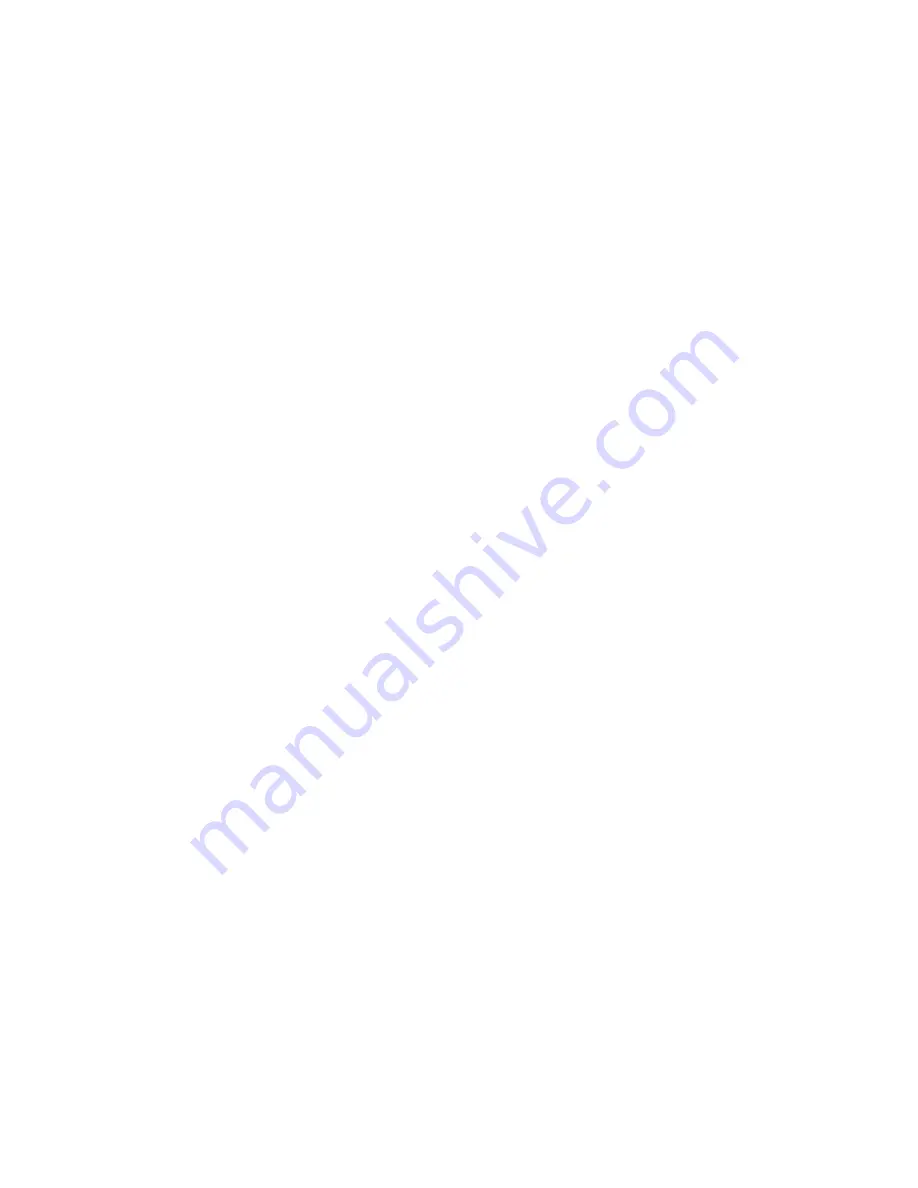
you can line up each louver on its centerline. Repeat the above procedure to reproduce the
louvers in the panel. Now drill two ¼” diameter holes in the appropriate location for the
landing gear legs. I installed this panel with five #0 screws on each side.
Dummy Engine:
Begin the dummy engine by cutting out the pieces which make up the crankcase and the
cam box. Glue these together and screw them to the cowl ring, which supported the real
engine. Cut away pieces until the dummy crankcase clears the engine. I was able to do
this and still keep all eleven cylinders visible from the front. Once this fits comfortably,
prime and paint it. Next, assemble eleven Williams Brothers ¼ scale Gnome Cylinders
but leave their heads and valve train off, as it is not correct for this model. Cut 11
plywood disks and drill holes in the location shown on the plans for the rocker arm
perches. Build up the valve area using left over pieces of the ¼” bass wood spars creating
¼” x ¼” x ¼” (slightly rounded after installation) valve holders. Drill through these on
the center of the valve bump 3/32”. I used small nails and #0 springs (from Ace
Hardware) for my valves and springs. 7 or 8 of these cylinders can now be installed
complete on your dummy crankcase. Cut the others to clear your engine installation.
Next, cut and drill out 22 rocker arms from 1/8” basswood as shown on the plan. These
can be painted once sanded. Now assemble the rocker perch post from brass tubing or
wood dowel. Slide two rockers on each and check one set with the inside of your cowl.
The rocker arms should be at roughly the same angle as the cowl is above them. Once
satisfied, glue in place and repeat for the other 10 sets. Install valve push rods made from
3/32” aluminum tube and you’re all set.
Final Assembly and Rigging:
You are now rapidly approaching the completion of this project! It is now time to make
the strut and wire fittings. Cut them from 1/32” brass using the templates shown on the
plans. I would recommend not drilling the holes in the strut fittings until after they are
bent to their U shape. Once they are bent insert a piece of wood into the fitting and drill
through. This way your holes will line up. One last thing I like to do is to solder a 4-40
nut on the side of the strut fitting which will face the fuselage. This helps speed the
assembly of the plane at the field. Debur and paint your fittings to suit your
documentation. I used aluminum high temperature engine paint, which I baked on, in my
oven. This has held up real well. You can now bolt all the fittings together. Sandwich the
flying wire brackets under the strut fittings. Next, assemble the model together. Due to
the thin wing section, chances are real good that your wings will have some warps in
them; mine did anyway! Either brace the wings in an unwarped, unsagged position or get
a helper to hold the wings true. While in this position, insert the struts in their fittings and
mark through the fittings onto the strut. Remove the strut and drill through a clearance
hole for a 4-40 bolt. Reinstall the strut and bolt it in place. Repeat on the other side. The
wings should now be set in a relatively unwarped fashion, you will probably note a bit of
droop (anhedral) at the tips however. This must be removed with the rigging. I use 80-
pound test, coated, fishing leader for my wires and small diameter aluminum tubes which
I crush and CA to swage the wires. Begin rigging the plane by installing the landing (strut
bottom to cabane) wires. This will remove the droop. You can use either turnbuckles or
Dubro 2-56 rigging couplers and clevises as adjusters on the detachable end of the wires.
Once all four landing wires are installed, next install the flying (strut top to fillet base)
wires and finally the drag (cowl to lower strut) wires. At this time check the balance of
the model. It should balance slightly nose down at a point 6-3/8” back from the leading
edge of the top wing.