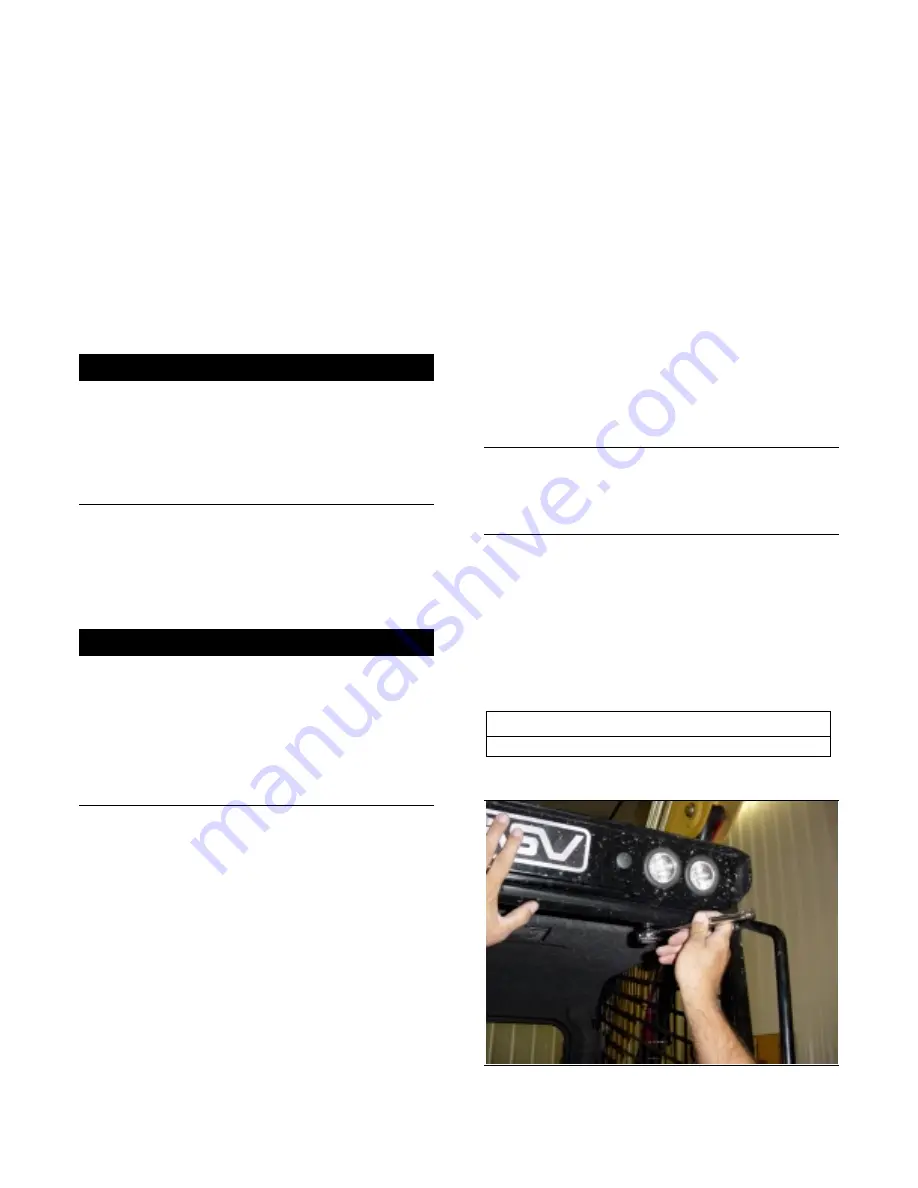
5-1
5. Dash & Lap Bar
Disassembly and Assembly
Chapter Overview
This chapter provides disassembly and assembly
procedures for the operator enclosure assembly.
Personal Safety
! WARNING !
Improper operation, lubrication, maintenance or repair
of this product can be dangerous and could result in
injury or death.
Do not operate or perform any lubrication, mainte-
nance or repair on this product until you have read
and understood the operation, lubrication, mainte-
nance and repair information.
Before starting any disassembly or assembly proce-
dures, refer to
Chapter 2. Product Safety – Basic
Precautions
for personal safety information.
Machine Preparation
! WARNING !
Accidental machine starting can cause injury or death
to personnel working on the machine.
To avoid accidental machine starting, disconnect the
battery cables from the battery and tape the battery
clamps and remove the key.
Place a “Do Not Operate” tag prominently on the ma-
chine to inform personnel that the machine is being
worked on.
Before starting any disassembly or assembly proce-
dures, refer to
Chapter 2. Product Safety – Repair
for machine preparation information.
Preliminary Checkout
If troubleshooting is required prior to disassembly or
assembly, refer to
Chapter 13. Troubleshooting
.
Operator Enclosure
Disassembly and Assembly
Procedures
Disassembly and assembly procedures are provided
for the following operator enclosure components.
•
Light Bar
•
Ignition Switch
•
Console Gauge/Warning Panel
•
Lap Bar Gas Assist Spring
Note:
Procedures are provided for only those operator
enclosure components listed above. However, information
for removal and installation of other operator enclosure
components can be obtained from the Rubber Track
Loader Parts List manual.
Light Bar Removal and
Installation
The tools required for light bar console removal and
installation are listed in Table 5-1. Use manufac-
turer-recommended tools whenever possible.
Table 5-1
Required Tools
Combination Wrench
Light Bar Removal
Figure 5-1