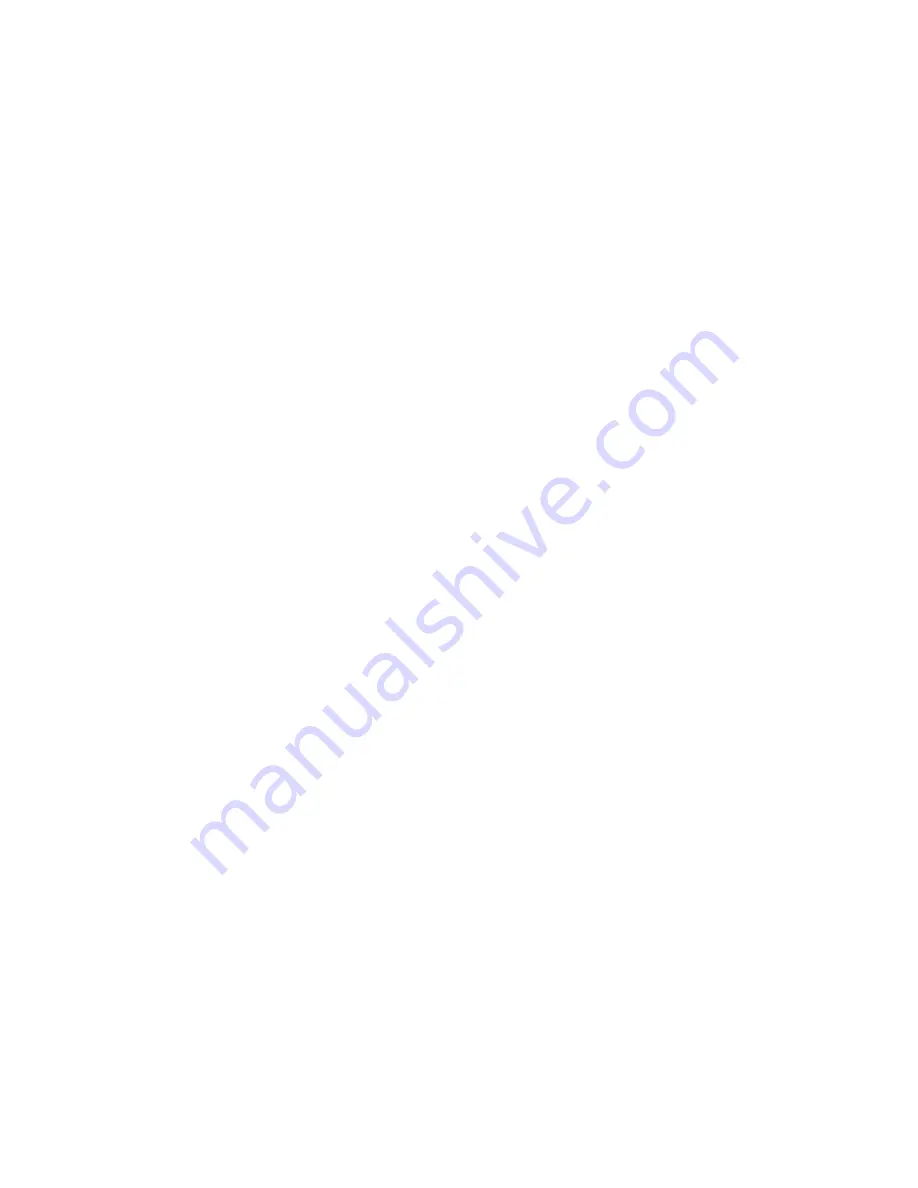
Fuselage Revisited:
At this time, we are going to add the lower wing fillets. At first glance these appear
daunting but are in reality quite simple to produce. First, select the softest sheet of 3/32”
balsa you have and cut out two sets of top and bottoms for the fillets. Now stand the
fuselage on it’s nose with the lower wing installed. Spray the inside (side which goes
against the fuselage) of one of the top fillet pieces with a mixture of water and ammonia.
Start to work the piece into a tight radius. Respray as you see fit and the piece will curl
right up. Now, put it in place against the lower wing and the fuselage. It should extend
out on the wing to about 1/8” shy of where the sheeting ends and the tail of the fillet
should line up with the bottom panel line on the fuselage. BE PAITENT! If you break
one, don’t despair as I broke one on my first try. Once you have it where you want it.
Tape and pin it in place and do the other side. Let these dry over night or longer. When
dry, remove your tape and pins. You now have a molded balsa fillet! Glue this (TO THE
FUSELAGE ONLY!) in place and add the two internal fill pieces and wet and add the
bottom cap. Once this assembly has dried, add a filler piece to the fillet where it butts
against the wing. Add another piece of filler to reinforce the front of the fillet and you are
done with the wooden part. Form the nose of the fillet out of litho plate using the pattern
provided. This will take patience. An alternative would be for you to make this piece
from fiberglass.
It is now time to install the firewall. This will vary according to the engine that you use.
The plans show the installation of a Brison 2.4. It will be worth your while to get all your
holes marked and drilled prior to gluing the firewall in place. Whatever you do, try and
rotate the engine so you will not have a hard interference between the carburetor and the
landing gear blocks. To get this placed correctly (with the Brison), set the firewall 1” back
into the box and epoxy it in place and install triangle stock for extra strength. Cut away
the former F1 until the engine sits flush against the firewall and then box the area where
the carb sits using scrap balsa. If you are building the late version shown on the plans
with the cut away cowl, you will have access to the carb for priming and choking. I made
my cowl out of fiberglass using blue Dow Board foam. I cut out enough rings to provide
the correct thickness, and then glued these together. Next I epoxied a piece of ½”
diameter wood dowel in the center. Take care to ensure that the dowel is truly centered
and vertical. Next I cut the cowl roughly to shape on my bandsaw. Then I chucked the
dowel in my drill press and shaped it using 80 grit sandpaper. I found it worked best to
use a long wide strip and allow only the paper (no backing) to contact the foam. Once
satisfied with the overall shape and diameter of the cowl, apply 3 layers of Bondo
Automotive fiberglass cloth (I cut up one whole package into 4” x 6” strips and kept
applying them with a min. of ½ “ overlap until gone) using epoxy resin and when set,
apply a coat of finishing resin. Chip out the foam you can and the rest can be removed
with lacquer thinner. Trim the opening to shape and add the cowl ring and the cowling is
ready to install. For those of you who feel that this sounds too much like work, a spun
aluminum cowl is now available from Arizona Model Aircrafters. Install the cowl with 6
evenly spaced mounting blocks and we can move on to some detail work.
Guns and Access Panels:
It is now time to start dressing up the SSW! I constructed my guns from Arizona Model
Aircrafter kits. Once these are complete, the next task is to build their mounts and shell
chutes. This is pretty straightforward. The guns base mount (M1) gets screwed to the rear
cabane strut mount. Once this is done glue M2 and M3 together as shown on the plans.
Trial fit these to M1 and check that the gun will rest upon it at the correct height. If all