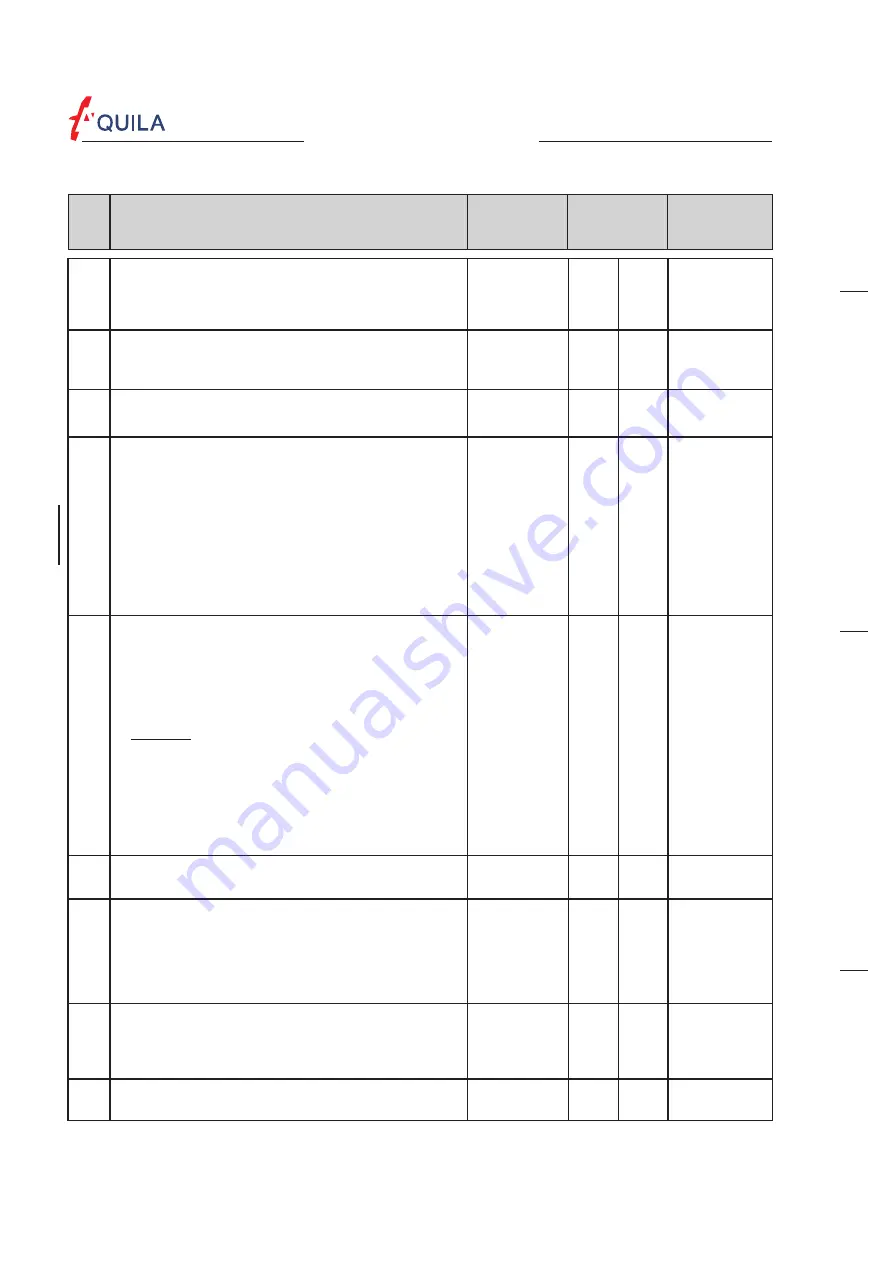
MAINTENANCE MANUAL
AQUILA AT01
A
1.
Engine cowling - Remove engine cowling. Check for cracks,
X
overheated areas, deformation, loose or missing fasteners.
Check condition of fire protect paint and heat resistance
shielding.
2)
1)
2.
Engine oil change - Remove oil drain screw from oil tank.
12-12-00
X
50h
Drain old oil and dispose in accordance with environmental
R912* 12-20-00 11)
regulations.
1)
3.
Oil tank - Check oil tank and clean if contaminated.
R912* 12-20-00 11)
X
200h
2)
1)
4.
Oil filter - Remove old oil filter from engine and install new
12-12-00
X
50h
oil filter. Lubricate mating sealing ring of new oil filter with
R912* 12-20-00 11)
engine oil. Tighten new oil filter by hand.
Cut open old oil filter without producing any metal chips and
inspect filter mat, filter cover, sealing lip, spring of bypass
valve (small) and positioning spring (large) for particles, wear
and missing material.
Findings:_____________________
2)
1)
5.
Oil change - Renew gasket ring of drain screw on oil tank.
12-12-00
X
50h
Tighten drain screw to 25 Nm (221 in.lbs).
R912* 12-10-00 4)
Refill oil tank with approx. 3 liters of oil. For oil quality, see
R912* 12-20-00 11)
Operators Manual and SI-912-016.
SI-912-010
SB-912-040
Refilled:______________Quantity:_______L
CAUTION:
DO NOT USE AIRCRAFT ENGINE OIL.
Due to the friction clutch and the high stresses
in the reduction gear 4-stroke motor cycle oils are
recommended. For suitable lubricants and oil change
intervals, see ROTAX Operators Manual and latest
appropriate ROTAX publications.
2)
1)
6.
Visual inspection of the magnetic plug for accumulation
R912* 12-20-00 12)
X
50h
of chips
7.
Check compression by differential pressure method.
R912* 12-20-00 5)
200h
Test pressure: 6 bar (appr. 6000 hPa / 87 psi)
Pressure drop: max. 25%
Cyl. 1 2 3 4
Pressure drop: _____ _____ _____ _____
2)
8.
Cooling air ducts, engine baffling and cylinder cooling
R912* 12-20-00 3)
X
fins - Check for obstructions, cracks, wear and general
SB-912-029
condition. Check for signs of abnormal temperatures.
Check crankcase for cracks.
2)
9.
Leakage bore at the base of the water pump - Check for
R912* 12-20-00 4)
X
signs of leakage.
Page 4
05-20-00
Maintenance Checks
No.
Engine
Reference
Interval
Initials
100h
other
1) If more than 30% of operation hours have been flown with leaded fuel e.g.: AVGAS 100LL
2) Check has to be carried out every 100 hours of operation or 12 month, whichever comes first.
16.09.19
Summary of Contents for AT01
Page 2: ...MAINTENANCE MANUAL AQUILA AT01 A ...
Page 4: ...MAINTENANCE MANUAL AQUILA AT01 A ...
Page 6: ...MAINTENANCE MANUAL AQUILA AT01 A ...
Page 9: ...MAINTENANCE MANUAL AQUILA AT01 A CHAPTER 5 TIME LIMITS MAINTENANCE CHECKS ...
Page 10: ...MAINTENANCE MANUAL AQUILA AT01 A ...
Page 12: ...MAINTENANCE MANUAL AQUILA AT01 A ...
Page 14: ...MAINTENANCE MANUAL AQUILA AT01 A ...
Page 18: ...MAINTENANCE MANUAL AQUILA AT01 A Maintenance Checks ...
Page 46: ...MAINTENANCE MANUAL AQUILA AT01 A Maintenance Checks ...