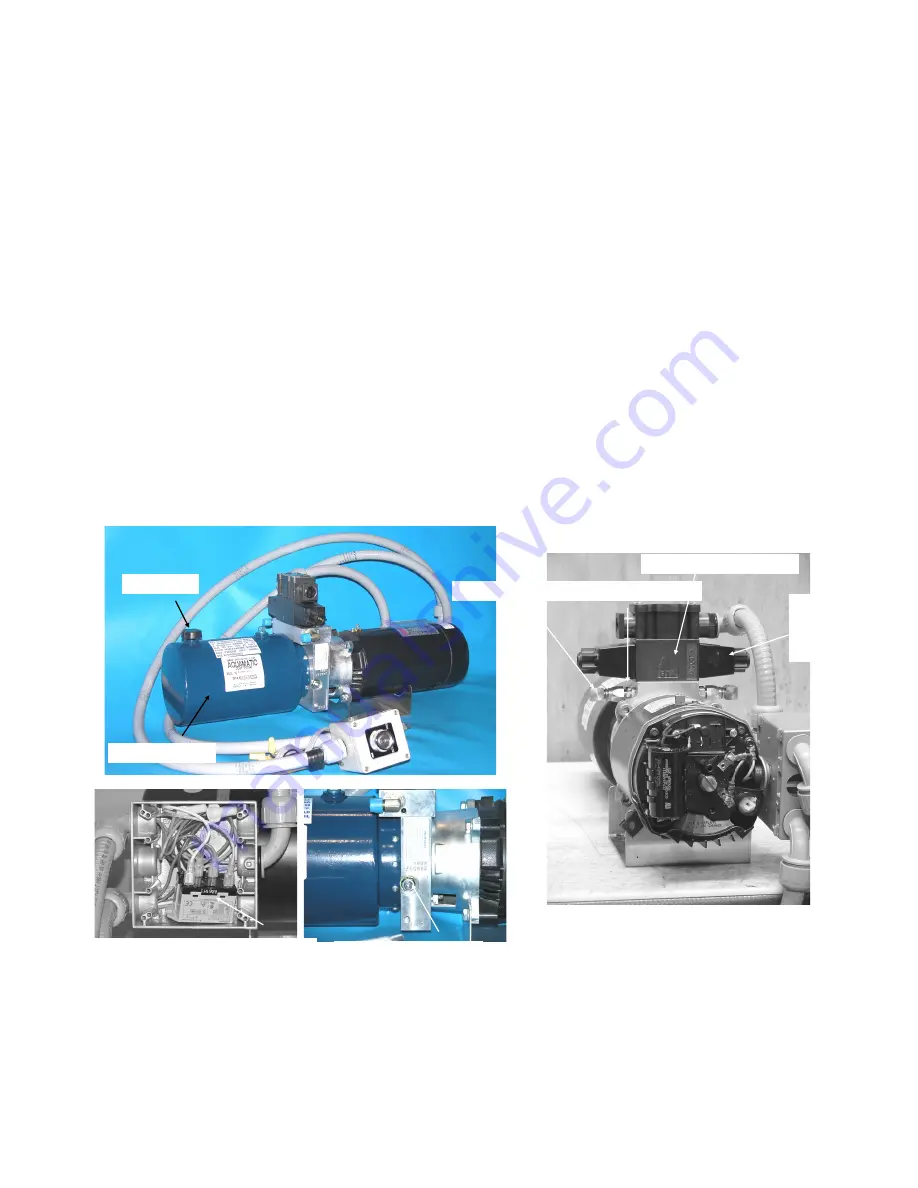
9
Hydraulic Pressure Adjustment
The amount of pressure that the powerpack (hydraulic pump) supplies to the hydraulic motors is more or less directly
related to the amount of torque or turning power that the motor can produce. Less pressure-less torque, more
pressure-more torque. Since you are using the pressure as a sensor to stop the cover when it reaches the end of travel
or meets an obstruction, you want to set the pressure just high enough to make the cover move, but low enough so
that it will stop when it meets an obstruction.
At the powerpack, there is an adjustable pressure relief valve. This is a spring-loaded screw valve, which will allow
hydraulic fluid to bypass back to the reservoir above a certain pressure setting. If the pressure needs to be adjusted,
refer to the following:
The pressure can be adjusted with a minimum amount of effort. The adjustment valve is located at the three o’clock
position, mid pack (looking from the tank end).
See diagram below.
Loosen the 9/16” nut with a socket. While
holding down the nut, screw the 3/16” Allen set screw in, to increase the pressure. This can be done by inserting the
Allen wrench through the end of the socket. Tighten the nut to reseal the adjustment. Make only small adjustments a
the time; 1/4 to 1/2 turns. Check to see that the cover operates in both directions without any hesitations.
Repeat adjustment if necessary.
It is very important to make sure that moisture and dirt stay out of the hydraulic fluid. Normally, the only place that it
might enter the system is through the powerpack’s fluid reservoir filler cap. Make sure that it is always on.
Dirt and
moisture can severely affect the life of the pump and hydraulic motors.
It
is
rec-
ommended that you arrange to have your fluid
changed at least every ten years to make sure that
the system remains in top condition. This can be done
simply by removing the filler cap of the reservoir and inverting the
powerpack to drain the old fluid. Pour the old fluid into an approved oil reclamation container. Replace the fluid
with automatic transmission fluid (Dexron type only). You may need approximately 3.5 quarts to fill the reservoir.
Run the system several times and repeat the draining and filling process as described above. Only fill the reservoir to
within 1-2 inch of the top to allow for fluid expansion
.
Filler Cap
Reservoir Tank
Valve Hose Fittings #516H & #515H
Solenoid
Magnet
#514H
Pressure Relief Valve
Solenoid Valve #513 H
Hydraulic Power Pack Relay #522H