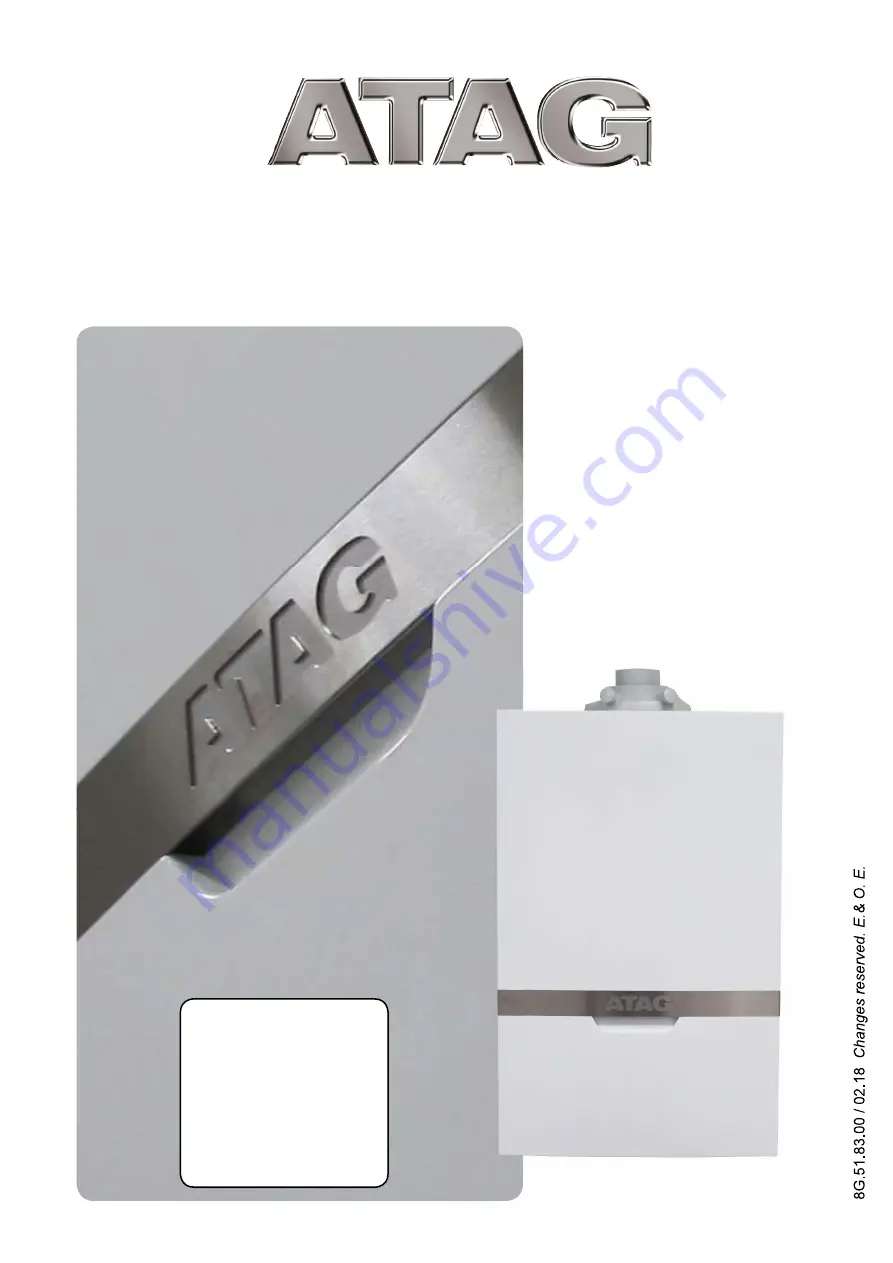
I n s t a l l a t i o n & S e r v i c i n g
Instructions
These instructions are to be retained by the user.
iC
24
iC
28
iC
36
iC
40
iC
Economiser Plus
27
iC
Economiser Plus
35
iC
Economiser Plus
39
Natural Gas Boilers
Boiler
G.C No
iC 24
47-310-19
iC 28
47-310-21
iC 36
47-310-23
iC 40
47-310-25
iC
Economiser Plus
27 47-310-27
iC
Economiser
Plus
35 47-310-29
iC
Economiser
Plus
39 47-310-31
CE PIN 0063CQ3634
Summary of Contents for iC 24
Page 33: ...Installation Servicing instructions ATAG iC Range 33 Figure 10 7 a 10 9 Electrical diagram...
Page 56: ...Installation Servicing instructions ATAG iC Range 56 Annex C Short parts list...
Page 57: ...Installation Servicing instructions ATAG iC Range 57...
Page 58: ......
Page 59: ......
Page 60: ......
Page 61: ......