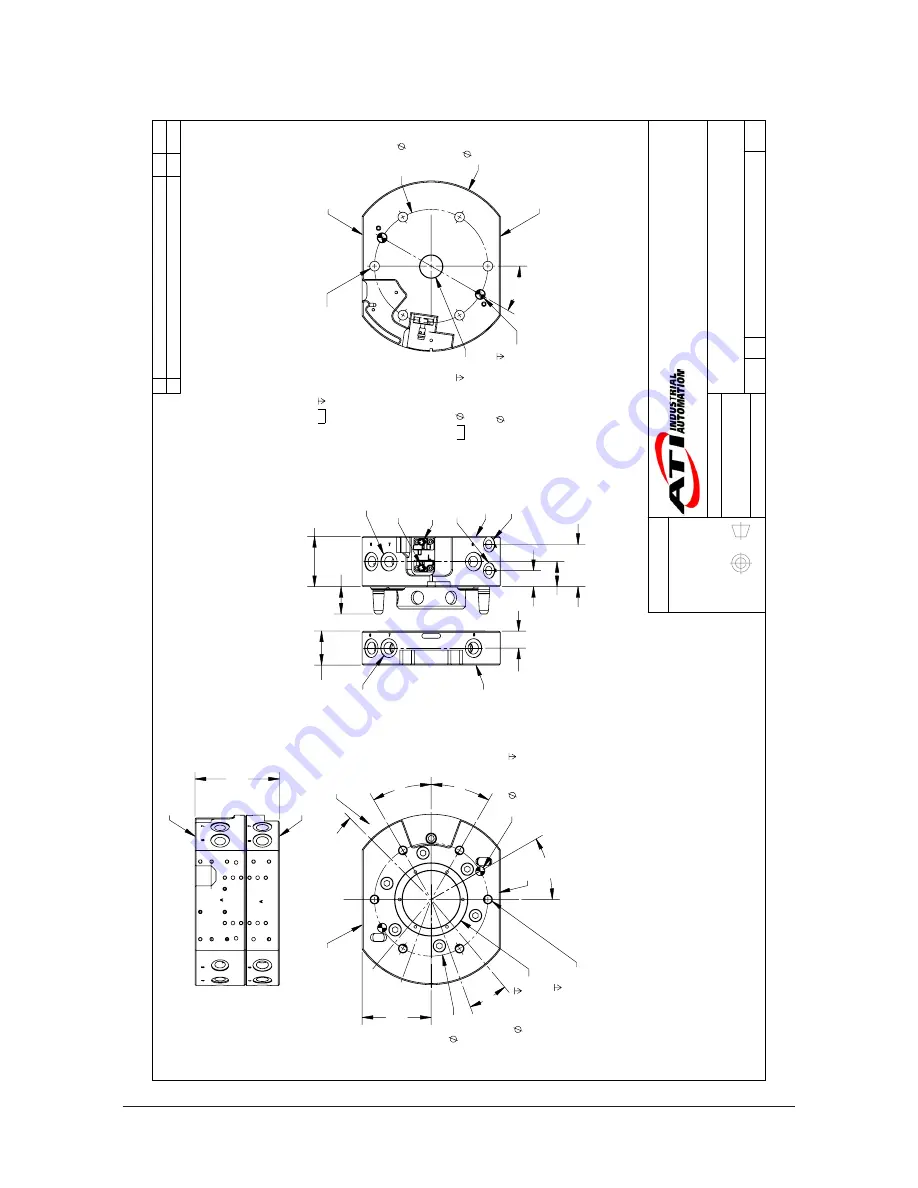
Manual, Tool Changer, QC-110
Document #9620-20-B-110 Series Base Tool Changer-26
Pinnacle Park • 1031 Goodworth Drive • Apex, NC 27539 • Tel: 919.772.0115 • Fax: 919.772.8259 •
B-53
8.4 QC-110 Tool Changer, G 1/4 BSPP Ports
3rd ANGLE PROJECTION
30.2 Pin
37.7 Tool
55.4 Master
18.9
17.8
27.7
46.6
8X G1/4
Pneumatic Thru Ports
8X G1/4 Pneumatic Thru Ports
(B)
(A)
G1/8
Lock Port
G1/8
Unlock Port
Lock Sensor
Unlock Sensor
25 H7
3.8
Note 3
B.C.
125
188
Master & Tool
6X Thru Holes for M10 SHCS
15.5 From Far Side Equally Spaced
Customer Interface
2X
10 (Slip Fit)
12
Equally Spaced
Customer Interface
Note 3
30°
Master Side
(projection only)
Flat A
Flat B
80
H7
4
Customer Interface
Note 4
15°
20°
Typ.
30°
30°
76.2 Typ.
B.C
125
30°
Tool Side
(projection only)
Flat A
Flat B
8
7
6
5
4
3
2
1
Pneumatic Port I.D.
6X M10X1.5
20
Equally Spaced
Customer Interface
2X
10 H7
6
Equally Spaced Customer Interface
93.1
Coupled
(A)
(B)
Notes:
The -Sx in the Master part number indicates the Lock/Unlock sen
sor option.
1.
Multiple sensor options are available. Ready to Lock sensing is available.
2.
No options for a boss size. Must use the two Ø10 dowel holes fo
r alignment.
3.
Center recess inserts available for several sizes.
4.
Part Numbers Shown: (A) Master: 9120-110AM-000-000-Sx-G14 (B) Tool: 9120-110FT-000-000-G14
Rev.
Description
Initiator
Date
05
ECO 14275; Updated to show current Master Side configuration
SZJ
7/26/2016
B
1:2.5
1
3
REVISION
NOTES: UNLESS OTHERWISE SPECIFIED.
DO NOT SCALE DRAWING. ALL DIMENSIONS ARE IN MILLIMETERS.
DRAWN BY:
CHECKED BY:
D. Swanson 6/5/09
D. Wagner 6/10/09
TITLE
SCALE
SIZE
DRAWING NUMBER
PROJECT #
SHEET OF
9630-20-110-G14
05
PROPERTY OF ATI INDUSTRIAL AUTOMATION, INC. NOT TO BE REPRODUCE
D IN ANY
MANNER EXCEPT ON ORDER OR WITH PRIOR WRITTEN AUTHORIZATION OF A
TI.
1031 Goodworth Drive, Apex, NC 27539, USA Tel: +1.919.772.0115 Email: [email protected] Fax: +1.919.772.8259 www.ati-ia.com ISO 9001 Registered Company
QC-110 Tool Changer with 1/4 BSPP Ports