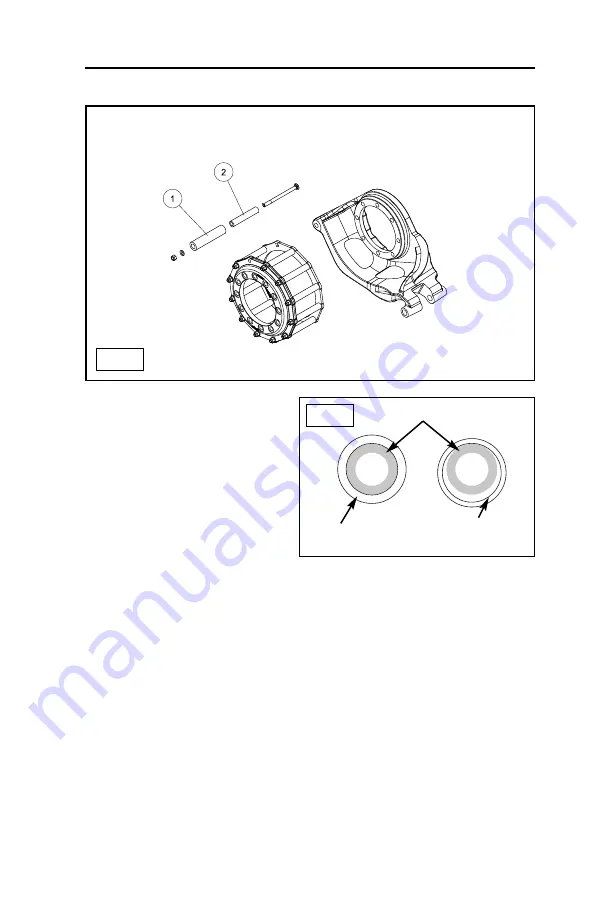
7 MAINTENANCE
85
7.15 Drive Sprocket Rollers
Compact Track Loaders use rollers on
each drive tooth of the drive sprock-
ets. These rollers help minimize fric-
tion between lugs on the track and
the sprocket. Sprocket rollers should
be treated as wear items that are
inspected regularly and replaced as
needed.
The rollers (1) rotate on steel pins (2),
limiting wear to the inside of the rollers. As they wear, the rollers become thinner,
but will continue to function and perform as long as they are rotating.
At 50 hour intervals, shut the machine down as described in section 5.13 and
visually inspect rollers. Replace any that show signs of cracking or wear-through.
Drive sprocket removal and roller / pin replacement should be performed by your
local VT-70 High Output dealer.
Steel Pin
New Roller
Normal Roller Wear
at 50% life
7.15-1
7.15-2
VT-70 High Output US ISO O&M
0404-853 2019-09
Summary of Contents for VT-70
Page 8: ...6 VT 70 High Output US ISO O M 0404 853 2019 09 This Page Intentionally Left Blank ...
Page 30: ...28 VT 70 High Output US ISO O M 0404 853 2019 09 This Page Intentionally Left Blank ...
Page 32: ...30 VT 70 High Output US ISO O M 0404 853 2019 09 This Page Intentionally Left Blank ...
Page 38: ...36 VT 70 High Output US ISO O M 0404 853 2019 09 This Page Intentionally Left Blank ...
Page 56: ...54 VT 70 High Output US ISO O M 0404 853 2019 09 This Page Intentionally Left Blank ...
Page 58: ...56 VT 70 High Output US ISO O M 0404 853 2019 09 This Page Intentionally Left Blank ...
Page 68: ...66 VT 70 High Output US ISO O M 0404 853 2019 09 This Page Intentionally Left Blank ...
Page 76: ...74 VT 70 High Output US ISO O M 0404 853 2019 09 This Page Intentionally Left Blank ...