH 254
Motor rating P
1
1600 W (S1)
Mains voltage
230 V
Mains frequency
50 Hz
Mains fuse
10 A inert
Idle speed (cutting blades)
6700 rpm
Feed rate for thicknessing
8 m/min
Max. workpiece width
254 mm
Workpiece height for thicknessing
5 - 160 mm
Depth of cut for planing
0 - 3 mm
Depth of cut for thicknessing
0 - 2 mm
Cutting blade dimensions
(length x width x thickness)
258 x 20 x 2.5 mm
Table dimensions Planing
1050 x 260 mm
Thicknessing
480 x 254 mm
Table height with stand
890 mm
Weight
approx. 82 kg
Diameter of the shavings exhauster connector
75 mm
Commercial small dust removers or industrial vacuum cleaners can be used for exhaustion.