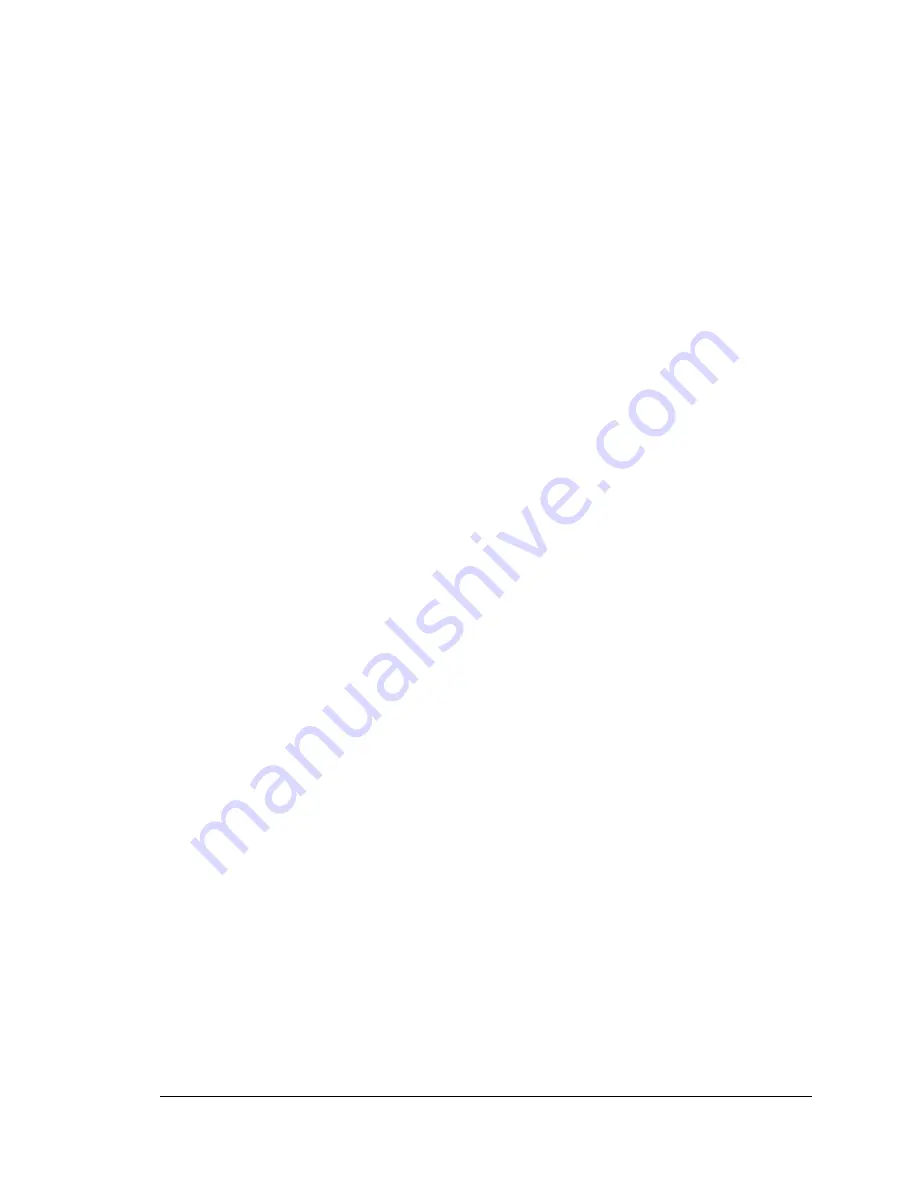
STERRAD
®
Sterilization System Routine Maintenance Guide
5
Chapter 1.
Introduction
The STERRAD
®
100S Sterilization System is a general purpose, low
temperature sterilizer using the STERRAD Process to inactivate
microorganisms on a broad range of reprocessable medical devices and
surgical instruments. This sterilizer offers an effective, safe, fast,
economical, easy to use, reliable, and flexible sterilization method.
A variety of routine maintenance procedures are performed on the
STERRAD 100S Sterilizer both at scheduled intervals and as needed.
These procedures are detailed in Chapter 3 of this guide.
You must read, understand, and follow the safety information presented
in Chapter 2 and throughout this guide. The safety information is
provided for your benefit and for the benefit of your instruments and
equipment.
Operation Information
This section provides a brief description of the operation of the
STERRAD 100S Sterilizer. More detailed information is found in the
STERRAD 100S Sterilization System User’s Guide and in the
STERRAD 100S FSE Troubleshooting Guide. The User’s Guide is
shipped with the system and is available by contacting the Customer
Care Center. The FSE Troubleshooting Guide is only available to those
persons who are trained to service STERRAD equipment by ASP
Technical Training. Please contact the ASP Customer Care Center for
more information: 1-888-STERRAD.
Note:
This following section presents a simplified
overview of the sterilizer components.