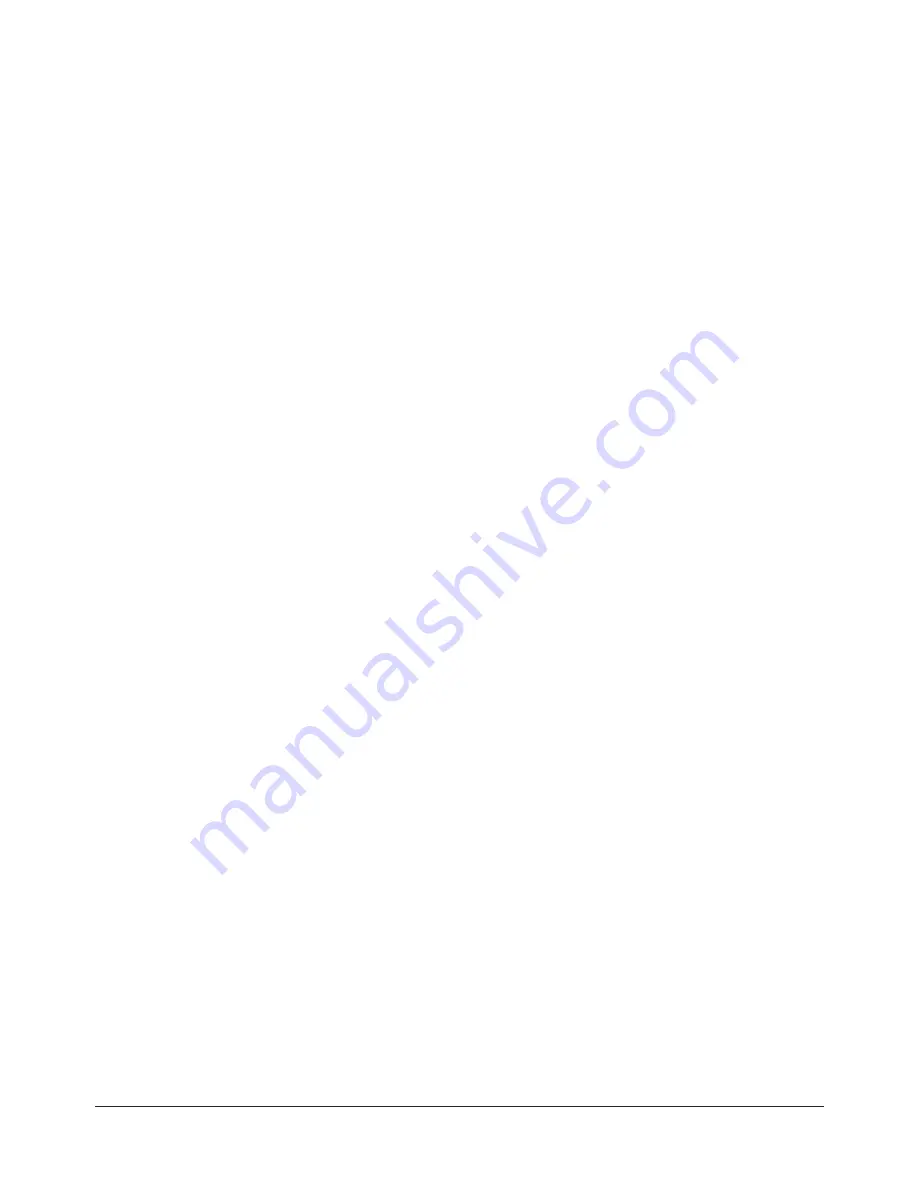
Manual, Compliant Reciprocating Tool, CRT Series
Document #9610-50-1028-04
Pinnacle Park • 1031 Goodworth Drive • Apex, NC 27539 USA • Tel: +1.919.772.0115 • Fax: +1.919.772.8259 • www.ati‑ia.com
15
4.2 Normal Operation
The following sections describe the normal operating conditions for the CRT.
4.2.1 Air Quality
The air supply should be clean, dry, filtered, and lubricated. A coalescing filter that has elements
rated for 30 micron or better is required. The air must be supplied at 6.2 bar (90 psi).
Air quality can affect tool performance substantially. Particulates can block airflow or impede
reciprocating motion. If reciprocating tools do not receive the proper air pressure, the tool stalls.
Any water in the system damages the housing and pneumatic drives.
4.2.2 Lubrication
Lubricate the air supply with 1‑2 drops of commercial air tool oil per minute (SAE
10W recommended).
The CRT should be run with lubrication in the air supply to maximize motor life.
4.2.3 Media Selection, Design, and Maintenance
Check media quality regularly to ensure it is not dull or worn. Using worn media causes a poor
surface finish and increased wear on the tool that results in premature tool failure.
In many robotic reciprocating applications, including steel and aluminum, no cooling or lubrication
of the rotary file is necessary. For some materials and applications, the addition of coolants or
compressed air may aid the cutting process. If it is determined that liquid coolants are required, a
non‑oil cutting fluid should be used to prevent premature wear of the tool.
4.2.4 Reciprocating Tool Approach Path Should Be Slow and at an Angle
The CRT should approach the workpiece slowly and at an angle.
When beginning a reciprocating pass, try to minimize the initial impact on the work piece by
slowly approaching the tool at an angle while maintaining a slightly parallel path with the surface.
Gouging and premature wear of the tool can occur if the tool perpendicularly approaches the
workpiece too quickly. Additionally, collisions could result and create a hazardous situation for
both personnel and equipment.
4.2.5 Program the Robot to Incorporate 50% Compliance Travel of the Tool
Program the robot to have the tool's compliance at 50% travel when on the nominal path.
As the part's edge deviates from the perfect path, the cutting bit can use compliance to follow along
high and low spots without losing contact or hitting the positive stop and gouging.
Do not "bottom out" the compliance and hit the positive stop.
Repeated impact on the positive stop creates "slop" in the compliance and reduces recentering.