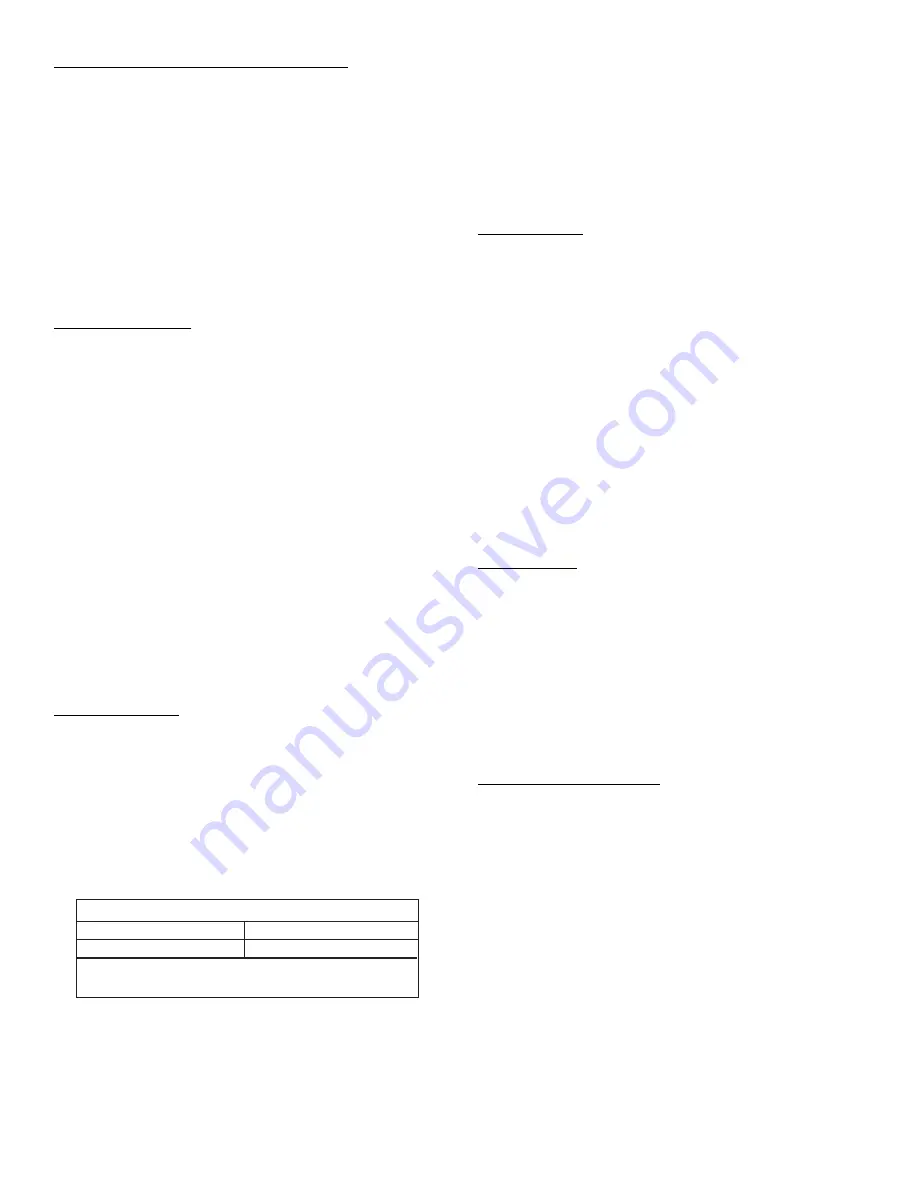
506318-01
Page 6 of 17
Issue 0946
Heat Pump Application with Electric Heat
Emergency Heat (heating heat pump)
If selector switch on thermostat is set to the emergency
heat position, the heat pump will be locked out of the heating
circuit, and all heating will be electric heat ( if applicable). A
jumper should be placed between W and E on the
thermostat so that the electric heat control will transfer to
the first stage heat on the thermostat. This will allow the
indoor blower to cycle on and off with the electric heat when
the fan switch is in the AUTO position.
* Add Jumper on Subbase (Optional)
Start-Up Procedure
1. Check to ensure:
!
Service valve and gage port caps are installed and
tightened.
!
Voltage supply at unit agrees with nameplate rating.
!
Field wiring connections are tight and factory wiring
has not been disturbed and are tight.
!
Indoor fan motor is on correct speed tap.
2. Set thermostat selector switch to OFF and fan control
switch to “Auto” is so equipped.
3. Close electrical disconnects to energize system.
4. Set room thermostat at desired temperature. Be sure
set point is below indoor ambient temperature.
5. Set the system switch of the thermostat on COOL (or
HEAT if applicable) and fan switch for continuous
operation (ON) or AUTO, as desired. There will be a 5
minute short cycle compressor delay on startup. Operate
unit for 15-20 minutes, then check the system refrigerant
charge.
6. Adjust refrigerant charge per “Adjusting Charge” section.
Adjusting Charge
Factory charge is shown on the rating label located on
the access panel.
All split system heat pumps are factory charged
for 15 feet of connecting line set and matched indoor
fan coil.
Nameplate refrigerant charge should initially be
adjusted for line set lengths other than 15 feet. For line
sets shorter than 15 feet in length, remove charge. For line
sets longer than 15 feet, add charge. Oil charge is sufficient
for all line lengths.
Before final adjustment is made to the refrigerant charge,
it is imperative that proper indoor airflow be established.
Airflow will be higher across a dry coil versus a wet coil.
Blower charts are calculated with a
dry or wet coil
basis.
Recommended airflow is
350-450 CFM per ton
(12,000
Btuh) through a
wet coil
. Refer to indoor unit instructions
for methods of determining air flow and blower performance.
All heat pump units are only rated with TXV installed on
indoor coil.
The optimum method for checking the charge is by
weight. However the following methods may be used
to confirm the proper charge:
Cooling Mode:
1. Operate unit a minimum of 10 minutes before
checking charge.
2. Measure liquid service valve pressure by attaching
an accurate gage to service port. Determine
saturation temp. from T/P chart.
3. Measure liquid line temperature by attaching an
accurate thermistor type or electronic thermometer
to liquid line near outdoor coil.
4. Calculate subcooling (saturation temp. measured
temp.) and compare with table on back of central
box cover.
5. Add refrigerant if subcooling is lower than table.
Recover refrigerant if subcooling is high.
6. If ambient temp is lower than 60°F, check charge in
heating mode or weigh refrigerant according to
name plate data.
Heating Mode
:
Check charge in heating mode if ambient temp is below
60° F. Indoor temp must be between 65° and 75° F.
Follow steps (1) to (6) above and compare with heating
mode subcooling range on the table on back of central box
cover.
Charge must be rechecked again during the cooling
season.
Cold Weather Application
A cold weather accessory kit may be required for heat
pumps operating at ambient conditions below 25°F.
Supplemental heat should be provided for these conditions
due to the expected performance degeneration.
Refrigeration Charge Adjustment
Liquid Line Diameter
Oz. Per Linear Foot *
3/8”
.6
* Factory charge for series is for 15’ (ft.) line sets
and matched fan coil.
Summary of Contents for 4HP13
Page 12: ...506318 01 Page 12 of 17 Issue 0946 ...
Page 13: ...Page 13 of 17 506318 01 Issue 0946 Defrost Control Board Diagnostic LEDs ...
Page 14: ...506318 01 Page 14 of 17 Issue 0946 H P 13 SINGLE PHASE WIRING DIAGRAM ...
Page 15: ...Page 15 of 17 506318 01 Issue 0946 H P 14 SEER WIRING DIAGRAM ...