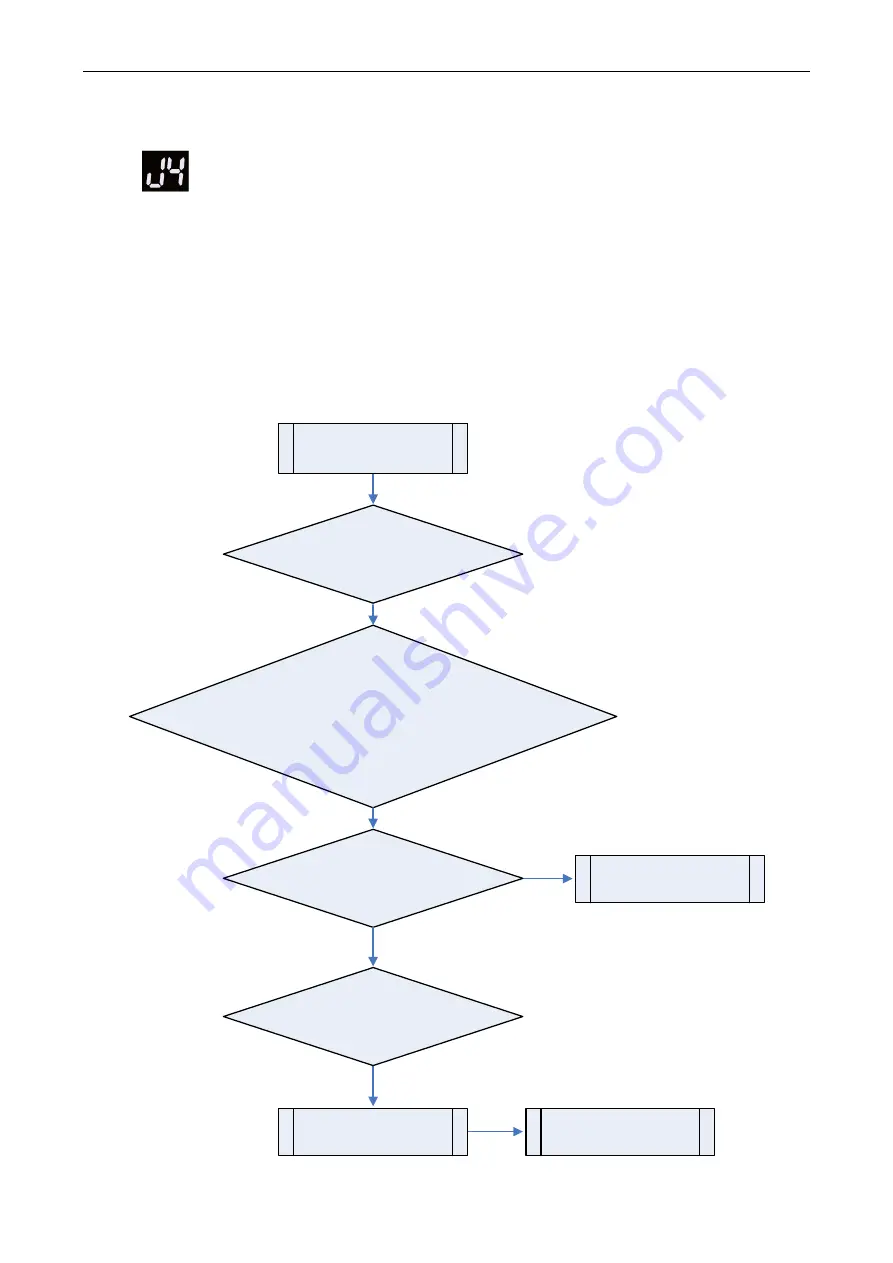
Gree GMV6 DC Inverter VRF Units Service Manual
141
2.95 "J4" Compressor 4 Over-current Protection
Fault display:
main board of outdoor unit, wired controller of indoor unit and receiver of indoor unit
display
Fault diagnosis:
When the operating current of the compressor detected by the current sensor or circuit exceeds the
limit, the unit will stop working.
Possible causes:
■ The unit's parameters are abnormal;
■ The drive module is abnormal;
■ The compressor is abnormal.
Troubleshooting:
"J4" Compressor 4
Over-current Protection
The co mpr essor is
abn ormal
Yes
Yes
Replace th e compre ssor
No
Replace th e d rive modu le
If th e h igh pressu re valu e o f th e u nit
is still a bove 60°C when the compre ssor runs at the lowest
frequen cy, the compre ssor may ha ve ena bled normal over-current
protection. In this case, check whether th e fan oper ate s prop erly an d
whether th e a mb ient temperature is n ormal and wh eth er the
power supply is normal (320V-460V)
Power on aga in
the units based on th e capa city
and nu mb er o f indoo r u nits enable d
previou sly in the case o f
protection state
Whether th e d rive modu le i s normal?
Yes
Yes
Is th e p rotection still occurring
afte r po we r-on?
Yes