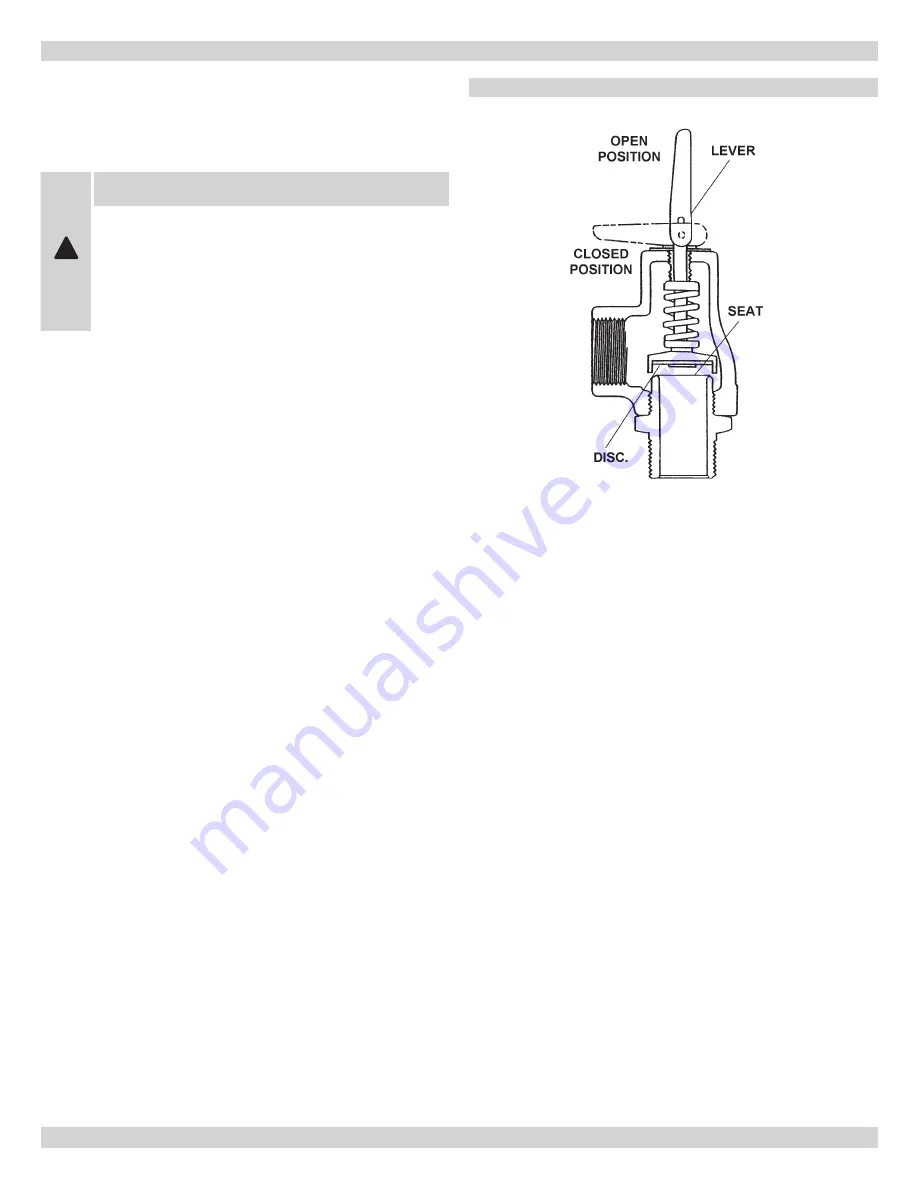
17
Hydronic block requires only minimum of periodic
maintenance. Preventive maintenance tasks
described below are not difficult and when done
annually, will aid unit to continue its trouble free
operation.
Boiler is designed to provide years of trouble free perfor-
1.
mance under normal operating conditions. Owner should
conduct general external examination at beginning of
each heating season and at mid-heating seating sea-
son to assure good working performance continues. A
qualified service technician should examine at least once
every year.
Do not store anything against boiler or allow dirt or
2.
debris to accumulate in area immediately surrounding
boiler.
Elements will burn out if not filled with water when
3.
electrical power is turned on. Do not connect thermo-
stat wire until system has been filled with water. Drain
water out of system only when absolutely necessary
to make repairs or prevent freeze-up during extended
cold weather shutdown.
Temperature and pressure gauge should be checked
4.
frequently. During normal operating conditions, pres-
sure should be stable throughout heating season. If
pressure under normal operating conditions consis-
tently rises and falls over period of time, this can indi-
cate fill valve leak, system leak, or compression tank
malfunction. Leaks anywhere must be repaired without
delay. If leaks or significant pressure fluctuations are
observed, call for service immediately.
Check pressure relief discharge piping to assure
5.
discharged water will be properly routed to suitable
container or drain. Manually operate pressure relief
valve by pulling lever at end of valve until lever is in
line with center-line of valve. (Figure 9) Close valve
to avoid losing excessive amount of water. Repeat
this procedure several times on quick cycling basis
to release any sediment that could block relief valve
pressure sensing mechanism. On heating system using
manual water make-up or feed mechanism, do not to
allow system pressure to drop to 0 PSI when cycling
relief valve. Allowing condition to occur could cause
air to enter system requiring purging as described in
“Startup and Seasonal Maintenance" on page 15.
figurE 9
If relief valve fails to close completely after cycling,
remove it for cleaning or replacement. Turn off power
to boiler and isolate hydronic block by shutting off inlet
and outlet gate valves. Reduce water pressure to zero
by opening relief valve. Remove relief valve and inspect
valve disc and seat. Cleaning parts with clean lint free
cloth may be all that is necessary. If this procedure
fails replace valve with new one of equal pressure and
discharge rating. After installing cleaned or new relief
valve, open gate valves and follow procedure described
in “Startup and Seasonal Maintenance" on page 15.
Inspect and check field entrance wire connections
6.
to unit for any signs of looseness or over heating.
Verify wire lugs are tight and torqued to manufacture
recommended settings - see Table B.
mAinTEnAncE
!
CAUTION
Turn off main power switch to block at main
service entrance before any work requiring
removal of cover is done for safety. All work
shall be performed by qualified service
personnel familiar with unit's control system
operation.