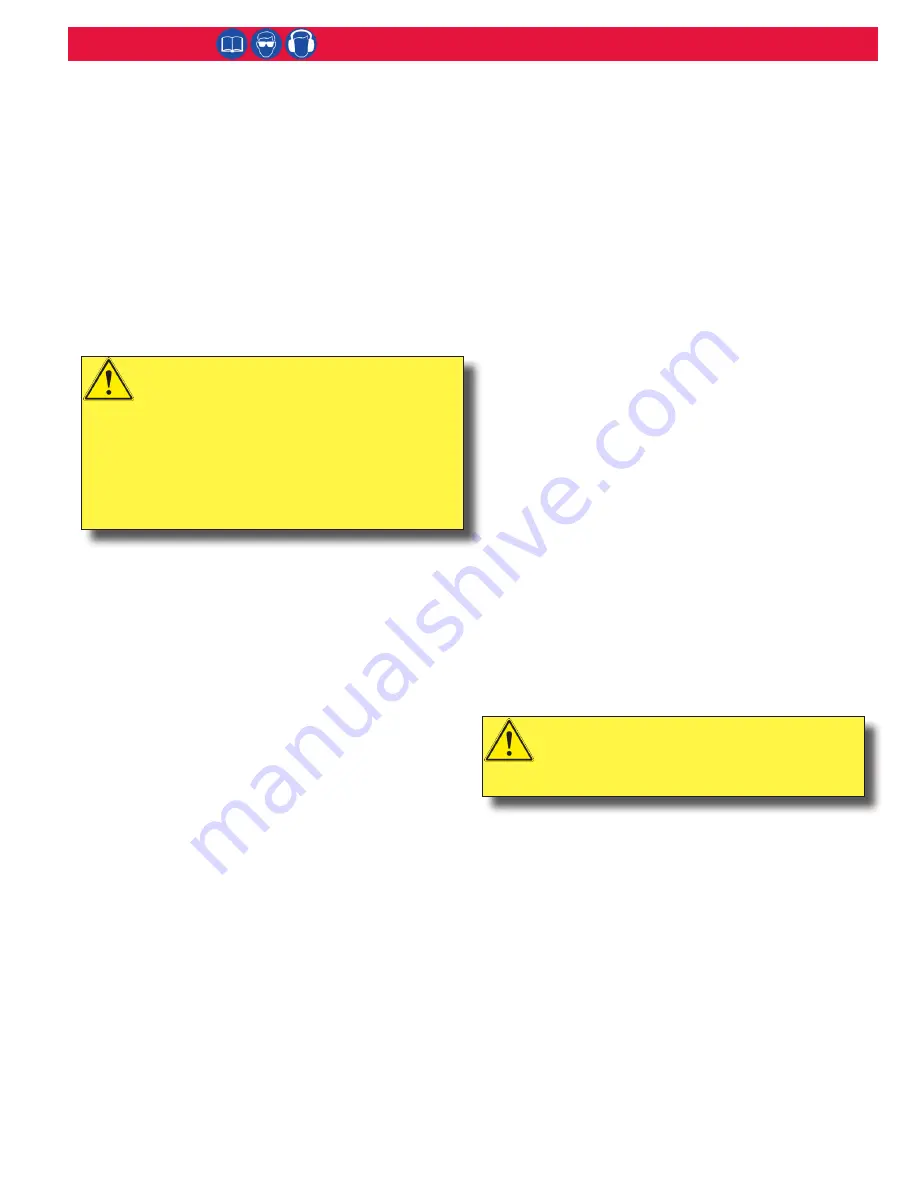
9
2012 series Pneudraulic Installation Tool (HK969)
GENERAL
The operating efficiency of your tool is directly related to
the performance of the entire system. Regular inspection
and the immediate correction of minor problems
will keep the tool operating efficiently, and prevent
downtime. A schedule of “preventive” maintenance of
the tool, nose assembly, hoses, trigger and control cord,
and Powerig®
hydraulic power source will ensure proper
operation of the tool and extend its life.
NOTE: Huck tools should be serviced only by
personnel who are thoroughly familiar with its
operation.
- Service the tool in a clean, well-lighted area. Take
special care to prevent contamination of pneumatic
and hydraulic systems.
- Have available all necessary hand tools (standard and
special), a brass drift and wood block, and a soft-jaw
vise. See
Kits & Accessories.
- Carefully handle all parts. Before reassembly, examine
them for damage and wear.
- Disassemble and assemble tool components in a
straight line. Do NOT bend, cock, twist, or apply undue
force. Follow the disassembly and assembly procedures
in this manual; failure to do so could result in tool
damage.
- Have the appropriate
Spare Parts Service Kit
(
2012KIT
[for 2012],
2012VKIT
[for 2012B and
2012V]) available when servicing the tool; it includes
important perishable parts. Other components, as
experience dictates, should also be available. See
Kits
& Accessories.
- Apply Loctite
®
243 Threadlocker (
Huck P/N
508567
)
to gland threads. Apply Loctite
®
271-05 (
Huck P/N
503657
) to nuts and locknut (P/N
505420
); torque to
25–30 ft.-lbs.
- Smear
LUBRIPLATE
® 130-AA
(
Huck P/N
502723
) or
SUPER-O-LUBE
®
(Huck P/N
505476
) on
rings and
mating parts to ease assembly.
- Apply Threadmate
®
(Huck P/N
508517
) to pipe
threads and quick-connect fittings.
DAILY
The 2012 series requires a minimum amount of
maintenance. Regular inspection and correction of minor
problems will keep the tool operating efficiently and
prevent downtime.
- If a filter-regulator-lubricator unit is not being used,
uncouple the air disconnects and add a few drops of
hydraulic fluid or a light-weight oil to the air inlet of
the tool.
NOTE: If the tool is in continuous use, add
a few drops of oil in every 2–3 hours.
- Before connecting an air hose to the tool, clear the air
lines of dirt and water.
- Check all hoses and couplings for damage and air
leaks; tighten or replace if necessary.
- Check the tool and nose assembly for damage (cracks,
scoring, and springs) and air or hydraulic leaks; tighten,
repair, or replace if necessary.
- Inspect the tool, hoses, and Powerig during operation
to detect abnormal heating, leaks, or vibration.
- Inspect hydraulic pistons and piston rods for scored
surfaces, and excessive wear or damage; replace as
necessary.
- Clean nose assemblies in mineral spirits to clear jaws
and rinse metal chips and dirt. For a more thorough
cleaning, disassemble the nose assembly. Use a
pointed “pick” to remove imbedded particles from
the pull grooves of the jaws. Check gripper teeth for
damage.
Clean
all parts of any assembly with UNITIZED™ Jaws
in mineral spirits or isopropyl alcohol only; do not let
jaws come in contact with other solvents. Do not let
jaws soak; dry them
immediately
after cleaning. Huck
recommends drying other parts before re-assembling.
WEEKLY
- Disassemble, clean, and re-assemble nose assembly in
accordance with applicable instructions
.
- Check the tool and all connecting parts for damage
and
fluid/air leaks; tighten or replace if necessary
.
Maintenance
CAUTIONS:
Replace all seals, wipers, and rings when the
tool is disassembled for any reason, and at
regular intervals, depending on severity and
duration of use.
Do not use TEFLON
®
tape on pipe threads.
Tape can shred resulting in tool malfunction.
Slic-tite
®
is available in stick form (Huck P/N
503237).
CAUTION: Damaged jaw teeth, or debris
packed between teeth, will result in failure
to install fastener or improperly installed
fastener.