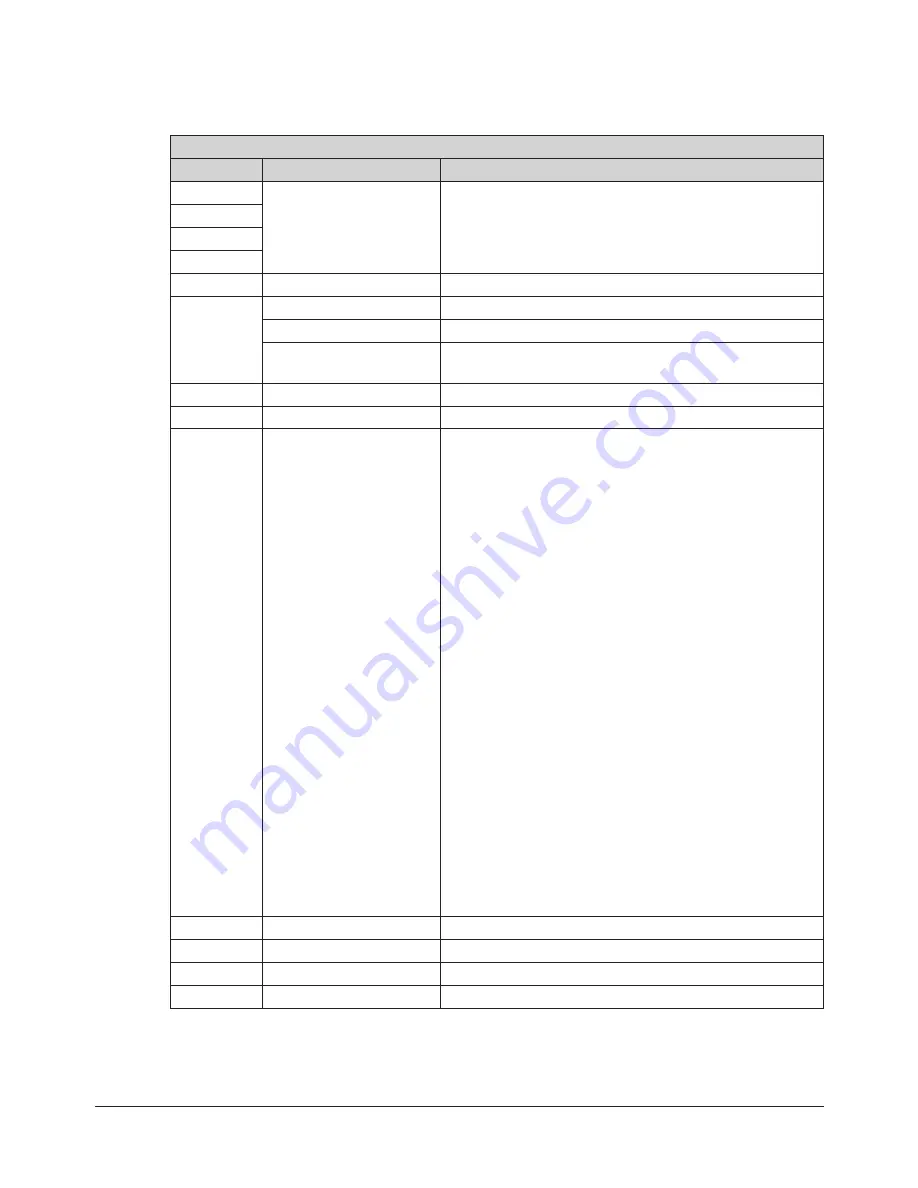
Manual, Passive Compliant Force Control
Document #9610-50-1036-04
Pinnacle Park • 1031 Goodworth Drive • Apex, NC 27539 USA • Tel: +1.919.772.0115 • Fax: +1.919.772.8259 • www.ati‑ia.com
23
The following serial console commands are available to use with a program like PuTTY (available online)
with a default baud rate of 115200.
Table 4.3—Serial Console Commands
Command
Operand(s)
Description
?
Print help text
H
Help
Man
SysVer
Print firmware version
Set / Cal
Read all parameters
[parameter name]
Read all parameters that match input parameter name
[parameter name] [value]
Write a new value to the parameter matching input
parameter name
SaveAll
Save all changes to parameters
StartCal
Start gravity compensation calibration process
Stream
[HDBXYZTP%OR]
Stream data over console interface
X = Raw accelerometer X axis
Y = Raw accelerometer Y axis
Z = Raw accelerometer Z axis
I = Filtered accelerometer X axis
J = Filtered accelerometer Y axis
K = Filtered accelerometer Z axis
R = DAC position
O = DAC regulator
% = Position
P = Raw hall effect sensor
F = Filtered hall effect sensor
T = Temperature
# = Line counter
S = Checksum
H = Hexadecimal
D = Decimal
B = Binary
> = Compressed
< = Formatted
Flow
Display current data during each step of main signal flow
Status
Display status report
LEDTest
Run startup LED test
Reset
Reset MCU (Microcontroller Unit)