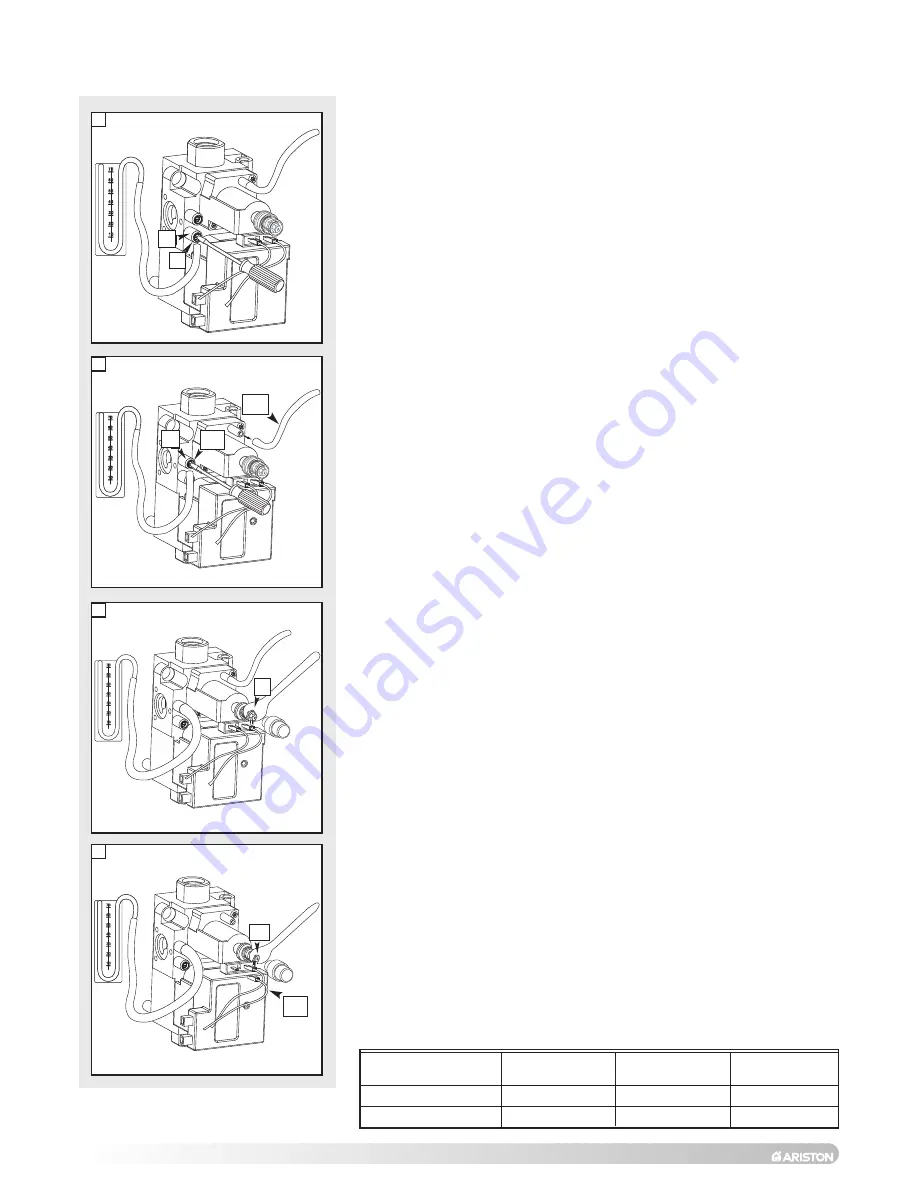
28
4.2
A
DJUSTING THE
G
AS
V
ALVE
(H
ONEYWELL
)
A
A
B
B
C
D
1
2
Recommended pressure for
soft-light ignition
8 mbar
NATURAL GAS (G20)
BUTANE GAS (G30)
PROPANE GAS (G31)
16 mbar
16 mbar
6.7 mbar
12 mbar
12 mbar
23 Kw
27 Kw
E
F
3
4
Setting the minimum and the maximum power of the boiler
1. Check that the supply pressure and dynamic pressure to the gas valve is
a minimum of 20 mbar for natural gas.
2. To do this, loosen the screw “A”.
Fit the pipe of the pressure gauge to the inlet pressure connection of the
gas valve
“B” check for the correct standing pressure, then operate the
appliance and check for the correct working pressure.
When you have completed this operation, replace the screw
“A” securely
into its housing to seal off the gas (check for tightness).
3. To check the pressure supplied by the gas valve to the burner, loosen the
screw
“C”. Fit the pipe of the pressure gauge to the pressure outlet test
point of the gas valve
“D”.
Disconnect the compensation pipe
“D1” either from the gas valve or from
the sealed chamber.
4. Push the On/Off button to “ON” position -green light- and ensure that the
hot water temperature control knob is set to maximum.
Turn on the boiler by running a hot water tap.
Adjust the 10mm nut
“E” on the modureg to set the maximum gas
pressure, turn the nut clockwise to increase and anti clockwise to
decrease the pressure until the required pressure is achieved (see
T
ABLE
A page 30)
5. To set the minimum power, disconnect a supply terminal “F1” from the
modureg and adjust screw
“F” (ensure the 10mm nut is held in position).
Turn the screw clockwise to increase the gas pressure and counter-
clockwise to decrease the gas pressure (displayed on the
pressure gauge) corresponding to the minimum power (see
T
ABLE
A page
30).
6. When you have completed the above operations, tur n off the
hot water tap, re-connect the supply ter minal to the modureg
on the gas valve and replace the cap on the screw of the
modureg.
Setting the maximum heating circuit power
7. To set the maximum heating circuit power, push the On/Off button to the
“ON” position -green light- and push the Heating button and set the time
clock and any external controls to the “ON” position -green light. Turn the
knob of the heating thermostat clockwise to maximum.
8. Remove the inspection panel of the P.C.B. and fit a small cross-head
screwdriver in to the right hand potentiometer (see page 28). Turn
clockwise to increase the pressure or counter-clockwise to reduce the
pressure. Adjust the setting to the required heating pressure value
(displayed on the pressure gauge), as indicated in the charts shown on
pages 30 amd 31.
9. Turn off the boiler by placing the main switch to the "OFF" position.
Setting pressure for soft ignition.
Disconnect the detection electrode connection close to the P.C.B.
(F
IG
.
11.14).
Start the boiler and during the ignition sequence adjust the left hand
potentiometer until the gas pressure reads the required gas pressure as
per the table below.
Once the gas pressure is set turn off the boiler and re-connect the
connection to the P.C.B.
NB.: It may be necessary to reset the flame failure reset a number of
times during this operation.
10. Remove the pipe from the test point and tighten the screw “C” to the
pressure test point in order to seal off the gas.
11. Carefully check the pressure test points for gas leaks (valve inlet and
outlet).
IMPORTANT!
Whenever you disassemble and reassemble the gas connections, always
check for leaks using a leak detection fluid.
N
OTE
:
ALWAYS CHECK THE GAS RATES FOLLOWING ADJUSTMENT
.
B
C
E
F
D
D1
F1
A
Summary of Contents for MICROCOMBI 23 MFFI
Page 45: ...45...
Page 46: ...46...
Page 47: ...47...
Page 48: ...48...
Page 49: ...49 8 SHORT SPARE PARTS LIST microCombi 23 27 MFFI...
Page 51: ...51 NOTES...