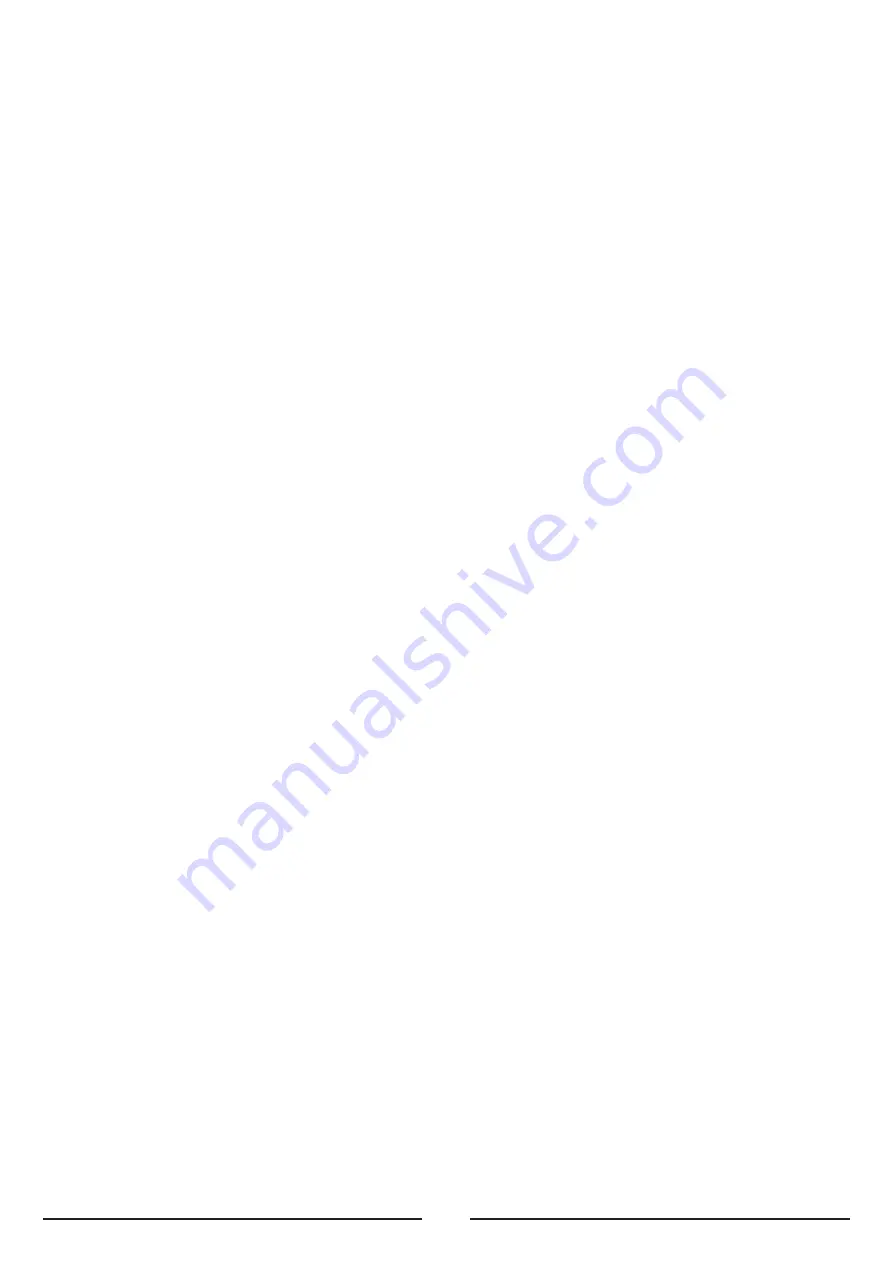
3
1.1
G
ENERAL
I
NSTRUCTIONS
Read the instructions and recommendations in these Installation Instructions
carefully to ensure proper installation, use and maintenance of the appliance.
Keep this manual in a safe place. You may need it for your own reference while our
Servicing Centre technicians or your installer may need to consult it in the future.
This is an appliance for the production of central heating (C.H.).
This appliance
must be used only
for the purpose for which it is designed.
The manufacturer declines all liability for damage caused by improper or negligent
use.
No asbestos or other hazardous materials have been used in the fabrication of this
product.
Before connecting
the appliance, check that the information shown on the data
plate and the table in section 7 comply with the electric, water and gas mains of the
property. You will find the data plate on the reverse of the control panel.
The gas with which this appliance operates is also shown on the label at the bottom
of the boiler.
Do not
install this appliance in a damp environment or close to equipment which
spray water or other liquids.
Do not place
objects on the appliance.
Do not allow
children or inexperienced persons to use the appliance without
supervision.
If you smell gas in the room,
do not turn on
light switches, use the telephone or any
other object which might cause sparks.
Open doors and windows immediately to ventilate the room.
Shut the gas mains tap (at or adjacent to the gas meter) or the valve of the gas
cylinder and call your Gas Supplier immediately.
If you are going away for a long period of time, remember to shut the mains gas tap
or the gas cylinder valve.
Always disconnect
the appliance either by unplugging it from the mains or turning
off the mains switch before cleaning the appliance or carrying out maintenance.
In the case of faults or failure
, switch off the appliance and turn off the gas tap. Do
not tamper with the appliance.
For repairs, call your local Authorised Servicing Centre and request the use of
original spare parts. For in-guarantee repairs contact MTS.
Check
the following at least once a year:
1 -
Check the seals for the water connections; replace any faulty seals.
2 -
Check the gas seals; replace any faulty gas seals.
3 - Visual check of the entire unit.
4 -
Visual check of the combustion process or analysis of combustion by-products
(see section 4.5) and cleaning of the burner if needed.
5 -
If called for by point. 3, dismantling and cleaning of the combustion
chamber.
6 -
If called for by point. 4, dismantling and cleaning of the burner jets.
7 -
Visual check of the primary heat exchanger:
-
check for overheating in the blade assembly;
-
clean the exhaust fan if needed.
8 -
Adjustment of the flow rate of the gas: flow rate for lighting, partial load and full
load.
9 -
Check of the heating safety systems:
-
safety device for maximum temperature (overheat thermostat);
-
safety device for maximum pressure (safety valve).
10- Check of the gas safety systems:
-
safety device for lack of gas or flame ionisation (detection
electrode);
-
safety device for gas cock.
11- Check of the electrical connection (make sure it complies with the instructions
in the manual).
12- General check of the combustion by-products of the discharge/ventilation
system.
13- Check of the general performance of the unit.
Summary of Contents for microSYSTEM 10 RFFI
Page 11: ...FIG 2 13 11 FIG 2 12...