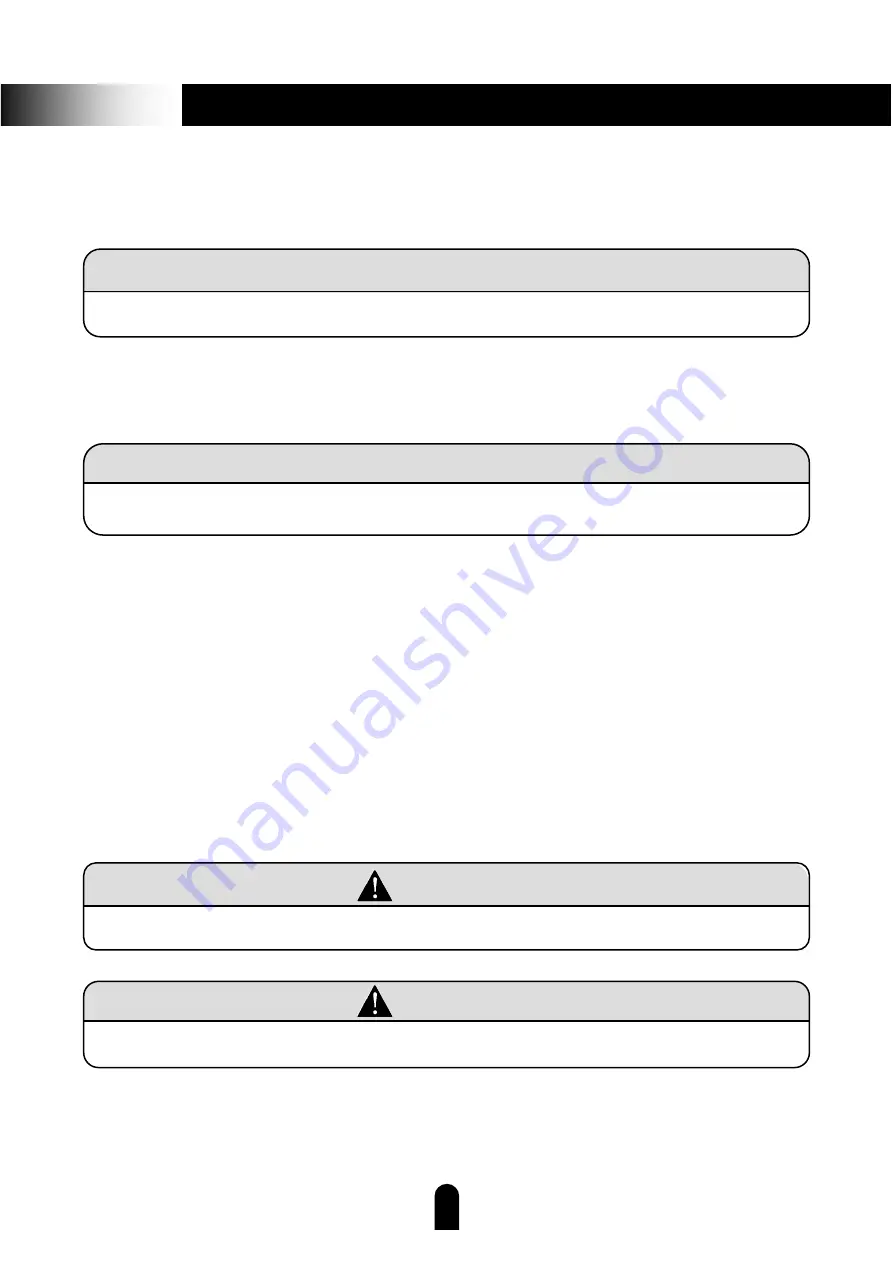
10
①
Operation
▲
Flushing the equipment before first use
Flush the equipment before first use. Check the fluid passage for leak at the same time. If there
is any leak, retighten using two (2) special spanner, putting one on the joint, the other on the base.
Remove foreign materials, as well.
Foreign materials, such as dust, contaminants, etc., may cause the nozzle to get
clogged, resulting in inconsistent spray pattern. Flush thoroughly.
Equipment Flushing Procedure
(1) Provide 3 liters of solvent (cleaning thinner).
Fill an empty can (fluid container) with solvent (cleaning thinner). Put the suction pipe into the can
and check to see that the suction filter is fully immersed in the solvent.
(2) Gradually open the air regulator (turn clockwise) and supply compressed air and then start
operation. Set the compressed air at about 0.1 MPa.
In order to prevent an air regulator from getting damage , unlock the handle of air
regulator before operate.
(3) Put the tip of spray gun into solvent and pull the trigger. Solvent circulates through the system,
purging air inside (which comes out in the form of bubbles).
This will clean the liquid passage through the system, hose and gun.
(4) Once passage cleaning is done, pull the suction pipe off the fluid can and run the pump idly to
completely remove residual solvent within the pump. And then close the air regulator (turn
counter-clockwise).
Now it’s ready for operation.
▲
Starting and adjusting the pump
(5) Provide a paint fluid can.
(6) Repeat Step (1) through (3), with paint fluid.
(7) Adjust the air regulator to keep compressed air pressure at 0.2 to 0.5MPa.
The fluid pressure of:
SP1636 is 20 times the compressed air pressure,
SP1628 is 30 times the compressed air pressure.
Therefore, when the ratio is:
1:20, fluid pressure will be 4MPa ~ 10MPa,
1:30. fluid pressure will be 6MPa ~ 15MPa or more, causing the pump to stop.
The fluid pressure can be 20, 30 times the operating air pressure, calling for
extra care when operating the pump.
(8)
Put the nozzle on the spray gun.
Ensure that spray gun’s trigger is locked. If you fail to do so, trigger could be
pulled accidentally, resulting in personal injury.
(9) Check to see that there is no leak from the joint between the painting equipment and hose.
If you find leak:
Bring the pressure down, Drain the fluid,
Then, locate the point of leakage, Retighten to fix the leak.
4
Operation
NOTICE
WARNING
WARNING
CAUTION