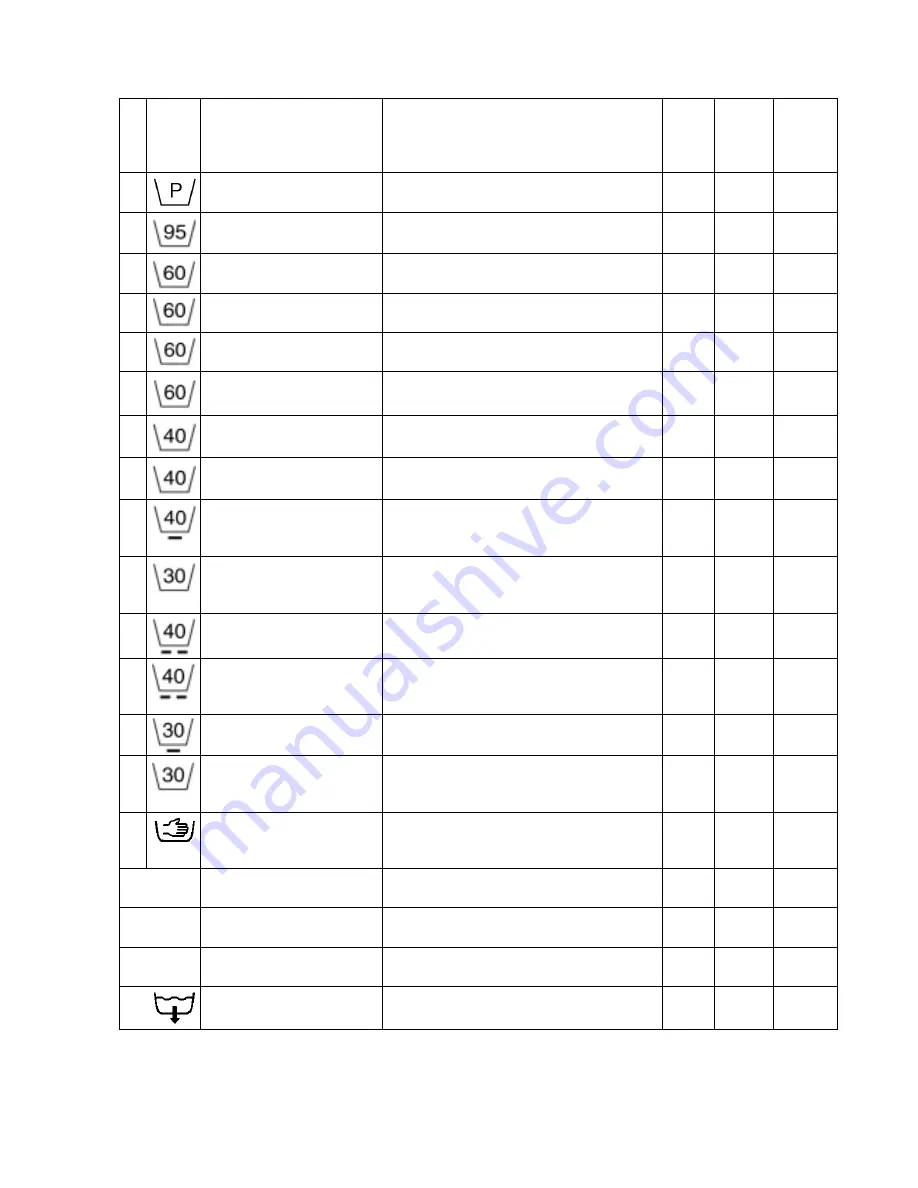
15
PROGRAMMES
COLD FILL MODELS
Wash
Label
Programme Type /
Fabric
Description
Temp
°C
Max
Load
(kg)
Approx
Prog.
Time
(h:min)
1
Prewash
Mixed
A cool temperature cycle to loosen stains
before selecting a main wash programme
30
6
0:25
2
Hygienic
White Cotton
For hard wearing heat resistant cotton
and linen
95
6
2:30
3
Super Wash
Colourfast Cotton
An intensive cleaning programme for
heavily soiled hard wearing fabrics
60
5
2:20
4
Everyday
Colourfast Cotton
For every day cleaning needs for
colourfast cotton or linen fabrics
60
5
1:30
5
Standard
Colourfast Cotton
An intensive cleaning, energy efficient
cycle using the maximum load capacity
60
6
2:00
5
Fast Wash
Colourfast Cotton
A fast cycle for lightly soiled heat resistant
cotton and linen fabrics
60
5
1:00
6
Everyday
Non-Colourfast Cotton
For the every day cleaning needs of
cottons and other hard wearing fabrics
40
5
1:15
6
Intensive
Non-Colourfast Cotton
A less energy efficient intensive 40°C
cycle for more stubborn soiling
40
6
1:45
7
Man Made Fibres
Coloured Synthetics &
Acrylics
A cycle designed to wash a variety of
man-made fibres and fibre mixtures
40
3
1:15
8
Cool Wash
Non Colourfast Cotton
Delivers the same performance as the
intensive 40°C cycle but it more energy
efficient at the expense of duration
30
4
1:50
9
Machine Washable
Wool
For machine washable wool and wool
mixtures
40
3
1:00
9
Gold Woolmark Approved
Handwash Wool
A special cycle for Hand Wash wool that
will not shrink your garments. Exclusively
approved by Woolmark
40
1
0:50
10
Machine Washable
Silk
For silk garments labelled as machine
washable
30
3
0:55
11
Fast Wash
Mixed
Not Wool, Silk/Handwash
A very short refresh programme for lightly
soiled mixed fabrics
30
3
0:30
12
Handwash
Delicates
Not Wool/Silk
A gentle cycle for delicate items labelled
as Hand Wash only
25
4
0:50
R&S
Rinse & Spin
Mixed
This partial programme completes two full
rinses and then a slow spin
-
3
0:30
FS
Fast Spin
Cotton
This partial programme completes the
maximum speed final spin
-
6
0:15
SS
Slow Spin
Delicates
This partial programme completes the
intermediate speed final spin
-
3
0:12
PO
Pump Out
All
This partial programme ensures the
appliance is emptied of water
-
6
0:02