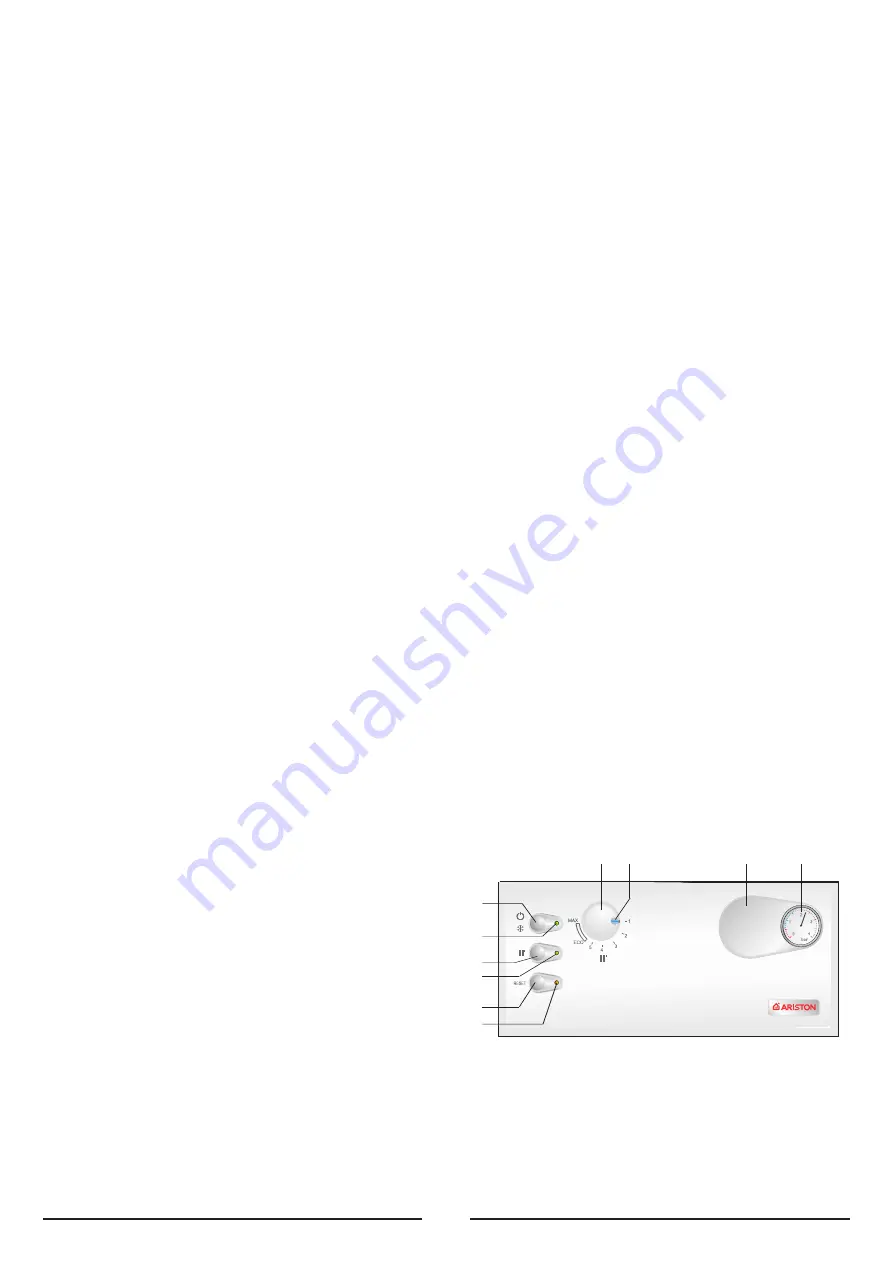
A
B
C
D
E
F
IL
GH
L
EGEND
:
A
- On/Off button
B
- On/Off L.E.D. green (frost protection active)
C
- Central Heating button
D
- Cental Heating active L.E.D. green
E
- Ignition failure (lockout) and/or overheat reset button
F
- Ignition failure (lockout) and/or overheat L.E.D. red
G
- Central heating temperature adjustment
H
- Energy Saving System (ESS)
I
- Knock-out for time clock
J
- Heating system pressure gauge
4.2
C
ONTROL
P
ANEL
F
IG
. 4.1
15
Close all air release valves on the central heating system.
Gradually open valve(s) at the filling point (filling-loop) connection to the central
heating system until water is heard to flow, do not open fully.
Open each air release tap starting with the lowest point and close it only when
clear water, free of air, is visible.
Purge the air from the pump by unscrewing anticlockwise and removing the
pump plug and also manually rotate the pump shaft in the direction
indicated by the pump label to ensure the pump is free.
Refit the pump plug.
Continue filling the system until at least 1.5 bar registers on the pressure gauge.
Inspect the system for water leaks and remedy any leaks discovered.
G
AS
S
UPPLY
:
Inspect the entire installation including the gas meter and test for soundness. The
gas installation should be in accordance with the relevant standards. In GB this is
BS6891 and in IE this is the current edition of I.S.813.
If the gas supply for the boiler serves other appliances ensure that an adequate
supply is available both to the boiler and the other appliances when they are in
use at the same time.
Pipe work must be of an adequate size. Pipes less than the 22mm should not be
used.
Open the gas cock (supplied with the connection kit) to the appliance and check
the gas connections on the appliance for leaks.
When the installation and filling are completed, flush the system while cold, refill,
turn on the Central Heating system (Section 4.4) and run it until the temperature
has reached the boiler operating temperature.
The system must then be immediately flushed through.
The flushing procedure must be in line with BS 7593:1992 code of practice for
treatment of water in domestic hot water central heating systems.
During this operation, we highly recommend the use of a central heating flushing
detergent (Fernox Superfloc or equivalent), whose function is to dissolve any foreign
matter that may be in the system.
Substances different from these could create serious problems to the pump or
other components.
The use of an inhibitor in the system such as Fernox MB-1 or equivalent is strongly
recommended to prevent corrosion (
sludge
) damaging the boiler and system.
Failure to carry out this procedure may invalidate the appliance warranty.
For IE it is necessary to complete a “Declaration of Conformity” to indicate
compliance to I.S.813. An example of this is given in the current edition of I.S.813.
In addition it is necessary to complete the “Benchmark” Log Book.
Summary of Contents for microSYSTEM 10 RFFI
Page 11: ...FIG 2 13 11 FIG 2 12...