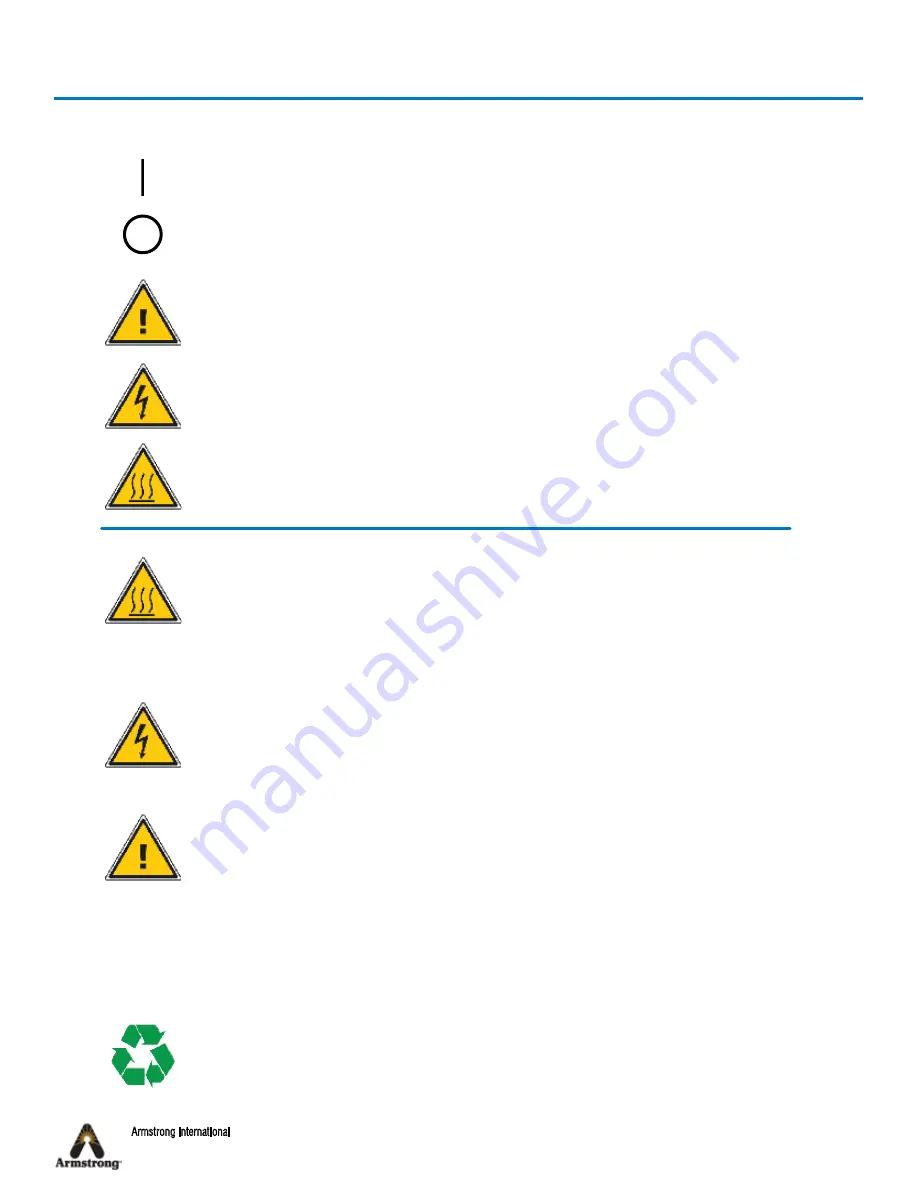
Armstrong International
IOM-246-V2.0
Steam QM-3 Calibration
Page 2 of 14
Safety
Icon Legend
Burn hazard! Uninsulated components upstream of cabinet may be hot.
•
Do not touch when unit is working.
•
Allow to cool before moving or servicing unit.
Live steam will cause burns; condensate water may cause them. Skin exposure
to 140 °F (60 °C) water for only five seconds may cause a second degree burn.
This device must be installed in accordance with appropriate local,
national, and international standards, codes, and practices.
Read this manual. It contains important information.
Service must be performed by a qualified person.
Installation should always be accompanied by competent
technical assistance.
Improper installation, start-up, operation, maintenance, or service
may void warranty.
You are encouraged to contact Armstrong International or its local
sales representative for additional information.
Shock hazard! High voltages present inside equipment.
•
Electrical installation must be performed by qualified personnel.
•
Disconnect power before performing any electrical service.
Equipment must be disposed of according to applicable
environmental requirements.
Indicates Power On
Indicates Power Off
Indicates important information concerning potential
for personal injury or damage to equipment
Indicates electrical hazard
Indicates hot surface
Keep unit away from heat-sensitive equipment and installations.