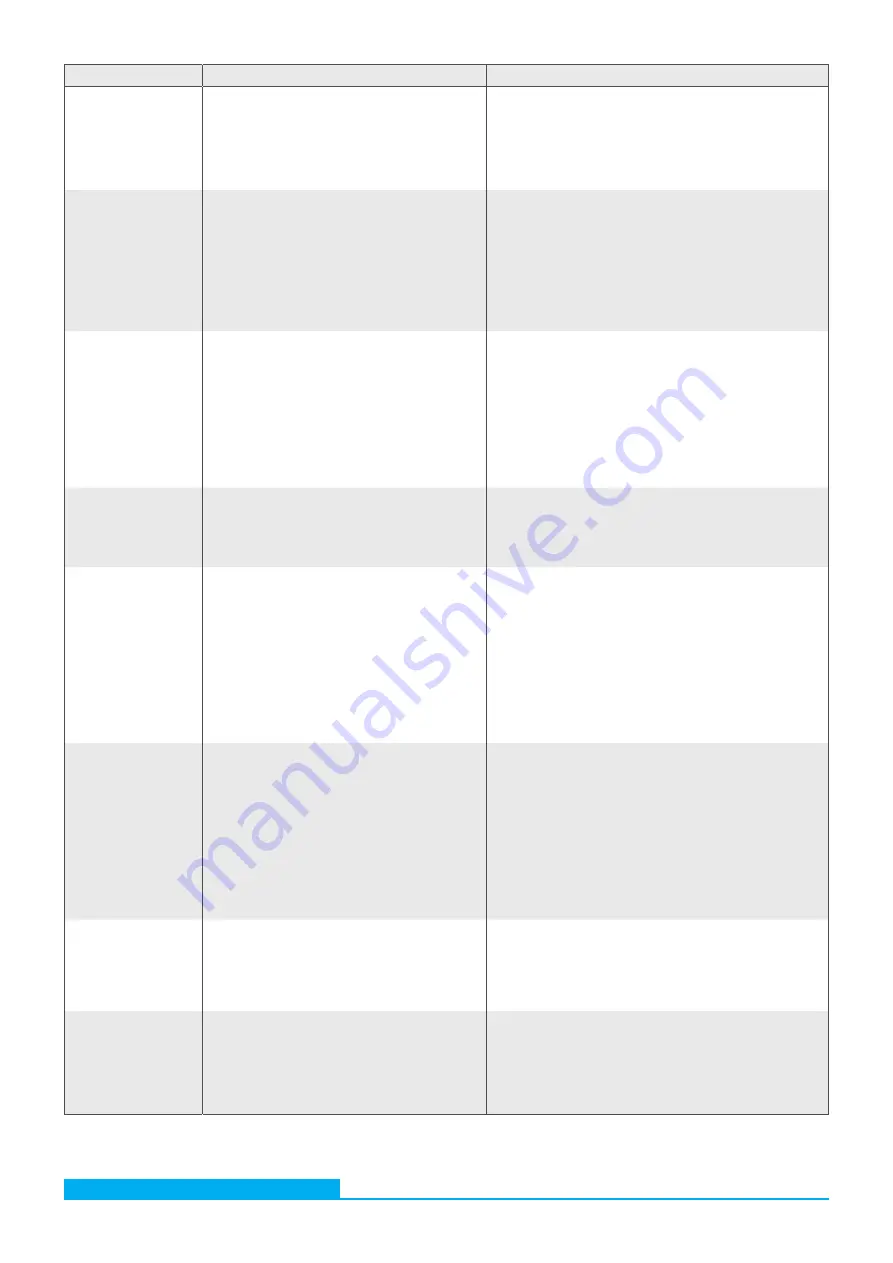
Subject to change · UMPC 045_31168300 · 0717 · EN
Page 38
www.argo-hytos.com
Error
Reason
Measure
E-motor can not be
switched on during
commissioning
›
E-cable or plug defective
›
Missing mains voltage
›
Motor defective
›
Pump defective
›
Too high viscosity (medium)
›
Have the cables disconnected by qualified personnel
›
Establish power supply / activate electrical fuse
›
Replace motor (repair at manufacturer)
›
Replace pump (repair at manufacturer)
›
Heat medium
E-motor switches off
during operation
›
Filter element contaminated
›
Suction strainer contaminated
›
Viscosity too high
›
Suction height too great
›
Leakage on the suction side
›
Wear of the pump
›
Replace filter element
›
Replace the suction strainer
›
Heat medium
›
Adjust suction height
›
Replace the suction hose or seal the connection points
(retighten them)
›
Replace pump (repair at manufacturer)
Too loud operating
noise
›
Filter element contaminated
›
Suction strainer contaminated
›
Viscosity too high
›
Suction height too great
›
Leakage on the suction side
›
Filter unit is mounted on a vibration-sensitive
base (sheet metal)
›
Replace filter element
›
Replace the suction strainer
›
Heat medium
›
Adjust suction height
›
Replace the suction hose or seal the connection points
(retighten them)
›
Improve your local conditions
Pump does not suck
›
Leakage on the suction side
›
Sealing plug of the screen element is leaking
›
Unit is pumped empty (when refilling)
›
Replace the suction hose or seal the connection points
(retighten them)
›
Check / replace sealing ring, check tightening torque
›
Prime the unit (0.5 l to 3 l)
Cleanliness classes
displayed on the
LubMon Visu do not
change during
cleaning
›
Max. dirt capacity of the filter element is
reached
›
Leakage at the suction hose, falsification of
the measurement results by free air in the oil
(air bubbles)
›
Rotary valve on lever position "Pumping"
›
Replace filter element
›
Check the suction connection, if necessary, tighten the
hose clips / check the oil for foaming or air bubbles and
eliminate the cause.
If the cause cannot be eliminated, take the oil sample
and have it evaluated in the laboratory. Vent the filter
unit
›
No particle counting is possible with the lever position
"Pumping"
Cleanliness classes
displayed on the
LubMon Visu become
poorer during
cleaning
›
Max. dirt capacity of the filter element is
reached
›
Leakage at the suction hose, falsification of
the measurement results by free air in the oil
(air bubbles)
›
Rotary valve on lever position "Pumping"
›
Replace filter element
›
Check the suction connection, if necessary, tighten the
hose clips / check the oil for foaming or air bubbles and
eliminate the cause.
If the cause cannot be eliminated, take the oil sample
and have it evaluated in the laboratory. Vent the filter
unit
›
No particle counting is possible with the lever position
"Pumping"
Displayed cleanliness
classes are not
plausible
›
Viscosity range below or exceeded. Particle
counter is supplied with too little or too
much oil
›
Rotary valve on lever position "Pumping"
›
Adjust the fluid temperature (also see operating
conditions)
›
No particle counting is possible with the lever position
"Pumping"
After cleaning for
high cleanliness
classes no further
improvement (e.g.
order number 10 at
4, 6 and 14 μm).
›
Set measuring time is too short
›
Observe the defined limit values for oils with
cleanliness classes according to ISO 4406.
Upper limit value: 24 (for 4, 6 and 14 µm)
Lower limit value: 10 (for 4, 6 and 14 µm)
Table 7: Error description