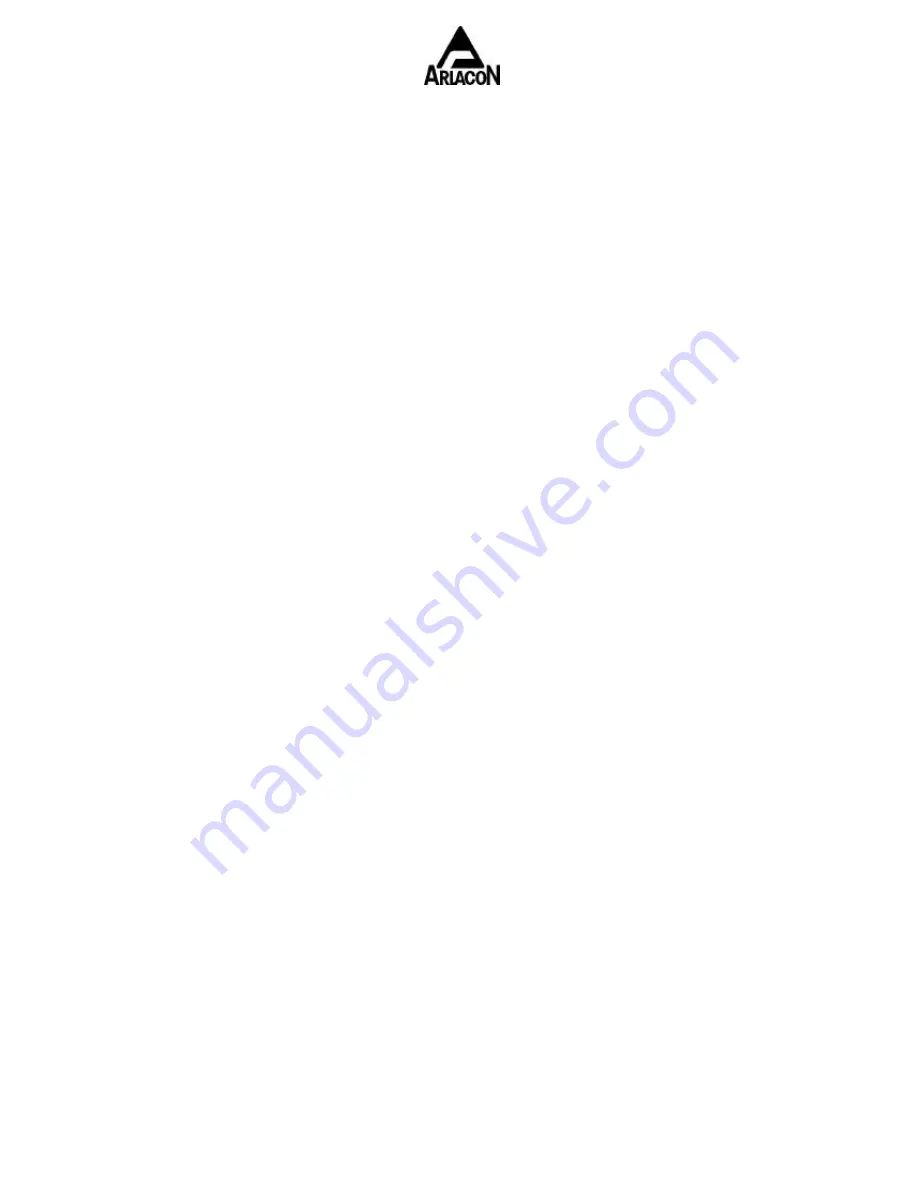
ARLACON MC300
MC300MAE
Control system
User's manual
30
Product code 1003418
PIDFREQ=500
RESX=125 ' 125 pulse edges/mm
MAXERRX=10 ' poserr >10mm cuts off servo
GAINX=100 ' gain
INTGX=0 : DERVX=0 : SCOMPX=0 ' others off
SPEEDX=200 ' 200 mm/s
ACCELX=400 ' 0.5 s ramp (200/400=0.5)
FILTERSIZEX=20 ‘ 40ms filter (20/500 seconds)
To start moving the X axis, use the PWRX=1 command to start position control. The amplifier
will go active and the position regulator will start holding the position.
To start a system with high speed capability, use a lower value, like PWRX=0.2 to limit the
regulator maximum output (max output = 10 x PWRX [volts]).
If the system is unstable, runs away from the set position and cuts off at MAXERR, check
encoder phasing and speed loop phasing.
To operate the REF output without the speed regulator, use the OPWRX= command.
When the position regulator is running, use the MOVE command to try moving the axis to new
positions.
Adjust the GAIN,DERV,INTG and SCOMP parameters for stable operation. For many systems
with tacho speed loop the parameters can be set by adjusting GAIN while leaving DERV, INTG
and SCOMP to 0 and then adding DERV if necessary.
After the feedback parameters are set, SCOMP may be set at a value corresponding the
speed of the axis when REF is 10V (this is called critical SCOMP). This will add a feedforward
part in the REF signal compensating for the known part of the speed reference during motion
and thus enabling accurate path control. Using a SCOMP value higher than the critical value
causes undercritical SCOMP that compensates only partly for the position lag when in motion.
To disable speed compensation, leave SCOMP at 0. Critical SCOMP also provides the fastest
point-to-point positioning. Undercritical or no SCOMP causes smoother operation at the end of
the motion to avoid overshoot.
INTG can be used to integrate the position error for minimum error at constant or zero speed.
The best INTG operation is achieved with high speed servo components and critical SCOMP.