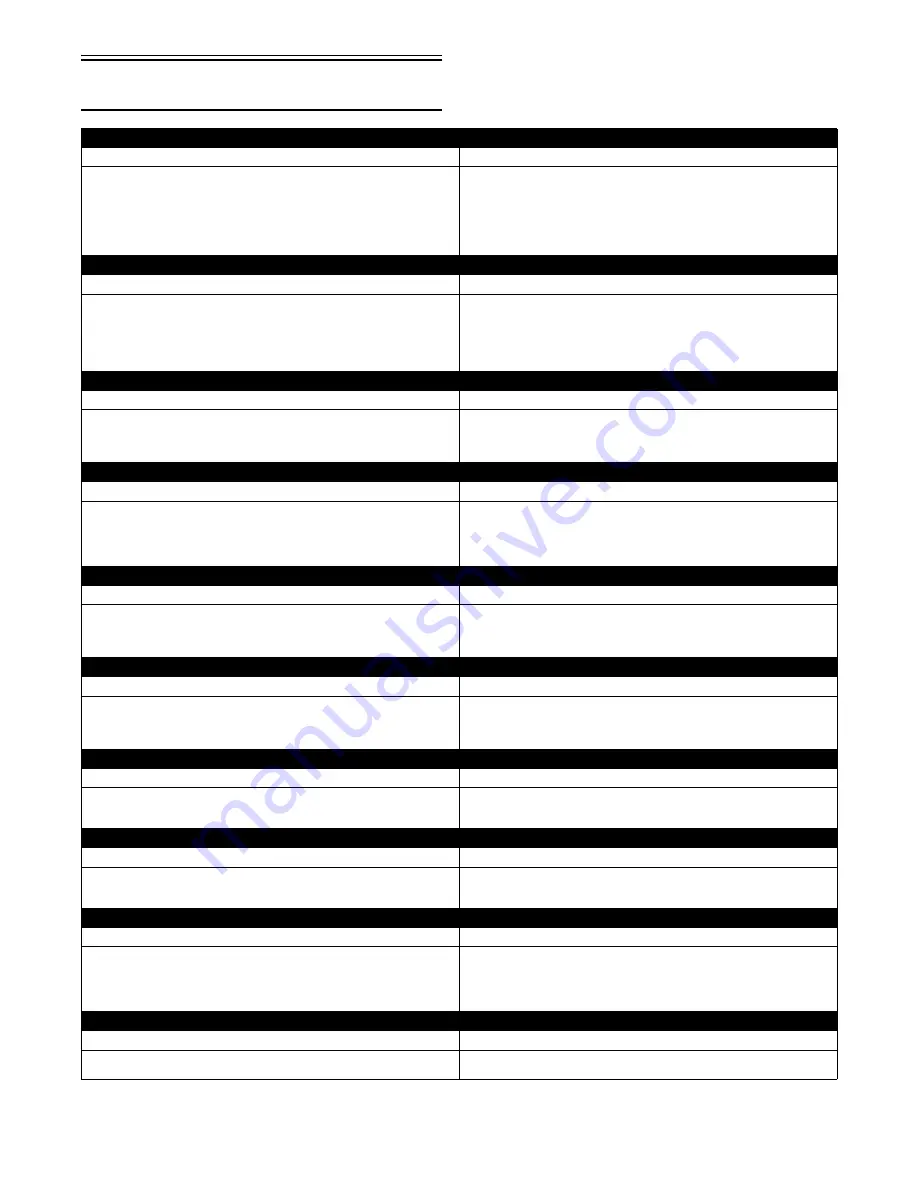
28
Troubleshooting
Problem: Engine will not start or is hard to start (Compression too low)
Condition
Remedy
1.
Valve clearance
out of adjustment
2.
Valve guides
worn - seated poorly
3.
Valves
mistimed
4.
Piston rings
worn excessively
5.
Cylinder bore
worn
6.
Spark plug
seating poorly
7.
Starter motor
cranks too slowly - does not turn
1. Adjust clearance
2. Repair - replace guides
3. Adjust valve timing
4. Replace rings
5. Replace cylinder
6. Tighten plug
7. See Electrical System
Problem: Engine will not start or is hard to start (No spark)
Condition
Remedy
1.
Spark plug
fouled
2.
Spark plug
wet
3.
Magneto
defective
4.
CDI unit
defective
5.
Ignition coil
defective
6.
High-tension lead
open - shorted
1. Clean - replace plug
2. Clean - dry plug
3. Replace magneto
4. Replace CDI unit
5. Replace ignition coil
6. Replace high tension lead
Problem: Engine will not start or is hard to start (No fuel reaching the carburetor)
Condition
Remedy
1.
Gas tank cap
obstructed
2.
Carburetor inlet needle
defective
3.
Fuel hose
obstructed
4.
Fuel screens
obstructed
1. Clean or replace cap
2. Replace needle
3. Clean - replace hose
4. Clean - replace inlet screen - valve screen
Problem: Engine stalls easily
Condition
Remedy
1.
Spark plug
fouled
2.
Magneto
defective
3.
CDI unit
defective
4.
Carburetor jets
obstructed
5.
Valve clearance
out of adjustment
1. Clean plug
2. Replace magneto
3. Replace CDI unit
4. Clean jets
5. Adjust clearance
Problem: Engine noisy (Excessive valve chatter)
Condition
Remedy
1.
Valve clearance
too large
2.
Valve spring(s)
weak - broken
3.
Rocker arm
- rocker arm shaft worn
4.
Camshaft
worn
1. Adjust clearance
2. Replace spring(s)
3. Replace arm - shaft
4. Replace camshaft
Problem: Engine noisy (Noise seems to come from piston)
Condition
Remedy
1.
Piston - cylinder
worn
2.
Combustion chamber carbon
buildup
3.
Piston pin - piston pin
bore worn
4.
Piston rings - ring groove(s)
worn
1. Replace - service piston - cylinder
2. Clean chamber
3. Replace - service pin - bore
4. Replace rings - piston
Problem: Engine noisy (Noise seems to come from timing chain)
Condition
Remedy
1.
Chain
stretched
2.
Sprockets
worn
3.
Tension adjuster
malfunctioning
1. Replace chain
2. Replace sprockets
3. Repair - replace adjuster
Problem: Engine noisy (Noise seems to come from crankshaft)
Condition
Remedy
1.
Bearing
worn - burned
2.
Lower rod-end bearing
worn - burned
3.
Connecting rod side clearance
too large
1. Replace bearing
2. Replace bearing
3. Replace thrust washer(s)
Problem: Engine noisy (Noise seems to come from transmission)
Condition
Remedy
1.
Gears
worn - rubbing
2.
Splines
worn
3.
Primary gears
worn - rubbing
4.
Bearings
worn
5.
Bushing
worn
1. Replace gears
2. Replace shaft(s)
3. Replace gears
4. Replace bearings
5. Replace bushing
Problem: Engine noisy (Noise seems to come from secondary-transmission/right-side cover)
Condition Remedy
1.
Gears - shaft(s)
worn
2.
Bearing(s)/bushing(s)
damaged
1. Replace gears - shafts
2. Replace bearing(s)/bushing(s)
Summary of Contents for Altera 300
Page 1: ...2017 S SERVICE ERVICE MANUAL ANUAL www arcticcat com ...
Page 99: ...98 NOTES ...
Page 100: ...99 NOTES ...
Page 101: ...100 NOTES ...